How To Distinguish Cast Components And Forged Components | Casting Vs Forging
China has become an international production base of castings and forgings (including die-casting parts, ordinary castings, forgings, etc.), which are produced in Europe, the United States, Japan, South Korea and other countries and regions. Australia has already transferred its original or newly developed products to China, which has typical cost and technology advantages. There are two blank forming processes. The blanks they produce are very similar in appearance. Not very good professionals are not easy to separate. This is die casting and forging (liquid forging). In this guide, we discuss how to distinguish between cast components and forged components & how to compare casting & forging.
Read more: Difference Between Casting and Forging
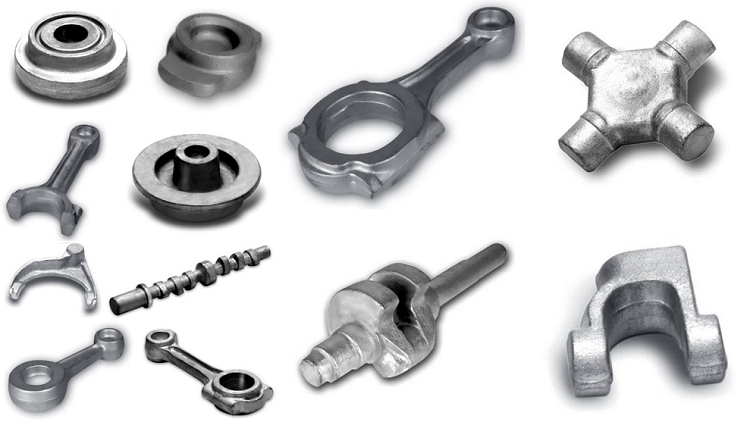
How To Distinguish Between Cast Components And Forged Components
1. It is recommended to distinguish between casting and forging, at least for two types of manufacturers: firstly, some intermediate mechanisms in China, including parts and the entire manufacturer. They take on parts and then find some manufacturers in the country to make them. Because of the different production process of these two gaps, the current market price is different, and the latter is generally higher than the former. If we do not distinguish the two gaps, if we press the low price of castings when accepting business quotation, we will have operation errors, which will affect the income and even loss. Secondly, Professional foundry and forging manufacturers. Because the latter is a part of die casting, it can be produced through traditional die casting technology and the business is taken over. After the die casting mold is opened, the blank produced in the die casting process basically has shrinkage, shrinkage defect or appearance defect, and the blank is unqualified, which eventually causes the improper loss.
2. The relationship between die-casting and press-forging, liquid die forging, continuous casting, and forging processes and the essence of the forging process are in one piece of equipment. In the same set of molds, casting filling and forging are continuously completed. The continuous casting and forging process is not a new process, and its principles have a long history. The most typical and simplest continuous casting forging process is the common liquid die forging (melt forging) process. Visually speaking, the die-casting forging process is a liquid die-forging process, which is as complex as traditional die-casting parts, and has specialized equipment with a high degree of automation. Because of this, it is not easy to separate die casting forgings from ordinary die casting parts. Similar to the quality of the blank produced in the continuous casting forging process, it is a process of “casting first and then forging”. The first type of casting and forging process is very common: rough machining requires two sets of molds, one for manual metal mold casting, and the other for precision forging using a friction machine or hydraulic press.
3. Die casting forging process is a process completed on a special die casting mold forging machine. The basic technology is: the metal liquid is first filled into the cavity of the mold by low-speed or high-speed casting. The mold has a movable cavity surface, which is pressed and forged with the cooling process of molten metal, thus eliminating a blank. Loose defects will also lead to the internal structure of the blank to reach the broken grains of forging. The overall mechanical properties of the blank have been significantly improved. In addition, the blank produced by this process has an external surface finish of 7 (Ra1.6), such as cold extrusion process or machined surface, with metallic luster.
Another advantage of die casting and forging process is that in addition to traditional casting materials, it can also produce deformation alloy and forging alloy to produce highly complex parts. These alloy grades include: hard aluminum, super hard aluminum alloy, forged aluminum alloy, such as LY11, LY12, 6061, 6061, LYC, LD, etc.). The tensile strength of these materials is almost twice that of ordinary cast alloys. It is more active in aluminum alloy automotive wheels, frames and other components and is expected to produce higher strength and impact resistant materials.
4. How to distinguish the two blank and appearance, it is difficult to distinguish the blank generated by the two processes. If you see a machined part, it’s more difficult to distinguish. Therefore, we can only reverse analysis and judgment: first, die casting parts are generally “structural parts”, while die casting forgings are “functional parts”“ Structural components “correspond to” functional components “. The latter generally refers to impact, high temperature, pressure, strength, surface treatment (such as anodizing) and heat treatment (solid solution strengthening). Typical products include engine block, wheel hub, piston, connecting rod, brake pad, pneumatic valve body or hydraulic valve body. The former is like a door frame, an instrument panel, an engine hood, etc. Second, judging from the material composition. Because die casting is usually cast alloy, for other grades of alloy, they are usually produced by die casting and die forging. The third is to judge the processing requirements of the outer surface blank.
For example, for aluminum die casting parts, due to the silicon and the blank produced in the die casting process, there are micropores (commonly known as “water particles”) on the outer surface, while the surface material will have “black spots” after anodization. Therefore, if the blank is anodized, the blank is not produced by ordinary die casting process. The fourth is judging from metallographic structure. Die casting parts and forgings are easily distinguished in metallography. The former is dendritic cast structure, while the latter is forged structure with uniform fracture grains.
5. Remove some misunderstandings. First of all, we can not think of the vacuum infiltration after die casting to solve the shrinkage and shrinkage defects in die casting. It can not be considered that vacuum die casting process can be used to produce continuous casting and forging process. Here comes the function. When technology advances, we must have a scientific thought and an attitude of keeping pace with the times. Second, the vacuum die casting has the same shrinkage and shrinkage defects as the common die casting; Vacuum die casting, which is more effective than ordinary die casting, can assist the metal liquid phase shrinkage and shrinkage caused by exhaust gas and shrinkage hole. There is no way. Third, the most common mistake made by professionals is that, although it is well known that this blank cannot be produced by ordinary die casting process, it is a process called “reverse punch indirect and partial extrusion”. They think that this process has the same effect as the liquid forging process, which is totally wrong“ The essence of “reverse punch extrusion” process is still a die casting process! Only that kind of “full projection area forging” is the real liquid forging process.