Compacted Graphite Iron (CGI) represents a significant evolution in cast iron technology, blending the advantages of both traditional gray iron and ductile iron to create a material with superior mechanical properties. Unlike gray iron, which features flaky graphite structures, or ductile iron with spherical graphite, CGI’s unique microstructure consists of compacted, worm-like graphite. In this article, we will explore what CGI is, its key properties, composition, applications, and how it compares to other types of cast iron.
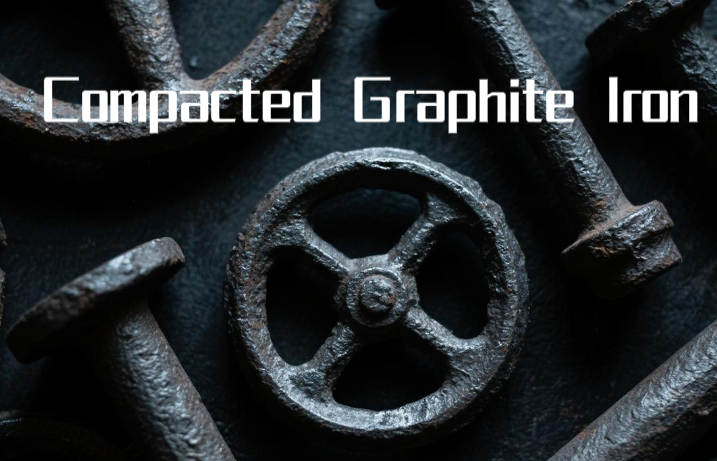
What is Compacted Graphite Iron?
Compacted Graphite Iron (CGI) is a type of cast iron where the carbon forms short, thick, worm-like graphite structures instead of the flakes seen in gray iron or the spheres in ductile iron. This unique graphite shape gives CGI mechanical properties that fall between gray iron and ductile iron — it is stronger and tougher than gray iron, but still maintains better thermal conductivity and vibration damping than ductile iron. Because of this balance, CGI is often used in applications like diesel engine blocks, turbocharger housings, and exhaust manifolds, where both strength and heat resistance are critical. It’s become especially important in modern automotive and heavy-duty industries aiming for lighter, more efficient engines without sacrificing durability.
Compacted Graphite Iron Properties
Compacted Graphite Iron (CGI) has a unique set of properties that make it suitable for high-performance applications. Here are the key properties of CGI:
Microstructure:
Compacted Graphite: The graphite structure is more compact and intermediate between flake graphite (found in gray iron) and spherical graphite (in ductile iron), which provides enhanced mechanical properties like strength and fatigue resistance.
Tensile Strength:
CGI offers higher tensile strength compared to gray iron, typically ranging from 400 to 600 MPa. This makes it suitable for components that need to withstand significant mechanical stress without cracking.
Hardness:
CGI generally has higher hardness than gray iron, improving its wear resistance. The hardness values typically range from 190 to 240 HB (Brinell hardness).
Fatigue Resistance:
Due to its unique microstructure, CGI exhibits improved fatigue resistance over gray iron, which is crucial for parts subjected to repeated stresses, such as engine blocks and cylinder heads.
Thermal Conductivity:
CGI has good thermal conductivity, though it is not as high as gray iron. This helps dissipate heat from high-temperature components, but it’s not as efficient as aluminum alloys in heat management.
Damping Capacity:
CGI has excellent vibration damping properties, which help reduce noise and vibration in engine components and contribute to smoother operation.
Wear Resistance:
CGI demonstrates superior wear resistance under high-stress and high-temperature conditions, particularly when compared to traditional gray iron. This makes it ideal for automotive and industrial applications that involve high wear rates.
Machinability:
Although more difficult to machine than gray iron, CGI can still be processed using standard machining techniques. However, the wear on tools can be higher compared to other iron alloys.
Density:
CGI is denser than ductile iron but generally lighter than gray iron, making it possible to reduce component weight while maintaining strength and durability.
Corrosion Resistance:
Similar to gray iron, CGI has moderate corrosion resistance, which makes it suitable for applications where exposure to environmental conditions like moisture and chemicals is not extreme.
