Malleable cast iron is a versatile and highly durable material, known for its unique blend of strength, flexibility, and machinability. Unlike traditional cast iron, which is often brittle and prone to cracking, malleable cast iron undergoes a specialized heat treatment process that transforms its structure, enhancing its toughness and ability to withstand impact. In this article, we will explore the key characteristics of malleable cast iron, how it is produced, its properties, applications, and how it compares cast iron.
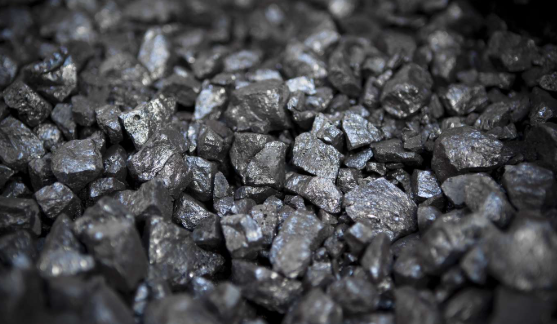
What is Malleable Iron?
Malleable cast iron is a type of cast iron that has been heat-treated to transform its brittle structure into a more ductile and flexible material. It is produced by first casting white iron—which is very hard and brittle—and then annealing it at high temperatures for an extended period. This heat treatment breaks down the cementite (iron carbide) into small, rounded particles of graphite known as temper carbon, giving the iron improved toughness, machinability, and the ability to deform without breaking. Malleable cast iron is commonly used for applications like pipe fittings, brackets, and small automotive parts where moderate strength and ductility are required.
Advantages of Malleable Cast Iron
Malleable Iron Castings are a type of iron produced through a specialized heat treatment process that converts white iron into a more ductile and machinable form. It is characterized by its excellent combination of strength, ductility, and impact resistance, making it suitable for applications requiring both durability and the ability to withstand shock or vibration. The material exhibits good wear resistance and can be easily machined, welded, and fabricated, though it is not as strong as steel. Its microstructure consists of tempered carbon (temper carbon) in a ferritic or pearlitic matrix, which contributes to its unique mechanical properties
How Malleable Cast Iron is Produced?
1. Casting White Iron
The process starts by casting the component using white cast iron, which is rich in carbon and has a microstructure full of iron carbides (Fe₃C). These carbides make it extremely hard, but also very brittle.
2. Annealing (Heat Treatment)
The white iron castings are then subjected to annealing, a long, controlled heating process, in two main stages:
First Stage – Decarburization (Optional for some types): Castings are heated to around 850–950°C (1560–1740°F) in an oxidizing atmosphere. This breaks down some cementite (Fe₃C) and allows carbon to escape as gas, reducing brittleness.
Second Stage – Graphitization: The castings are slowly cooled over many hours or days. Remaining cementite decomposes into ferrite or pearlite matrix and temper carbon nodules (rounded graphite particles).
3. Resulting Microstructure
The final material has a ferritic or pearlitic matrix (depending on cooling conditions).It contains rounded graphite nodules, called temper carbon, which improve ductility and impact resistance.
Final Product
The end result is a strong, machinable, and ductile metal—malleable cast iron—suitable for demanding structural and mechanical applications such as pipe fittings, automotive parts, and industrial tools.
What are Malleable Iron Properties?
Mechanical malleable iron properties:
Tensile Strength: ~350–450 MPa (can vary by grade)
Yield Strength: ~250–300 MPa
Elongation: ~5–15% (good ductility for cast iron)
Hardness: ~130–180 Brinell (can be higher for heat-treated grades)
Impact Resistance: Higher than gray cast iron due to its ductility
Physical Properties:
Density: ~7.2 g/cm³
Melting Point: ~1260–1300°C
Thermal Conductivity: ~25–50 W/m·K
Electrical Conductivity: Lower than steel but adequate for structural uses
Machinability: Good, especially compared to gray or white iron
Malleable Iron Castings Applications
Pipe Fittings: Used in plumbing, gas, and steam systems for elbows, tees, unions, and couplings due to their strength and leak resistance.
