Cast vs Forged - Difference Between Casting and Forging | Diecasting-mould
Casting and forging are two very different manufacturing technologies, when we are faced with which one to choose, we should understand each process including their principle, features, advantages, shortcomings, and applications. Here we are going to explore cast vs forged, what’s the difference between casting and forging, as well as what is forging and what is casting.
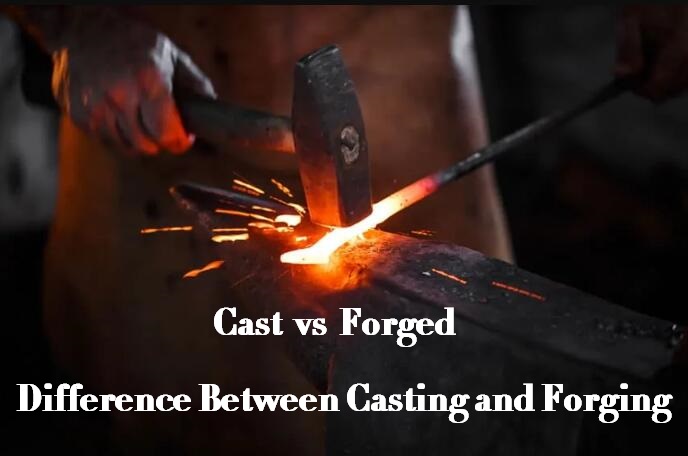
What is Casting?
Casting is a manufacturing process in which a liquid material poured into a mold with a hollow cavity of the desired shape, then the liquid material solidifies in the mold to form the part with a shape same as the cavity, the solidified part called casting, it is ejected or broken out of the mold to finish the casting process. The casting process suits various purposes and applications, especially large, complicated, and intricate components. A wide range of die casting parts is provided at Junying.
Advantages of Casting:
– A wide range of materials for selection (aluminum, zinc, magnesium, copper, etc.)
– Suitable for producing more complex and intricate parts
– Die cast parts are more refined and defined
– The casting process can be completed at a faster speed and greater volumes
– Custom alloys can be added at the molten stage
– No strict limitations in casting size
What is Forging?
Forging is a manufacturing process that shapes the metal using heat, and compressive and percussive force. A hammer or a die strikes the metal to deliver the blows and shape the part into the desired geometry. At the same time, the pounding action of forging will cause unbroken grain flow, which allows the metal to retain its strength. Forged metal offers a stronger structure than castings and plates, the uniformity of composition is also higher. Forging is often classified as cold forging, warm forging, and hot forging based on the temperature at which it is performed. Cold forging is done with the metal at room temperature. In forging, the metal may be heated as well. When forging is performed with metal heated to above room temperature and below the recrystallization temperature, that is warm forging. When the metal is heated to above recrystallization temperature, that is hot forging.
Advantages of Forging:
– Forged parts are denser and mechanically stronger
– High resistance to impact and wear
– Reduced porosity and cavity defects
– Tight grain structure in forged metal
Difference Between Casting and Forging - Cast vs Forged
What’s the difference between die casting and forging and which one to choose? When it comes to the selection of manufacturing methods, let’s get into the comparison between forging and casting.
1. Casting is a process that involves heating metal and pouring the molten metal into a mold, while in forging when the energy or force is applied to the metal, it is shaped always in a solid state.
2. Forged parts are stronger than castings. That means, the forging process offers a stronger end product than casting. During the die casting or casting process, the metal is heated to a molten state, so the grain is free to expand, which results in the final product has a more random grain structure. This will cause a decreased strength. On the contrary, the force from forging keeps the grain structure tight and makes the final product stronger.
3. Forge parts allow for much greater deformation before failure than cast parts.
4. Forging has limitations in product sizes, it’s more difficult to shape solid metal. While with casting, complex casting parts can be easily fabricated.
5. Generally, casting is cheaper than forging. Die casting tooling is also less expensive than forge dies because they withstand lower force.
6. In metal forging, the solid metal is pushed into an open die to form the shape, while in die casting, the molten metal is forced into a fully enclosed die under pressure.
7. Forgings normally have less surface porosity, finer grain structure, higher tensile strength, better fatigue strength, and greater ductility than castings. Forged parts had a 26% higher tensile strength than the same cast parts.
8. Forgings are often made from iron, steel, and titanium that is not possible in die casting, while castings can be made of aluminum, magnesium, zinc, copper, and more alloys.