Zinc Die Casting Surface Finish Processes - Polishing, Sand Blasting, Anodizing | Diecasting-Mould
As we all know, the casting performance of zinc alloy material is very good, more and more products are used for zinc alloy material to produce zinc alloy die casting, so the zinc alloy die casting process is more and more popular, but the chemical properties of zinc alloy material are very active, so the zinc alloy die casting parts are often used for surface treatment, and the treated products are not easy to be oxidized in the air, thus corrosion resistance Corrosion, wear resistance and beautiful! So what are the common surface finishes of zinc alloy die castings in the die casting industry?
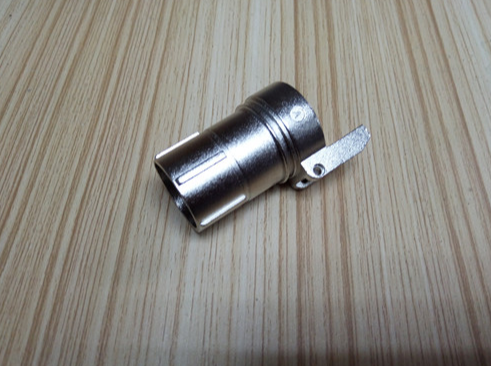
What Are The Common Surface Finishes Of Zinc Die Casting
The surface treatment of zinc is mainly divided into sandblasting, polishing, wire drawing, electroplating and spraying. Below are some of the common zinc alloy die casting surface processing technology.
1. Sand blasting of zinc alloy die castings
The process of cleaning and roughening metal surface by the impact of high-speed sand flow. This method of zinc surface treatment can make the surface of the workpiece get a certain degree of cleanliness and different roughness, improve the mechanical properties of the workpiece surface, so as to improve the fatigue resistance of the workpiece, increase the adhesion between the coating and the coating, prolong the durability of the coating, and be conducive to the leveling and decoration of the coating. This technology is often seen in Apple’s various products, and is increasingly used by the existing TV case or middle frame.
2. Polishing of zinc alloy die castings
Using mechanical, chemical or electrochemical methods to reduce the surface roughness of the workpiece to obtain a bright and smooth surface. Polishing process is mainly divided into: mechanical polishing, chemical polishing, electrolytic polishing. After mechanical polishing and electrolytic polishing, zinc parts can approach the mirror effect of stainless steel, giving people the feeling of high-grade, simple and fashionable future.
3. Drawing of zinc alloy die castings
Metal wire drawing is a manufacturing process in which the zinc plate is repeatedly scraped out with sandpaper. Wire drawing can be divided into straight line drawing, random drawing, rotary drawing and thread drawing. Metal wire drawing process can clearly show each fine and micro wire trace, so as to make the metal matte with fine silk luster. The product has a sense of fashion and technology.
4. High gloss cutting of zinc alloy die castings
The diamond knife is reinforced on the spindle of the high-speed rotary engraving machine to cut the parts, and the local bright area is produced on the surface of the product. The brightness of the cutting highlight is affected by the speed of the milling bit. The faster the bit speed is, the brighter the highlight will be. Otherwise, it will be darker and more likely to produce tool marks.
5. Anodizing of zinc alloy die castings
Anodic oxidation refers to the electrochemical oxidation of metals or alloys. Zinc and its alloys form an oxide film on zinc products under the action of external current under the corresponding electrolyte and specific process conditions. Anodizing can not only solve the defects of zinc surface hardness and wear resistance, but also prolong the service life of zinc and enhance the beauty. It has become an indispensable part of zinc surface treatment and is the most widely used and very successful process.
6. Two Color Anodizing of zinc alloy die castings
Two Color Anodizing refers to anodizing on a product and giving different colors to specific areas. Because of the complexity of the process, the cost of two-color anodizing is high. But through the contrast between the two colors, it can reflect the high-end and unique appearance of the product.
7. Electrophoretic for zinc alloy die castings
Electrophoresis is that the electrophoretic paint is applied to the cathode and anode, and the charged paint ions move to the cathode under the action of voltage, and interact with the alkaline substance generated on the cathode surface to form insoluble matter and deposit on the surface of the workpiece. It includes four processes: electrolysis, electrophoresis, electrodeposition, and electroosmosis.
The above seven are the common surface finish process of zinc alloy die casting parts. Diecasting-mould has been focusing on the die casting industry for 15 years, and has accumulated rich die casting service experience in the die casting industry. Equipped with advanced die casting technology equipment and experienced die casting technology team, from product mold design to product delivery one-stop production, in order to better serve each customer of Diecasting-mould and ensure the quality of zinc alloy die casting products, we also have our own factory which can effectively help customers improve production efficiency and save production costs!