Automotive Components: Ideal for parts like brackets, differential housings, steering components, and suspension systems because of their toughness and durability.
Hand Tools and Hardware: Wrenches, clamps, and vises are often made from malleable iron because it offers a balance of strength and machinability.
Construction and Agricultural Equipment: Used in clamps, connectors, levers, and housings that need to endure rough use and repeated stress.
Railroad Industry: Couplings, brake shoes, and other structural hardware benefit from the impact resistance of malleable iron.
Electrical Fittings: Conduits, junction boxes, and hardware that need to protect electrical systems while being mechanically robust.
General Industrial Machinery: Used for gears, levers, and connecting parts where both flexibility and strength are necessary.
Malleable Cast Iron Compositions
Element | Content (%) | Purpose |
Carbon (C) | 2.0 – 2.7% | Provides castability; transformed into temper carbon after annealing |
Silicon (Si) | 0.9 – 1.6% | Promotes graphite formation and improves machinability |
Manganese (Mn) | 0.15 – 1.2% | Increases hardness and strength; too much can form carbides |
Sulfur (S) | ≤ 0.15% (ideally low) | Can make iron brittle; kept minimal |
Phosphorus (P) | ≤ 0.2% | Improves fluidity but reduces toughness |
Iron (Fe) | Balance | Main base metal |
Does Malleable Iron Rust?
Yes, malleable iron can rust because it is primarily composed of iron, which naturally oxidizes when exposed to moisture and oxygen. Like other types of cast iron and steel, malleable iron lacks inherent corrosion resistance, making it vulnerable to rust over time—especially in humid or outdoor environments. However, rusting can be significantly reduced or prevented through protective coatings such as galvanization (zinc coating), painting, or plating, and by using it in environments where it is not constantly exposed to water or corrosive elements.
Malleable Iron vs Cast Iron, Which is Better?
While malleable iron and cast iron are both iron-carbon alloys, they differ significantly in their structure, properties, and applications due to variations in composition and heat treatment.
1. Composition & Structure
Cast Iron (typically gray or white iron) contains 2.0–4.0% carbon and 1.0–3.0% silicon. In gray cast iron, carbon forms graphite flakes, making it brittle but good at damping vibrations. White cast iron has carbon in cementite (Fe₃C) form, making it extremely hard and brittle.
Malleable Iron starts as white iron but is heat-treated (annealed) to transform the carbon into small rounded graphite particles called temper carbon, resulting in a more ductile and impact-resistant material.
2. Mechanical Properties
Property | Malleable Iron | Gray Cast Iron |
Tensile Strength | Higher (350–450 MPa) | Lower (150–300 MPa) |
Ductility | High (can bend before breaking) | Very low (brittle) |
Impact Resistance | Good | Poor |
Machinability | Good | Good (better than white iron) |
3. Applications
Malleable Iron is used where strength and flexibility are essential — pipe fittings, automotive parts, hand tools, and railway hardware.
Cast Iron (Gray/White) is used where vibration damping, compressive strength, or wear resistance are more important — engine blocks, machine bases, cookware, and brake rotors.
The Differences Between Malleable Cast Iron and Cast Iron
Malleable iron is tough, ductile, and shock-resistant, ideal for mechanical parts that need to endure stress. Cast iron (especially gray iron) is brittle but strong in compression and excellent for static, non-impact uses. So, if you’re choosing between them: pick malleable iron when you need durability and flexibility, and gray cast iron when you need rigidity and vibration damping.
Feature | Malleable Cast Iron | Cast Iron (Gray/White) |
Heat Treated? | Yes (annealed white iron) | No (cast and cooled) |
Graphite Form | Rounded nodules (temper carbon) | Flakes (gray) or none (white) |
Strength and Toughness | Higher | Lower |
Cost | Slightly more expensive | Economical and easy to cast |