Cost:
While CGI offers improved performance over gray iron, it can be more expensive due to the added complexity in processing and the cost of specific alloying elements. However, its longer lifespan and reduced material usage can offset the initial cost in many applications.
CGI Compositions
Compacted Graphite Iron (CGI) is a type of cast iron that has a unique microstructure characterized by compacted, rather than flake or nodular, graphite. Its composition is similar to that of other cast irons but with specific modifications to achieve the compacted graphite form. Here’s an overview of the typical composition of CGI:
- Carbon (C)
Range: 3.0% to 4.0%
Carbon is a key element in CGI, forming the graphite structure that gives the material its unique properties. The high carbon content is crucial for achieving the compacted graphite structure that distinguishes CGI from other forms of cast iron. - Silicon (Si)
Range: 1.5% to 3.0%
Silicon promotes the formation of graphite during casting, influencing the type of graphite structure formed. Higher silicon content helps in the formation of the compacted graphite, rather than a flake form. It also enhances the material’s fluidity during casting. - Manganese (Mn)
Range: 0.5% to 1.0%
Manganese helps deoxidize the molten iron and can improve the mechanical properties of CGI, including its strength and toughness. It also plays a role in controlling the solidification process and stabilizing the graphite structure. - Phosphorus (P)
Range: Typically less than 0.1%
Phosphorus is usually kept at low levels because high phosphorus content can lead to brittleness. Low levels help maintain the material’s strength and ductility. - Sulfur (S)
Range: Typically less than 0.02%
Sulfur can form iron sulfide during casting, which negatively affects the mechanical properties by weakening the structure. Low sulfur content is crucial for maintaining the material’s strength and machinability. - Magnesium (Mg)
Range: Typically not present in large amounts, but small amounts can be used in some formulations.
Magnesium is sometimes added to CGI in controlled amounts to modify the graphite structure or improve mechanical properties. It is not typically used to produce CGI, as it is more relevant to ductile iron. - Nickel (Ni)
Range: 0.5% to 2.5%
Nickel can be added to CGI to enhance its strength, ductility, and corrosion resistance. It is particularly used in applications where high toughness and resistance to wear are needed. - Chromium (Cr)
Range: 0.5% to 2.0%
Chromium is added to CGI to improve its resistance to wear, oxidation, and corrosion. This is particularly important in automotive applications where components are exposed to high temperatures and harsh conditions. - Copper (Cu)
Range: 0.2% to 2.0%
Copper can be added to improve the material’s resistance to corrosion and wear. It also helps in enhancing the material’s strength and machinability. - Other Alloying Elements
Boron (B): Small amounts of boron (around 0.005% to 0.05%) can be used to improve the hardenability and strength of CGI.
Titanium (Ti): Titanium, when used, helps in controlling the graphite formation and refining the grain structure.
Vanadium (V): Vanadium can be added for additional strength and hardness, particularly in high-performance applications.
Compacted Graphite Iron Grades
Compacted Graphite Iron (CGI) is available in various grades, each tailored to specific applications based on its unique properties. The grading system for CGI typically follows the ISO 1083 standard or similar regional standards, and the grades are categorized based on the tensile strength and characteristics of the material.
Common Compacted Graphite Iron (CGI) Grades:
CGI 400/18 (EN-GJS-400-18):
Tensile Strength: 400 MPa (58,000 psi)
Elongation: 18%
Properties: This grade provides good strength with excellent fatigue resistance and moderate ductility. It’s often used for applications requiring high strength and moderate wear resistance.
Applications: Engine blocks, cylinder heads, and other components subject to high thermal and mechanical stresses.
CGI 500/14 (EN-GJS-500-14):
Tensile Strength: 500 MPa (73,000 psi)
Elongation: 14%
Properties: A higher tensile strength compared to CGI 400/18, with improved wear resistance and good thermal conductivity. This grade strikes a balance between strength and ductility.
Applications: Used for more demanding applications, such as in automotive engine components, heavy-duty industrial machinery, and high-performance mechanical parts.
