Zinc Vs Aluminum Alloy - What’s The Difference Between Aluminum And Zinc Die Casting
How to tell the difference between zinc and aluminum alloy for die casting service?
Die casting is one of the most cost-effective, accurate and versatile manufacturing processes in the world today. The main field of die casting industry can be divided into zinc alloy die casting and aluminum alloy die casting, which are widely used in recent years. Then do you know the difference between zinc and aluminum alloys? You’ve come to the right place! Here at Die-casting Mould, we will discuss the difference between zinc and aluminum alloys and comparison of zinc die casting & aluminum die casting. If you want to know more information, make sure to continue reading below!
What Is Zinc Alloy
Zinc alloy is an alloy composed of zinc based on adding other elements. The common alloy elements are aluminum, copper, magnesium, cadmium, lead, titanium and other low-temperature zinc alloys. Zinc alloy has a low melting point, good fluidity, easy to weld, braze, and plastic processing, corrosion resistance in the atmosphere, and easy recycling and remelting of residual waste; but its creep strength is low and natural aging is easy to cause dimensional changes. Prepared by melting method, die-casting or pressure-processed into material. According to the manufacturing process, it can be divided into cast zinc alloy and deformed zinc alloy. It can be used for die-casting instrument, auto parts shell electric pole surface galvanized anti-corrosion, boiler water wall pipe hot dip galvanizing treatment to improve high temperature corrosion resistance, etc.
Features of zinc alloy:
● Relatively large.
● Good casting performance, can die-cast precision parts with complex shapes and thin walls, and the surface of the castings is smooth.
● Can be used for surface treatment: electroplating, spraying, painting, polishing, grinding, etc.
● When melting and die casting, it does not absorb iron, does not corrode the pressure, and does not stick to the mold.
● It has good mechanical properties and wear resistance at room temperature.
● Low melting point, melting at 385℃, easy to die casting.
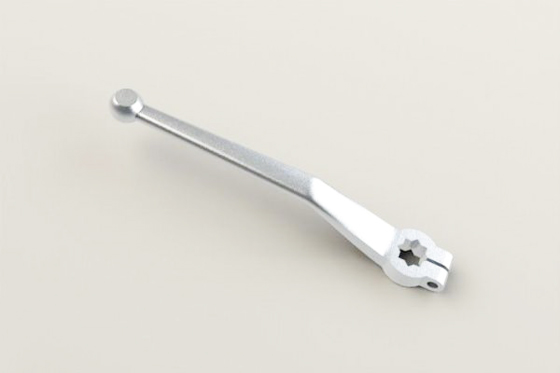
What Is Aluminum Alloy
Aluminum alloy is the general term of aluminum based alloys. The main alloy elements are copper, silicon, magnesium, zinc, manganese, and the secondary alloy elements are nickel, iron, titanium, chromium, lithium, etc. Aluminum alloy has low density but relatively high strength, close to or exceeds high-quality steel, good plasticity, and can be processed into various profiles. It is a type of non-ferrous metal structural material widely used in industry. It is used in aviation, aerospace, automobile, machinery manufacturing, A large number of applications in the ship and chemical industry.
Features of aluminum alloy:
● High thermal conductivity.
● Environmentally friendly.
● Low temperature resistance.
● Heat treatment can be used to obtain good mechanical properties, physical properties and corrosion resistance.
● High strength.
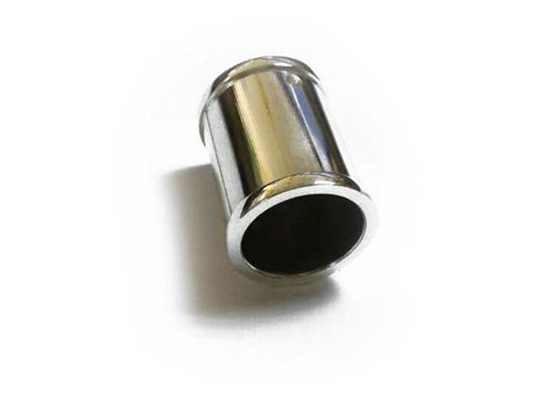
Aluminum Vs Zinc Alloy – What’s The Difference Between Zinc And Aluminum Alloy
1. Material
The zinc alloy material has a high specific gravity and good casting performance. Zinc alloy material has high density and high strength, which is close to or exceeds that of high-quality steel. In general, the zinc alloy die casting part is heavier than the aluminum alloy die casting.
2. Property
Zinc alloy material has a low melting point, has good mechanical properties and wear resistance, and can be used for surface treatment. The aluminum alloy has excellent electrical conductivity, thermal conductivity and corrosion resistance. The difference in performance lies in the different requirements of the products they apply, so we can choose the material of the die casting according to the required performance of the product.
3. Die casting process
● The melting temperature of the two alloys is different. Zinc alloy is more than 400 degrees, and aluminum alloy is more than 700 degrees.
● Different processing equipment, although called die casting machine, but can not be universal.
● Processing technology and parameters are different.
The above points are the biggest difference between zinc alloy die casting and aluminum alloy die casting (zinc alloy vs aluminum). The difference between the two also determines the scope of application and which products are more practical.
Which To Choose For Your Die Cast Project, Aluminum Alloy Or Zinc Alloy?
The price of zinc alloy is close to that of aluminum alloy. If the structure and die casting process permit, it is cost-effective to use aluminum alloy. The proportion of zinc alloy is about 2.5 times of that of aluminum alloy, and the price is the same. Therefore, the material cost of zinc alloy is two or three times higher than that of aluminum alloy. Now many enterprises want to replace zinc alloy with aluminum alloy in order to save cost, but some cannot be replaced because the strength, hardness and molding performance of zinc alloy are much better than aluminum alloy. If you want to polish the surface of the product electroplating, and require a high appearance quality, it has to use zinc alloy. Aluminum alloy material is difficult to meet the high surface quality requirements, because the aluminum alloy die casting molding performance is poor, the product surface is easy to have a lot of pores, and the surface quality is poor after electroplating.
It is not always easy to select the right alloy for your project. Need a hand? With over 10 years of die casting expertise, our team of experienced engineers will evaluate your requirements to help you decide which would be the best alloy option for your application to achieve the desired result for your part. Contact Die-casting Mould to get started on your next project today!