Zinc Die Casting Design Process - 9 Zinc Die Casting Mold Making Ideas
Zinc is one of the important and common materials for die casting, what’s the process of designing the zinc die casting mold? As die casting is one of the important methods for forming nonferrous metals, 80% of the quality of die casting depends on the die casting mold. Making die casting mold is the key to product development. For designers involved in zinc die casting mold, here are some tips and steps on how to design your part or product for zinc die casting efficiently and economically.
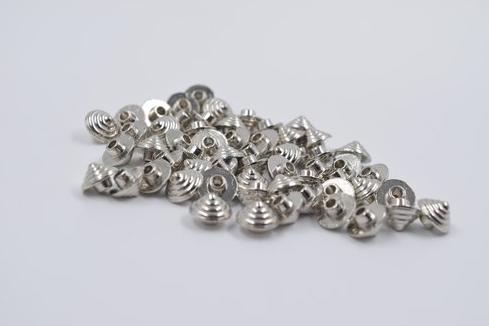
Zinc Die Casting Design Process
The design program of zinc alloy die casting mold generally includes the following aspects:
1. Obtain necessary information and data
It includes: Part drawing of die casting parts, dimension tolerance, shape and position tolerance, surface roughness, material, heat treatment requirements and other technical requirements; production batch and delivery date of die casting parts, equipment condition of zinc alloy die casting unit, processing capacity and equipment conditions of mold processing unit and other users’ requirements.
2. Analyze the structure, material and technical requirements of zinc alloy die casting
1) Whether the structure of zinc die casting can ensure the quality of casting and favorable molding is analyzed. For example, whether the wall thickness of the die casting is uniform and reasonable, whether there is a fillet at the corner of the wall, whether the diameter and depth ratio of the hole are appropriate, whether the required dimensional accuracy and surface roughness are appropriate, whether additional demoulding slope is required, whether there are inserts, etc.
2) Analyze the requirements of zinc die casting alloy materials for mold materials and applicable die casting machines.
3) If there are unreasonable or inappropriate structures and requirements, put forward modification opinions to discuss with customers. Only by combining product design, mold design, mold manufacturing and product production, can we get perfect quality die castings.
3. Determine the number of cavities, select parting surface, gating system and overflow system
1) Preliminarily determine the number of cavities of the die-casting mold according to the production batch of die-casting machine and die-casting parts.
2) Choose the position of the parting surface reasonably according to the basic principles of parting surface selection.
3) Reasonably choose the type of gating system and gate location according to the structural characteristics of the casting, and make the casting have the best molding conditions.
4) Determine the form and location of the overflow system.
4.Select the die casting machine model
Calculate the required clamping force according to the quality of the zinc die casting and the projected area of the zinc die casting part on the parting surface, and combine with the actual situation of the die casting machine owned by the die casting unit, preliminarily select the die casting machine.
5. Determine the mold structure
After the determination of parting surface, gating system and overflow system, the following aspects should be considered:
1) Determine the structure of the forming parts. If it is mosaic type, determine the combination form and fixed form of insert and core.
2) Determine the structure form and composition of core pulling mechanism according to the shape characteristics of side hole and side concave.
3) Determine the form and layout of the guiding mechanism.
4) According to the structural characteristics of the die casting, select the type of the ejection mechanism and the pushing position of the die casting and the pushing position and the reset and guiding form of the ejection mechanism.
5) Determine the form of temperature regulation system, and preliminarily consider the layout of cooling channel.
6) When considering the composition of each mechanism of the mold, the machining performance of the parts should be considered.
Then Select zinc die casting parts material and heat treatment.
6. Draw the structure sketch of the mould
Drawing the structure sketch can check the coordination relationship between the structures considered. For inexperienced designers, this sketch is used to solicit the opinions of mold manufacturing and mold operators, so as to introduce their rich practical experience into the design.
7. Calculation and verification of parameters
1) Calculate the forming size of forming parts.
2) Calculate and check the thickness of cavity side wall and bottom plate of forming parts to determine the size of template.
3) Calculate the core pulling force, core pulling distance, mold opening stroke and inclined guide pillar size.
4) Check the compression instability of push rod.
5) Check the relevant parameters of die casting machine, such as clamping force, chamber capacity, opening stroke and installation dimension of mold.
6) Calculate the parameters of temperature regulation system.
8. Draw the assembly drawing of die casting mold
In addition to indicating the assembly relationship between parts, the assembly drawing of die casting mold shall also indicate:
1) The maximum dimension and installation dimension of the mould.
2) Die casting machine model selected.
3) The minimum opening stroke and pushing out stroke of ejection mechanism.
4) Casting gating system and its main dimensions.
5) Action process of special mechanism.
6) Name of mold parts.
7) Technical requirements for die casting die assembly.
9. Draw the part drawing of die casting mold
Starting from the forming parts, the structural parts such as movable and fixed die sleeve plate, sliding block and inclined guide pillar are designed. The die part drawing should correctly reflect the shape of the part, indicate the part size, dimensional tolerance, form and position tolerance, surface roughness, technical requirements and material heat treatment requirements.