Tesla has developed an integrated molding frame, which has saved a lot of time and manufacturing costs. It seems like a good thing, but why hasn’t integrated die-casting become popular in the automotive industry?
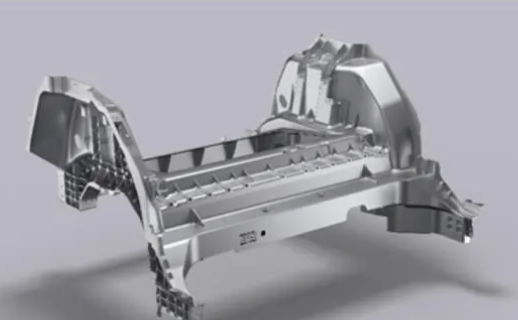
The so-called integrated die-casting technology refers to the process of redesigning and highly integrating multiple independent and dispersed small components in the original design, using a large die-casting machine for one-time molding, saving the welding process, and directly obtaining a complete large component.
Integrated die-casting technology is an innovation of traditional automotive production processes, which can make the body lightweight, save costs, improve efficiency, reduce supply chains, shorten the manufacturing and transportation time of the entire vehicle, reduce labor and robots, and greatly enhance the manufacturing scale.
Tesla is a strong promoter of integrated die-casting technology. With the adoption of integrated die-casting technology in the rear floor of Tesla Model Y, more and more vehicle manufacturers are also starting to promote the die-casting storm of aluminum alloy structural components. However, die-casting technology requires a large tonnage die-casting machine to work, and some components require a 6000 ton die-casting machine to be die-casting formed. Currently, the difficulty is high, and many car companies dare not act rashly and are still observing. Therefore, this is also one of the reasons why it has not been widely adopted yet.
Now, Tesla has made progress in manufacturing systems, thanks to integrated die-casting technology. The number of welding robots in the factory has decreased by 70%, and workers have also decreased by 60%. The rear floor of the car has adopted integrated die-casting technology, reducing more than 70 components and 700 welding points. The weight of the vehicle has decreased by more than 100 kilograms, the range has increased by 14%, and daily wear and tear costs have decreased by 20%. Tesla also stated that integrated die-casting technology is not limited to the rear floor of automobiles, and there is still room for improvement. In the future, more components will be integrated. However, in what appears to be a bustling industry from the outside, the people in the bureau remain somewhat calm. Several heads of die-casting manufacturers have stated that their related businesses are still in the research and development and reserve stages, and they are uncertain about the future space of the industry. In the past, the components of a car were complex and diverse, and the main engine factory could allocate them to different manufacturers for manufacturing. After implementing integrated die-casting technology, the division of labor became clearer. Generally speaking, the main engine factory would entrust the die-casting business to one or two enterprises, and even different car models would have to customize die-casting machines. It was no longer a time when everyone could share the pie. The industrial chain naturally seizes the time layout, strives to not fall behind others, and always harbors a sense of worry.
Another reason for industry chain concerns is that not all new energy vehicle models will use integrated die-casting technology. In the early stages of integrated die-casting technology, each die-casting machine can basically only handle one vehicle model. Generally, die-casting machines are difficult to meet, and their tonnage also needs to be continuously increased. Only in the future, large-scale production can bring economies of scale, equipment leveling, and research and development investment. That is to say, only popular models that use integrated die-casting technology can potentially bring better economic benefits. From this perspective, currently, there are not many models that use integrated die-casting technology, but very few. In addition, the high maintenance cost brought about by integrated die casting is also a major issue that cannot be ignored. If the large parts of integrated die-casting are damaged due to collision, it is difficult to repair and the entire large component must be replaced. The cost of replacement is very expensive, at least tens of thousands of dollars, which is difficult for ordinary consumers to accept.
How to make it easier for consumers to accept new products while undergoing technological innovation is also a thought-provoking issue for OEMs and the industry chain. At present, there are still some uncertain factors regarding the evolution of integrated die-casting technology. Whether it can be further popularized will require more time and patience.