The gating system functions in the filling process in casting, and the design of the gating system will affect the casting quality. So today we are going talk about what is a gating system and its essential components, uses, and purposes, as well as the factors affecting gating systems.
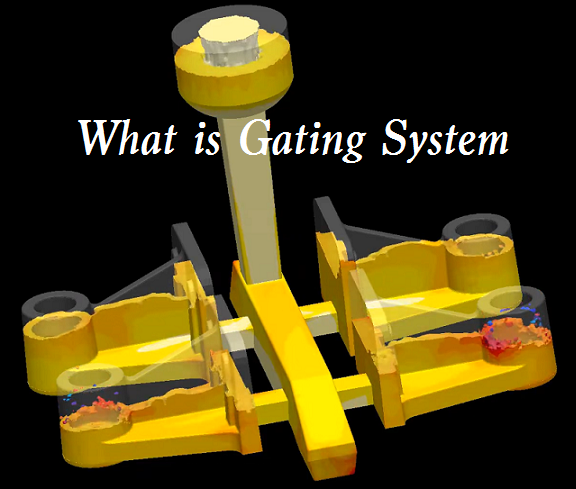
What is Gating System?
The gating system in casting is a structure with all channels through which molten metal passes and enters the mold cavity. There are three main types of gates, including vertical gating system, bottom gating system, and horizontal gating system. A good gating system should be able to ensure proper distribution of molten metal without excessive temperature loss, turbulence, gas entrapping, and slags, so it is important to consider some factors when designing the gating system, such as the metal composition, pouring cup dimensions, runner types, etc.
Elements & Components of Gating System
– Pouring basin: collects poured molten metal, prevents mold erosion, and prevents slag and other impurities from entering the mold cavity.
– Sprue: leads the molten metal from the pouring cup to the sprue well.
– Sprue Well: changes the direction of metal flow and passes it to the runner.
– Runner: takes the metal liquid from sprue to the ingates of casting. There are straight runners, tapered runners, uniform-size runners, and more.
– Slag trap: filters the slag when molten metal moves from runner and ingate.
Uses of Gating System
– Fill the mold cavity completely
– Avoid erosion
– Remove inclusions
– Regulate flow
– Minimize turbulence
– Trap containments
– Get directional solidification
– Save material
Purposes of Gating System
– Clean the metal: the cavity must be filled with a clean metal so that it prevents the entry of slag and inclusions into the mold cavity, which in turn minimizes the surface instability.
– Smooth filling process: a smooth filling in casting will help to reduce the bulk turbulence.
– Uniform filling: a uniform filling means that the casting is filled in the right manner.
– Complete filling: makes the metal thin with minimum resistance at the end sections.
What Factors Affect the Gating System?
– Type and size of runner and sprue
– Pouring rate
– Mold position during pouring and solidification
– Temperature and fluidity of the metal
– Location and sizes of gates that connect runner and casting
– Type of pouring equipment
Design Tips for Gating System
1) The cavity layout and gate opening position shall be symmetrical as far as possible to prevent the overflow phenomenon caused by the eccentric load of the mold.
2) The arrangement of cavities and gates should minimize the overall dimensions of the mold.
3) The system flow passage shall be as short as possible, with appropriate section size, as far as possible to reduce bending, and the surface roughness shall be low to minimize heat and pressure loss,
4) For multiple cavities, the material melt shall enter the depths and corners of each cavity at the same time as much as possible, and the splitter channel shall be arranged as balanced as possible.
5) On the premise that the mold cavity is full, the volume of the gating system shall be as small as possible to reduce material consumption.
6) The gate position shall be appropriate to avoid impacting the inserts and small and fine cores as much as possible and to prevent the core from deforming. The residual mark of the gate shall not affect the appearance of the parts.