Which Is Better, Die Casting Or Stamping? - Difference Between Die Casting And Stamping Process
If you have the need for manufactured metal parts of different shapes, casting and stamping are the two best methods you can choose. Casting involves pouring hot metal into a mold, stamping means putting a sheet of metal onto a form and hitting the sheet of metal with a large, shaped hammer. In this article, we make a comparison between die casting and stamping, covering advantages and disadvantages of each, difference between casting and stamping process, we help you make a better choice when die casting vs stamping.
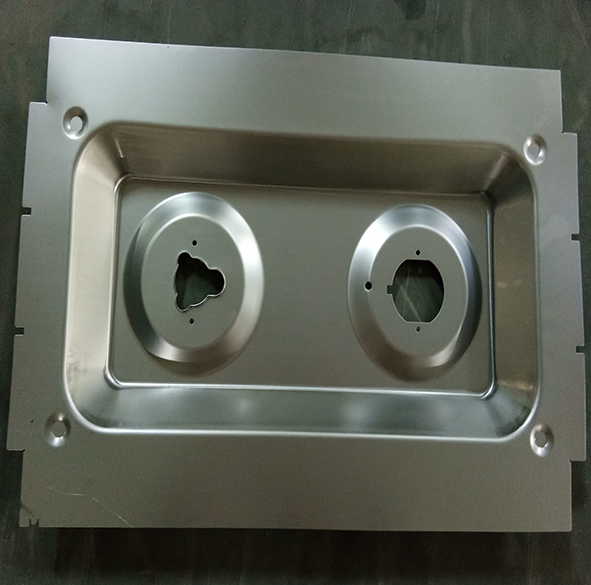
Die Casting – Advantages, Process & More
The basic process of die casting is: the liquid metal is first cast at low speed or high speed and filled into the cavity of the mold. There is a movable cavity surface in the die casting mold factory, which is pressed and forged with the cooling process of the liquid metal, which not only eliminates the shrinkage defects of the blank, but also makes the internal structure of the blank reach the forged broken grain. The comprehensive mechanical properties of the blank have been significantly improved. In addition, the surface finish of the blank produced by this process reaches grade 7 (Ra1.6), which is the same as the surface produced by cold extrusion or machining, and has metallic luster. Therefore, we call the die casting mold forging process “limit forming process”, which is a step further than “no cutting, less allowance forming process”. Another advantage of die casting and forging process is that in addition to the traditional casting materials, it can also use deformation alloy and forging alloy to produce parts with complex structure.
Stamping – Advantages, Process & More
Compared with other methods of mechanical processing and plastic processing, stamping has many unique advantages both in technology and economy. The main manifestations are as follows:
1. The production efficiency of stamping process is high, and the operation is convenient, and it is easy to realize mechanization and automation. This is because stamping depends on the stamping die and stamping equipment to complete the processing. The stroke times of ordinary press can reach dozens of times per minute, and the high-speed pressure can reach hundreds or even thousands of times per minute, and each stamping stroke can get a stamping part.
2. As like as two peas are used to ensure the stamping parts’ surface quality, the mold life is generally longer. The stamping quality is stable and interchangeability is good, and it has the same characteristics.
3. Stamping can process parts with large size range and complex shape, such as stopwatch of clock and watch, automobile longitudinal beam, panel, etc. with the cold deformation hardening effect of material during stamping, the stamping strength and stiffness are higher.
4. Stamping does not produce chips and chips, consumes less materials, and does not need other heating equipment, so it is a kind of material saving and energy-saving processing method, and the cost of stamping parts is lower.
Because of the advantages of stamping, stamping processing has a wide range of applications in various fields of the national economy. For example, in aerospace, aviation, military industry, machinery, agricultural machinery, electronics, post and telecommunications, transportation, chemicals, medical equipment, household appliances and light industry, there are stamping processes. Not only the whole industry uses it, but everyone is directly connected with stamping products. Of course, stamping also has some problems and shortcomings. The main performance in the stamping process noise and vibration two kinds of public hazards, and the operator’s safety accidents occur from time to time. However, these problems are not entirely due to the stamping process and die itself, but mainly due to the traditional stamping equipment and backward manual operation.
Die Casting Vs Stamping, What’s The Difference?
1. Two extremely different processes of metal forming are metal stamping and die casting. Ingots or billets are used by die casting, while stamping requires blanks or coils of sheet metal; metal is heated to die cast past its melting point, while stamping is almost always a cold working process.
2. Die casting is capable of generating parts with geometries that are extremely complex. When it is used for components with simpler geometries, metal stamping is more economical. Stamping is capable of producing very complex parts, but at a cost: the more complicated a part is, the more components the instrument and die require, the higher the cost of tooling becomes, the more tool and die components there are.
3. Stamping can be carried out on both ferrous and non-ferrous materials, whereas die casting is usually restricted to non-ferrous materials only. Although it can be minimized by careful design, stamping generates a large amount of scrap material-it can be recycled, but the cost of the material includes the cost of material that is not used directly. A much smaller volume of scrap is generated by die casting and the scrap produced is more readily recyclable, simply converted to the holding pot and allowed to re-melt.
Which Is Better, Die Casting Or Stamping?
If you need a high volume of components with any level of complexity to be produced, die casting is usually the right choice. Since stamping dies are cheaper and usually last the lifetime of the part, and can quickly produce strong parts, if they have a very large amount of product they need to run off quickly, some may opt for stamping.