Aluminum housings can also be made from cast aluminum, which can offer advantages such as greater design flexibility and the ability to produce complex shapes. Cast aluminum housings can also be made from various aluminum alloys, depending on the application requirements. There are two main categories of aluminum used to construct housings: aluminum profiles and die cast aluminum. Oxidation techniques may be applied to aluminum profiles, however, die cast aluminum can only be sprayed. Today, we’re going to find out why are most aluminum housings on the market painted rather than oxidized.
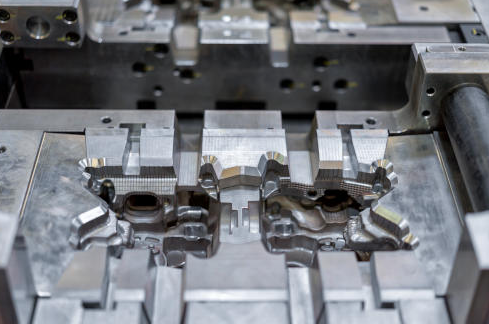
Why Are The Most Aluminum Housings On The Market Painted Rather Than Oxidized?
Most aluminum housings on the market are painted rather than oxidized for several reasons:
Appearance: Painted housings can have a more consistent and uniform appearance, and the color can be customized to suit the needs of the customer. In contrast, oxidized aluminum has a more natural, matte appearance that may not be suitable for all applications.
Protection: Paint can provide an extra layer of protection against scratches, corrosion, and other forms of damage. This is especially important for housings that are exposed to harsh environments, such as those used in outdoor applications.
Cost: Painting is generally less expensive than the process of anodizing, which is the most common method of oxidizing aluminum. Anodizing requires specialized equipment and chemicals, and the process can be more time-consuming and labor-intensive than painting.
Flexibility: Painted housings can be easily touched up or repainted if they become damaged or worn over time. In contrast, anodized aluminum is more difficult to repair and may require stripping and recoating to restore its appearance.
Advantages of die cast aluminum
Die cast aluminum has several advantages that make it a popular choice in various industries. Die cast aluminum offers a unique combination of strength, lightweight, corrosion resistance, thermal conductivity, and versatility, making it a popular choice in various industries, including automotive, aerospace, electronics, and consumer goods.
Lightweight: Aluminum is a lightweight material, which makes it ideal for applications where weight is a concern. Die cast aluminum components can be up to 1/3 lighter than similar components made of steel or other metals.
High Strength: Despite its lightweight, die cast aluminum is a strong material that can withstand high loads and stresses. This makes it an ideal material for structural components in various applications.
Corrosion Resistance: Aluminum is naturally resistant to corrosion, which makes it ideal for outdoor and marine applications where exposure to moisture and salt can cause other metals to corrode.
High Thermal Conductivity: Aluminum is an excellent thermal conductor, which makes it an ideal material for heat sinks, electronic enclosures, and other components that need to dissipate heat quickly.
Dimensional Stability: Die cast aluminum components have excellent dimensional stability, which means they maintain their shape and size even under high loads and stresses. This makes them ideal for precision components that need to maintain tight tolerances.
Versatility: Die cast aluminum can be easily machined, welded, and finished with various coatings, including powder coating, anodizing, and painting, which makes it a versatile material for various applications.
Why is die cast aluminum not suitable for oxidation?
Die cast aluminum can be oxidized, but the resulting finish may not be as good as the finish achieved on other types of aluminum. This is because die cast aluminum typically contains higher levels of impurities, such as silicon and copper, than other types of aluminum.
During the anodizing process, these impurities can cause uneven anodic coatings, which can result in a blotchy or mottled appearance on the surface of the part. In addition, the anodizing process can expose any porosity or defects in the die cast aluminum, which can also affect the appearance and performance of the finished part.
To mitigate these issues, die cast aluminum parts can be pre-treated before anodizing, such as with a chromate conversion coating, to improve the adhesion and uniformity of the anodic coating. However, even with pre-treatment, the resulting finish may not be as uniform or consistent as that achieved on other types of aluminum.
As a result, other surface treatment options may be preferred for die cast aluminum parts, such as painting or powder coating, which can provide a more consistent and uniform finish while also offering protection against corrosion and other forms of damage.
What are the advantages of painted aluminum housings?
Painted aluminum housings offer several advantages, including:
Aesthetic appeal: Painted aluminum housings can be customized to match the desired color and finish, providing a visually pleasing appearance that can enhance the overall look of the product.
Protection: Paint provides a protective barrier that can help prevent damage to the aluminum housing from environmental factors such as UV radiation, moisture, and corrosive chemicals. This can extend the lifespan of the product and reduce the need for maintenance.
Resistance to wear and tear: Paint can also help protect the aluminum housing from scratches, abrasion, and other types of physical damage. This can help maintain the integrity of the housing and protect any internal components from damage.
Flexibility: Painted aluminum housings can be easily touched up or repainted if needed, making them a more versatile option compared to anodized aluminum housings, which are more difficult to modify or repair.
Cost-effectiveness: Painting is often a more cost-effective option compared to other surface treatments such as anodizing or plating. This can make it a more practical option for applications that require a high-quality finish but have budget constraints.
Compatibility with other materials: Painted aluminum housings can be easily integrated with other materials, such as plastic or glass, making them a more versatile option for products that require a combination of materials.