It is normal that a poor surface finish appears in casting? How to address the causes and get a good casting surface finish? Some casting processes give a relatively good surface finish.
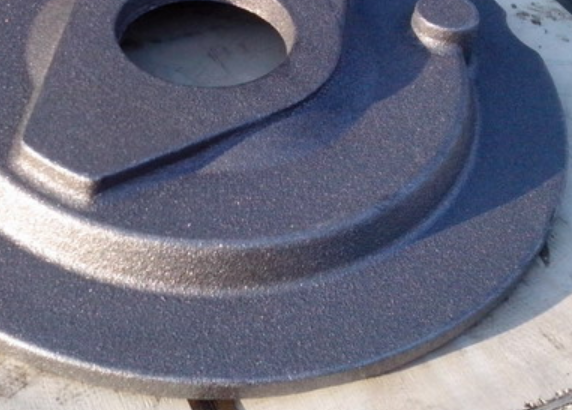
Which Casting Process Gives the Best Surface Finish?
The casting process that gives the best surface finish depends on several factors such as the casting material, the complexity of the part, and the desired surface finish. But some casting processes are generally known for producing high-quality surface finishes. These include:
– Investment casting: Investment casting, also known as lost-wax casting, is capable of producing very high-quality surface finishes. The process involves creating a wax pattern of the part and then coating it with a ceramic shell. The wax is melted out and the cavity is filled with molten metal, producing a high-quality surface finish with intricate details.
– Precision sand casting: Precision sand casting, also known as no-bake sand casting, can produce high-quality surface finishes with good dimensional accuracy. The process involves using a binder and sand to create a mold, which is then filled with molten metal. The mold is then removed to reveal the cast part.
– Permanent mold casting: Permanent mold casting, also known as gravity die casting, can produce high-quality surface finishes with good dimensional accuracy. The process involves using a reusable mold made from steel or graphite to cast the part.
– Die casting: Die casting can produce relatively smooth surface finishes, with surface roughness values typically falling within the range of 4 to 8 µm (160 to 320 µin). The process involves injecting molten metal into a mold under high pressure.
What Causes Poor Surface Finish in Casting?
Poor surface finish in casting can be caused by several factors, including:
– Poor mold design: The mold used for casting the part must be designed to create the desired surface finish. If the mold is poorly designed or has defects, it can transfer those defects onto the surface of the casting.
– Casting defects: The presence of casting defects such as porosity, inclusions, or shrinkage can cause surface irregularities or roughness.
– Casting parameters: The temperature, pressure, and speed of the casting process must be properly controlled to minimize turbulence and metal velocity, which can create surface defects.
– Finishing techniques: Improper or inadequate post-casting finishing techniques can leave behind surface imperfections or roughness.
– Material properties: The material properties of the casting material can affect the surface finish. For example, if the casting material is too hard or too brittle, it may be more difficult to achieve a smooth surface finish.
– Handling and storage: Poor handling or storage of the casting can cause surface damage, scratches, or other imperfections.
– Environmental factors: Environmental factors such as temperature, humidity, and air quality can also impact the surface finish of a casting.
How Do You Get a Good Surface Finish in Casting?
To achieve a good surface finish in casting, the following steps can be taken:
– Proper mold design: The mold used for casting the part must be designed to create the desired surface finish. A smooth and detailed mold surface can transfer to the casting surface and produce a smooth finish.
– Control of casting parameters: The temperature, pressure, and speed of the casting process must be properly controlled to minimize turbulence and metal velocity, which can create surface defects.
– Post-casting finishing: After casting, the surface of the casting can be improved through various finishing techniques such as sanding, filing, polishing, vibratory finishing, or shot blasting. These techniques can remove any surface irregularities, burrs, or imperfections to produce a smooth, uniform surface finish.
– Selection of casting material: The material properties of the casting material can affect the surface finish. Choosing a material that is easily castable and has good machinability can help achieve a smooth surface finish.
– Environmental control: Environmental factors such as temperature, humidity, and air quality can also impact the surface finish of a casting. Controlling the environment during casting and finishing can help ensure a good surface finish.
– Quality control: Regular quality control checks during the casting process can help identify any issues that may impact the surface finish. This can include checking for defects, verifying dimensional accuracy, and testing for mechanical properties.