CGI 600/10 (EN-GJS-600-10):
Tensile Strength: 600 MPa (87,000 psi)
Elongation: 10%
Properties: Offers a higher tensile strength with slightly reduced elongation, which makes it suitable for high-strength applications where toughness and resistance to cracking are critical.
Applications: Heavy-duty engine components, structural parts in machinery, and high-load-bearing components in the automotive and industrial sectors.
CGI 700/04 (EN-GJS-700-04):
Tensile Strength: 700 MPa (102,000 psi)
Elongation: 4%
Properties: This grade provides very high tensile strength and is suitable for high-stress applications where the material must resist deformation. However, the elongation is low, which makes it more brittle.
Applications: Heavy machinery, automotive components subject to extreme stress, and specialized industrial equipment.
CGI 800/02 (EN-GJS-800-02):
Tensile Strength: 800 MPa (116,000 psi)
Elongation: 2%
Properties: A high-strength grade, used in very demanding applications where wear resistance and high strength are paramount. The low elongation indicates that it may not be suitable for highly dynamic or shock-loaded applications.
Applications: Used in high-performance applications such as turbine housings, powertrain components, and other critical machinery parts that require very high strength and durability.
Compacted Graphite Iron Applications
Compacted Graphite Iron (CGI) has a range of applications across various industries due to its unique combination of high strength, improved fatigue resistance, and excellent wear resistance. Its ability to withstand high thermal and mechanical stresses while being more lightweight than traditional cast iron makes it an attractive material choice in demanding applications. Here are some of the primary applications of cgi metal:
- Automotive Industry
CGI is extensively used in the automotive sector due to its superior mechanical properties, including high strength, good machinability, and fatigue resistance. Common applications include:
Engine Blocks: cgi metalis used in engine blocks for modern high-performance and heavy-duty engines, particularly in diesel engines. Its thermal conductivity helps in managing the heat from high-output engines.
Cylinder Heads: Some vehicle models use CGI for cylinder heads to improve strength and fatigue resistance under high stress, especially in turbocharged engines.
Exhaust Manifolds: Due to its excellent heat resistance and durability, CGI is often used for exhaust manifolds, which need to withstand high temperatures and thermal cycling.
Pistons and Crankshafts: In heavy-duty engines, CGI’s wear resistance helps in the production of pistons and crankshafts that operate in harsh conditions. - Heavy-Duty Machinery
Machine Components: CGI is used for components that need high strength and wear resistance in heavy-duty machinery, such as construction equipment, mining machinery, and agricultural machines. Components like gears, housings, and brake rotors benefit from CGI’s combination of durability and reduced weight compared to traditional materials.
Brake Discs: CGI is ideal for brake discs in heavy vehicles and machinery where high strength, heat resistance, and wear resistance are required. - Diesel Engine Components
Crankcases and Cylinder Liners: CGI is a popular material for diesel engine crankcases and cylinder liners, offering improved thermal conductivity and resistance to fatigue, which is essential for the long service life of these components.
Turbocharger Housings: The heat-resistant properties of CGI make it suitable for turbocharger housings that need to withstand high temperatures and cyclic loading.
- Power Generation Equipment
Turbine Housings: CGI is used in power generation equipment, particularly turbine housings, where high strength and resistance to thermal fatigue are critical. The material’s performance under high temperatures and pressure makes it suitable for such applications.
Pump Casings: The durability and wear resistance of CGI make it a suitable choice for pump casings used in power plants and other high-demand industrial sectors.
- Industrial Equipment
Heat Exchangers: CGI’s excellent thermal conductivity and resistance to thermal expansion make it an ideal choice for heat exchangers in industrial applications, where efficient heat transfer is crucial.
Compressor Housings: The wear resistance of CGI makes it an ideal material for compressor housings, which operate under high-pressure conditions and must endure constant mechanical stress.
