Which Gating System Is Suitable For Aluminum Alloy Die Casting
There are many process methods applicable to aluminum alloy. The following suggestions on improving the gating system are only put forward for the sand casting process of horizontal parting.
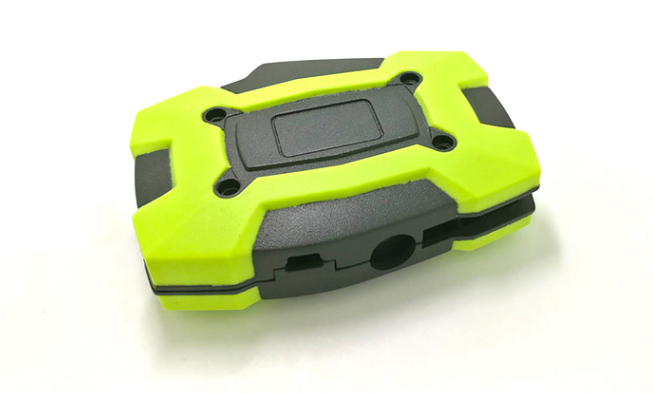
Gating System Of Aluminum Alloy Die Casting
Taking out the aluminum alloy liquid from the melting furnace and pouring it into the mold is a key process in the production of aluminum alloy die castings. Although this process takes a short time, the movement of the alloy liquid in the transmission process is very intense, the oxide film on the liquid surface is constantly damaged, new oxide films are constantly generated, and the “oxide film interlayer” is constantly involved in the alloy liquid, Therefore, most waste products are caused at this stage. From the point of view of “oxide film interlayer”, the control of pouring process is much more important than that of smelting process.
When the aluminum alloy liquid flows, if the flow rate is low, the surface tension of the alloy liquid can restrict the liquid flow so that it will not disperse and splash; If the flow rate is high, the liquid flow will inevitably disperse and splash.
Many studies have shown that for a variety of liquid casting alloys, the critical velocity of liquid flow without dispersion and splash is 0.5m/s.
At present, the most widely used pouring method is still the traditional gravity pouring, that is, the gravity of the alloy liquid itself is used to inject it into the mold from above the mold. In fact, this is the most undesirable pouring method for aluminum alloy, because when the liquid flow falls from the straight gate to its bottom, the flow rate is much higher than 0.5 m / s, and the scattered liquid flow and splash are inevitable. In addition, there are many problems with some of the design principles of the gating system that are regarded as conventional. The liquid flow in the gating system often produces turbulence and splash, which will cause a large number of “oxide film interlayer” and bubbles to be involved in the alloy liquid, resulting in a variety of casting defects.
The differential pressure casting or low pressure die casting process is adopted, and the liquid flow enters the mold from below the mold. If properly controlled, the alloy liquid can fill the mold smoothly and slowly. There are few defects in aluminum alloy die castings, and the mechanical properties of materials are greatly improved. According to the literature, many large aluminum alloy and magnesium alloy die castings used in American aviation and aerospace are made by differential pressure die casting process.
There is also a pouring process of stable mold filling, which is the tilt casting or tilt filling to transfer the liquid flow horizontally. The pouring method is: place the mold and ladle in a tilting device to align the gate of the mold with the outlet of the ladle, and then tilt the device slowly to transfer the alloy liquid smoothly from the ladle to the mold. At present, it has been reported that this process has been used to produce aluminum alloy die castings and titanium alloy die castings, mainly some particularly important die castings.
Although the latter two pouring processes have good effects and are more suitable for the production of aluminum alloy die castings, gravity pouring is a traditional process that has been applied for thousands of years, and there are constraints in production conditions. Today, with the increasing consumption of aluminum alloy die castings, most die castings are still produced by gravity pouring. In order to further improve the quality of die castings and make full use of the potential of aluminum alloy in mechanical properties in casting production, improving the gating system is a subject that must be seriously faced at present.
Which Types Of Gating System Is Suitable For Aluminum Alloy Die Casting
According to the cross-sectional area ratio of each element of the gating system, there can be many different modes, and we only mention three of them here.
1. The closed gating system is characterized by: the cross-sectional area at the end of the straight gate > the cross-sectional area of the runner > the cross-sectional area of the inner gate. It is the most commonly used gating system for manufacturing iron castings, with the smallest flow blocking section at the inner gate.
When the closed gating system is adopted, due to the action of static pressure head and liquid flow kinetic energy in the system, the alloy liquid enters the mold cavity by spraying. It is difficult to avoid turbulence and oxide film on the surface of liquid flow, and it will impact the mold. These conditions have a negative impact on the quality of castings. Therefore, in principle, this gating system is not suitable for aluminum and magnesium alloys that are easy to oxidize and have high oxide melting point, but it is also used in actual production.
2. Open gating system for aluminum alloy die castings, in order to avoid turbulence and oxide film involvement, open gating system is widely used. Some literatures suggest that the cross-sectional area ratio of each component of gating system is: Straight gate outlet cross-sectional area: total cross-sectional area of runner: total cross-sectional area of inner gate = 1: 2 :4. It was also suggested that the ratio of the three should be 1:4:4.
