A draft angle is required in most casting processes, including die casting, permanent mold, and sanding casting. What is a draft angle in die casting and how to determine it? Understanding the importance of die casting draft, and design points.
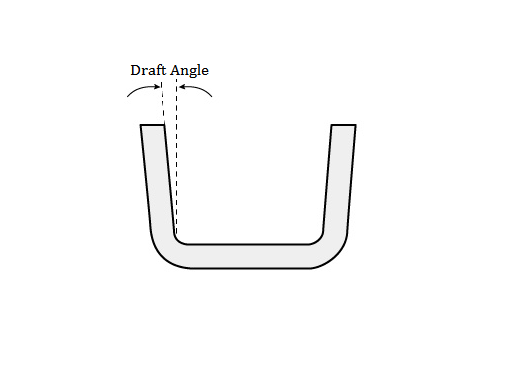
What is Draft Angle in Die Casting?
Die casting draft angle refers to the taper or inclination in the vertical direction of the casting. The draft angle is designed to reduce the friction between the part and the tool, and provide clearance for the part to eject easily from the mold. If there is no draft angle, the part may peel off, dent, or get stuck in the tool. How to determine it? The size of the draft angle is related to the demolding height, wall thickness, cavity surface roughness, and alloy type. The alloy has a large shrinkage rate, a strong affinity with the die-casting mold, and a rough surface of the cavity requires a large draft.
Why is the Die Casting Draft Angle Important?
The shrinkage stress of die castings in the process of molding cooling and shrinkage die casting causes the castings to stick to the mold core and produces demoulding resistance in the process of demoulding the castings from the mold. In order to reduce the resistance of demoulding from the castings, the core is easier to pull out and prevents the surface of castings and cores from being scratched due to friction caused by relative movement. In short, the die casting draft angle must be the same as the demoulding direction on the side of the casting.
How to Design Draft Angle?
1) Considering the problem of wall thickness, excessive thickness difference will affect the filling.
2) Considering the demoulding problem is very important in die casting practice. In reality, such problems often occur, which is much more annoying than injection molding demoulding. Therefore, pay attention to the setting of draft angle and the calculation of the demoulding force of medium moving fixed mold. Generally, the draft angle is 1 to 3 degrees. Generally, considering the smoothness of demoulding, the external draft angle is smaller than the internal draft angle, and the external draft is 1 degree, The internal draft should be about 2 ~ 3 degrees.
3) During the design, the problem of mold design shall be taken into account. If there are multiple coring positions, try to put them on both sides, and it is best not to put them in the lower position. In this way, the lower coring will be easy to cause problems after a long time.
4) Some die castings may have special requirements for appearance, such as oil injection, powder spraying, etc. at this time, the structure should avoid important appearance positions to facilitate the setting of gate overflow groove.
5) In the structure, try to avoid the structure that leads to the complex structure of the die, such as having to use multiple core pulling or spiral core pulling, etc.
6) For parts requiring surface machining, it should be noted that appropriate machining allowance should be reserved in the part design, not too much, expose all the pores inside, not too little, otherwise after rough and fine positioning, the black surface has not dried out, and you will wait to spark on the mold. How much will you give, The reserved amount should not be greater than 0.8mm. In this way, there are basically no pores on the processed surface, because it is protected by a hard layer.
7) Another thing is to pay attention to the material selection. Whether to use ADC12 or A380 depends on the specific requirements.
8) Aluminum alloy has no elasticity, so it can only be matched with plastic.
9) Generally, deep holes cannot be made. When opening the mold, only make some regular holes, and then post-processing.