- Marine Applications
Marine Engine Components: CGI is used in marine engines for components that need to withstand the harsh marine environment, such as cylinder heads and engine blocks. Its resistance to corrosion and high temperature makes it suitable for the unique conditions in marine operations. - Aerospace and Defense
Aircraft Components: CGI is sometimes used in certain aerospace and defense applications where strength, lightweight, and heat resistance are needed. For instance, parts of landing gears, frames, or structural supports in aircraft benefit from CGI’s mechanical properties. - Agricultural Equipment
Tractor Parts: CGI is also used in the agricultural industry for producing parts like engine blocks, axle housings, and other structural components that require strength and resistance to wear from prolonged use. - Industrial Pumps and Valves
Pump Components: CGI is used in industrial pumps for its wear resistance and strength, particularly in pumps handling harsh chemicals or abrasive materials.
Valve Bodies: The material’s excellent casting properties and durability make it ideal for valve bodies in high-pressure systems, ensuring long-term operational reliability. - Commercial and Industrial Heat Management
Heating Elements: Components used in high-temperature environments, such as commercial heating systems and industrial furnaces, use CGI for its heat resistance and low thermal expansion, helping with the overall energy efficiency and longevity of these systems.
Can you Weld Compacted Graphite Iron?
Welding Compacted Graphite Iron (CGI) is possible, but it presents certain challenges due to the material’s unique microstructure and properties. CGI combines the strength of gray iron with the benefits of graphite, which gives it enhanced thermal conductivity and strength, but also affects its weldability.
Welding Methods for CGI
Despite these challenges, CGI can be welded using the right techniques and precautions. Some of the most common welding methods used for CGI include:
-Preheating: To avoid thermal shock and cracking, it’s important to preheat the material before welding. The preheat temperature typically ranges from 300°F to 500°F (150°C to 260°C), depending on the thickness of the part. Preheating helps to reduce the thermal gradient and controls the cooling rate.
-Weld Filler Materials: Using the right welding filler material is crucial for successful welding. High-strength cast iron rods (such as Ni-Fe alloy rods) or Nickel-based alloys are often recommended for welding CGI. Nickel rods, in particular, help improve the weld’s strength, flexibility, and resistance to cracking.
-Shielded Metal Arc Welding (SMAW): This method, also known as stick welding, can be used for welding CGI, but care must be taken to control the heat input and minimize the risk of cracking. The use of nickel-based rods (e.g., Nickel 99) helps improve weld quality.
-Gas Metal Arc Welding (GMAW): This method is also known as MIG welding and can be used for CGI with the correct filler material. It is suitable for thinner sections but may require more precise heat control.
-Gas Tungsten Arc Welding (GTAW): Known as TIG welding, this method offers high control over the heat input and is ideal for smaller or more delicate welding tasks. TIG welding is suitable for more precise applications, though it is slower than other methods.
How’s the Compacted Graphite Iron Market?
The compacted graphite iron market is experiencing steady growth, driven by increasing demand in various industries such as automotive, aerospace, and manufacturing due to CGI’s superior mechanical properties, including enhanced strength and thermal conductivity compared to traditional cast iron. The rising focus on lightweight materials for fuel efficiency and performance improvements in vehicles further propels the market. Additionally, technological advancements in casting processes and rising applications in high-performance engine components are contributing to the market’s expansion. However, challenges such as fluctuating raw material prices and environmental regulations may impact growth in the short term. Overall, the CGI market is expected to continue its upward trajectory as industries seek innovative materials for improved performance and sustainability.
Compacted Graphite Iron vs Cast Iron, What’s the Difference?
Compacted Graphite Iron (CGI) and Cast Iron are both iron alloys, but they differ significantly in their composition, microstructure, properties, and applications. Here’s a comparison of the two:
- Microstructure:
Cast Iron: Cast iron has a graphite microstructure that typically forms in flake shapes. This is referred to as gray iron when the graphite is in a flake form. The flakes of graphite reduce the material’s strength and make it more brittle.
Compacted Graphite Iron (CGI): In CGI, the graphite takes on a compacted or vermicular (worm-like) shape rather than forming in flakes. This microstructure offers a balance between the properties of cast iron and steel, combining the advantages of both. - Mechanical Properties:
Cast Iron: Due to its flaky graphite structure, cast iron typically has good castability, excellent machinability, and high damping capacity, but it tends to be brittle and has lower tensile strength compared to CGI. Cast iron is also known for its good wear resistance.
