What are the advantages of die casting for mass production? And how do you increase the production rate in manufacturing?
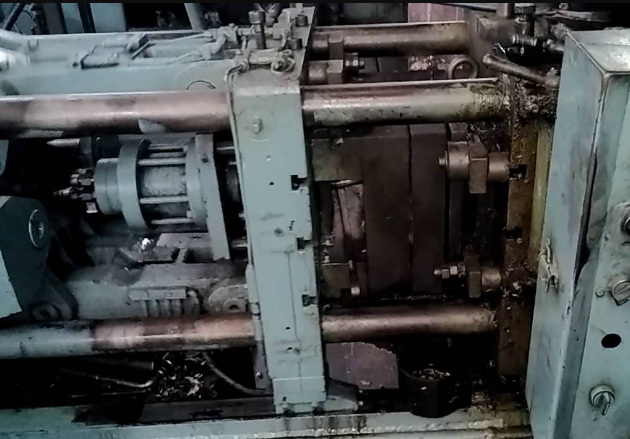
Which Casting Process Is Suitable for Higher Production Rates?
Among the various casting processes, high-pressure die casting (HPDC) is generally considered ideal for achieving higher production rates. High-pressure die casting is a casting process that involves injecting molten metal, typically aluminum or zinc alloys, into a steel mold under high pressure. The molten metal fills the mold cavity, solidifies rapidly, and the part is then ejected. HPDC offers several advantages that make it well-suited for high-volume production.
Is Die Casting Suitable for Mass Production?
Yes, die casting is good for mass production. This process allows for the production of highly detailed, complex, and dimensionally accurate parts with a high degree of repeatability. Die casting offers several advantages for mass production.
– Efficiency and High Production Rates: Die casting is a highly efficient process with fast cycle times. It enables manufacturers to produce large quantities of parts in a relatively short period. The high-speed production capability makes it ideal for mass production requirements.
– Complex and Intricate Shapes: Die casting allows for the creation of intricate and complex part geometries that may be challenging or costly to achieve through other manufacturing processes. The die’s design can incorporate intricate details, thin walls, and complex features, resulting in highly precise and intricate parts.
– Consistency and Tight Tolerances: Die casting offers excellent dimensional accuracy and consistency, ensuring that the produced parts meet tight tolerances and precise specifications consistently. This is crucial for mass production, where uniformity and consistency across a large quantity of parts are necessary.
– Material Variety: Die casting supports a wide range of materials, including aluminum, zinc, magnesium, and copper-based alloys. Each material has its own unique properties, making die casting suitable for various applications across industries such as automotive, aerospace, consumer electronics, and more.
– Cost-Effective: Die casting can be cost-effective for mass production due to its efficiency, minimal post-processing requirements, and high repeatability. The initial tooling costs can be higher compared to other processes, but the per-part cost decreases significantly with large production quantities.
What determines the production capacity of die casting?
– Die casting is a fast-paced manufacturing process. Cycle times can range from a few seconds to a few minutes, depending on the size and complexity of the parts and the specific die casting technology utilized. The high-speed nature of the process enables manufacturers to produce a significant number of parts in a relatively short period.
– Die casting processes can often be automated or semi-automated, allowing for continuous production with minimal downtime. Automation increases the production rate and improves overall efficiency. It also enables manufacturers to achieve consistent quality and reduce dependence on manual labor.
– Die casting molds, known as dies, can be designed with multiple cavities to produce multiple parts simultaneously in each casting cycle. This multi-cavity configuration further enhances production capacity by increasing the number of parts produced per cycle.
– The production capacity of die casting can be easily scaled to meet specific demand requirements. Manufacturers can adjust production volumes by increasing or reducing the number of die casting machines, optimizing production schedules, and managing multiple production lines.
– Experienced die casting manufacturers constantly work on process optimization, including reducing cycle times, improving efficiency, and implementing lean manufacturing practices. These efforts are aimed at maximizing production capacity and minimizing waste.
How to Increase the Production Rate in Die Casting?
1. Advanced Die Design: Employing advanced die design techniques can optimize the flow of molten metal and reduce turbulence during the filling process. This helps in achieving faster filling and solidification times, ultimately improving the overall production rate.
2. High-speed Injection Systems: Upgrading to high-speed injection systems ensures faster and more efficient injection of molten metal into the die. These systems can provide higher injection pressures and speeds, enabling faster fill times and reducing cycle times.
3. Advanced Cooling Methods: Implementing effective cooling methods, such as water or air cooling, can help in rapidly cooling and solidifying the cast parts. This reduces the time required for each casting cycle, allowing for faster production rates.
4. Automation and Robotics: Integrating automation and robotics into the die casting process can significantly improve production rates. Automated systems can handle tasks such as part ejection, trimming, and quality inspection, reducing the dependency on manual labor and increasing throughput.
5. Multi-Cavity Dies: Utilizing multi-cavity dies allows for the production of multiple parts simultaneously in each casting cycle. This approach increases productivity by producing a higher quantity of parts in the same amount of time.
6. Process Monitoring and Control: Implementing real-time process monitoring and control systems enables the identification and correction of process variations or abnormalities promptly. This helps optimize the process parameters for improved efficiency and reduces the risk of defects or downtime.
7. Lean Manufacturing Principles: Applying lean manufacturing principles, such as value stream mapping, 5S, and continuous improvement, can help identify and eliminate process bottlenecks, reduce waste, streamline workflow, and optimize production rates.
8. Equipment and Machinery Upgrades: Upgrading die casting equipment and machinery to utilize the latest technologies and advancements can enhance productivity and efficiency. Newer machines may provide higher injection pressures, faster response times, improved energy efficiency, and advanced control systems.
9. Skilled Workforce and Training: Ensuring that the die casting operators and technicians are adequately trained and possess the necessary skills is crucial for maximizing productivity. Ongoing training programs can keep the workforce updated with the latest techniques and best practices.
10. Efficient Part Handling and Tooling Changes: Implementing efficient part handling systems and optimizing tooling changeover processes can minimize downtime and maximize machine utilization, resulting in increased production rates.