In recent years, a lot of research work shows that the increase of cross-sectional area of runner can not avoid turbulence and dispersion, and the filling time of gating system is long, the alloy liquid level is easy to oxidize, which can not ensure the quality of castings. In addition, the size of the gating system is too large, which will also lead to the reduction of process yield, which is also undesirable.
3. Natural flow gating system, which is more suitable for aluminum alloy die casting, adopts a compact gating system to restrict the liquid flow and keep the liquid flow stable without dispersion. The connection between the sprue and the runner shall adopt the method of smooth transition. When the runner must be turned to the other direction, the corner shall also be a smooth arc. Such a gating system is called “natural flow gating system”.
When the liquid flows through the 90 ° bend, the flow rate of the liquid flow is reduced by about 20% due to the action of friction. Therefore, the relationship between the components of the natural flow gating system is roughly as follows: the cross-sectional area of the straight gate outlet: the cross-sectional area of the runner: the total cross-sectional area of the inner gate = 1:1.2:1.4. As for the specific dimensions of the components of the gating system, According to the structure of die castings and the overall arrangement of gating system, it is impossible to have generally applicable data at present. For important die castings and mass-produced die castings, the gating system shall be designed with reference to the results of computer simulation. If possible, video radiography technology should be used for verification.
V-shaped Funnel Gate Cup Should Not Be Used
At present, the V-shaped funnel gate cup widely used in the casting industry is not suitable for aluminum alloy die castings because it will bring many problems, such as:
1. When pouring, if the liquid flows directly from the ladle nozzle into the sprue, turbulence and splash will occur in the gating system.
2. The capacity of the sprue cup is small, it is difficult to keep full during pouring, and it is easy to get involved in air, oxide film and other inclusions.
3. During pouring, the liquid flow may be directly injected into the straight gate or rush to a certain part of the gate cup. Therefore, the liquid flow is unstable and the flow rate is difficult to control, which makes it difficult to reflect the design functions of other components of the gating system.
4. When pouring, if the liquid flow deviates from the center line of the straight gate, vortex will be generated, which is very easy to be involved in air and oxide film.
With the gate basin offset by the outlet, the liquid flow has a buffering effect after being injected into the gate basin. Of course, the effect is good. However, if the bottom of the gate basin is flat and the liquid flow flows to the outlet, due to the action of inertia, a considerable part of the falling DC channel near the starting point of the liquid flow cannot be filled.
The way to solve the problem is to set up a dike in the gate basin, but the influence of dike shape should be considered. If a rectangular dike is set, when the liquid flows to the outlet, there is a small section of horizontal flow, and the inertia will still work, but the impact is small. It is more ideal if a circular dike is set.
Considerations On Straight Gate
The straight gate commonly used in the foundry industry is often cylindrical with the same upper and lower cross-sectional areas. For aluminum alloys that are easy to oxidize, this direct gate is not suitable, because there is a large air gap in the direct gate during the pouring process, and an oxide film is formed on the liquid flow surface. More importantly, if there is no air gap in the sprue, the liquid flow is in close contact with the wall of the sprue in the mold, and most of the oxide film on the surface will adhere to the wall and do not enter the mold cavity; If there is an air gap, these oxide films are easy to be drawn into the cavity. Due to the effect of gravity acceleration, when the liquid falls, its velocity increases with the falling distance, and the cross-sectional area of the liquid flow decreases accordingly.
About Gate Nest
It is a conventional practice in the foundry industry to set the gate nest at the lower end of the straight gate. It is generally believed that the gate nest can play a buffer role, reduce the involvement of bubbles and reduce the turbulence in the gating system.
However, the systematic study by X-ray photography shows that for small or slightly large castings, in the channel compact gating system, it is better to adopt streamlined arc transition at the junction of straight gate and transverse gate. Under this condition, the surface tension of alloy liquid can be about the front edge of beam liquid flow without dispersion and splash. Setting a gate nest at the lower end of the straight gate will cause turbulence and involve bubbles, which is not conducive to the quality of aluminum alloy die castings.
Runner And Ingate
Determination of cross-sectional area of transverse gate and inner gate.
1.Location of inner gate
When a closed gating system is used, the inner gate is usually located in the lower part of the transverse sprue. The guiding ideology of this arrangement is that oxide films, bubbles and other inclusions involved in the liquid flow can float above the runner and will not enter the cavity through the inner gate. In fact, when the liquid flow front in the runner passes through the first ingate, it will fall into the ingate and flow into the cavity, and involve oxide film, bubbles and inclusions. The fallacy of this consideration is obvious. Even when casting iron castings with closed gating system, this process is not desirable because the front of liquid flow is also the most oxidized, dirty and contains the most impurities.
The internal gate shall be set above the transverse gate.
2.Cross sectional area of runner
The cross runner used by many production units, regardless of its length and several internal gates, is of equal section, and its function and effect are not carefully evaluated.
If there are multiple internal gates behind the runner, in order to make the liquid flow evenly enter the mold cavity through each internal gate, the constant cross-section runner is adopted, which not only consumes more alloy and reduces the process yield, but also has poor filling effect and damages the quality of the casting.