Compacted Graphite Iron (CGI): CGI retains many of the benefits of cast iron, such as excellent castability and machinability, but its compacted graphite structure significantly improves its tensile strength, fatigue resistance, and thermal conductivity. CGI is also less brittle than conventional cast iron, making it more durable and tougher in high-stress applications. - Strength and Durability:
Cast Iron: Cast iron generally has a lower tensile strength (around 200-300 MPa) and is more prone to cracking under stress. It excels in applications where low-to-moderate stress and vibration dampening are required.
Compacted Graphite Iron (CGI): CGI offers significantly higher tensile strength (ranging from 400 MPa to 800 MPa) and greater resistance to fatigue and thermal shock. This makes CGI ideal for high-stress applications such as engine blocks, cylinder heads, and other automotive or industrial components. - Thermal Properties:
Cast Iron: Gray cast iron is known for excellent thermal conductivity and good damping properties due to the presence of graphite flakes, which helps absorb vibrations.
Compacted Graphite Iron (CGI): CGI has better thermal conductivity than traditional cast iron, thanks to its compacted graphite structure. It also has better resistance to thermal cycling, which allows CGI to maintain its properties at elevated temperatures, making it suitable for applications involving high heat and thermal stress, such as in engine components.
- Ductility and Elongation:
Cast Iron: Due to the flake-like structure of the graphite, cast iron is less ductile and has lower elongation. It is prone to cracking under tensile stress.
Compacted Graphite Iron (CGI): CGI is more ductile and has a higher elongation compared to cast iron. The compacted shape of the graphite gives it improved impact resistance and toughness, which helps prevent cracking under stress. - Applications:
Cast Iron: Cast iron is commonly used in applications where weight, machinability, and cost-effectiveness are more important than high strength. Examples include pipes, machinery parts, furnace parts, and cookware.
Compacted Graphite Iron (CGI): CGI is used in high-performance applications where strength, fatigue resistance, and thermal properties are crucial. Common applications include automotive engine blocks, cylinder heads, heavy-duty machinery, and turbine housings. - Cost:
Cast Iron: Cast iron is less expensive to produce due to its simpler processing requirements. It is more cost-effective for applications where high strength is not a priority.
Compacted Graphite Iron (CGI): CGI tends to be more expensive to produce due to the specialized processes involved in controlling the graphite structure. However, the additional cost is often justified by the performance benefits, especially in high-performance automotive and industrial applications. - Weight:
Cast Iron: Cast iron is typically heavier due to its dense structure and higher carbon content.
Compacted Graphite Iron (CGI): CGI can be lighter than traditional cast iron for similar strength levels, which is especially beneficial in automotive applications where reducing weight is crucial for performance and fuel efficiency.
Differences between Compacted Graphite Iron (CGI) and Cast Iron (Gray and Ductile types)
Property | Compacted Graphite Iron (CGI) | Gray Cast Iron | Ductile Cast Iron |
---|---|---|---|
Graphite Shape | Worm-like/vermicular | Flake-like | Spheroidal (nodular) |
Tensile Strength | 400–700 MPa | 150–300 MPa | 400–600+ MPa |
Ductility (Elongation) | Moderate (1–3%) | Very low (<1%) | Good (10–18%) |
Thermal Conductivity | Moderate (~25–50 W/m·K) | High (~50–80 W/m·K) | Lower than gray iron (~30–50 W/m·K) |
Fatigue Resistance | Good | Poor | Excellent |
Vibration Damping | Moderate | Excellent | Moderate |
Machinability | Moderate (harder than gray) | Excellent | Moderate |
Wear Resistance | High | Moderate | Good |
Density | ~7.1–7.3 g/cm³ | ~7.1 g/cm³ | ~7.0–7.3 g/cm³ |
Castability | Lower than gray iron | Excellent | Good |
Common Applications | Diesel engine blocks, turbo housings, brake parts | Machine bases, cookware, pipes | Gears, crankshafts, suspension parts |
Production Cost | Higher than gray/ductile iron | Low | Moderate |
Main Advantage | Balance of strength, stiffness & thermal resistance | Great damping & castability | Strength with ductility |