The precision and durability of the machine depend on the aluminum casting‘s dimensional stability. Pump operating rate, energy consumption, and cavitation development are all directly influenced by the dimensions, profile accuracy, and surface roughness of the impeller, housing, and inner cavity of hydraulic components; Aluminum castings, such as the cylinder block, cylinder head, cylinder liner, piston ring, and exhaust pipe, have a direct impact on the durability of the engine. Using electromagnetic pump low-pressure casting technology, aluminum smelting and molding composite purification technology, and manufacturing industry core technology as its foundation, complex aluminum casting is a cutting-edge method for fabricating aluminum castings. The electromagnetic pump low-pressure casting molten metal transmission system not only improves the casting quality of aluminum castings, but also can function in a natural setting due to its stable flow, convenient flow control, and the advantages of the process melting aluminum oxide reverse suction and easy realization. Lessen the burden on the workforce and achieve fully automated, state-of-the-art casting production. Here we talk about the quality requirements for aluminum casting.
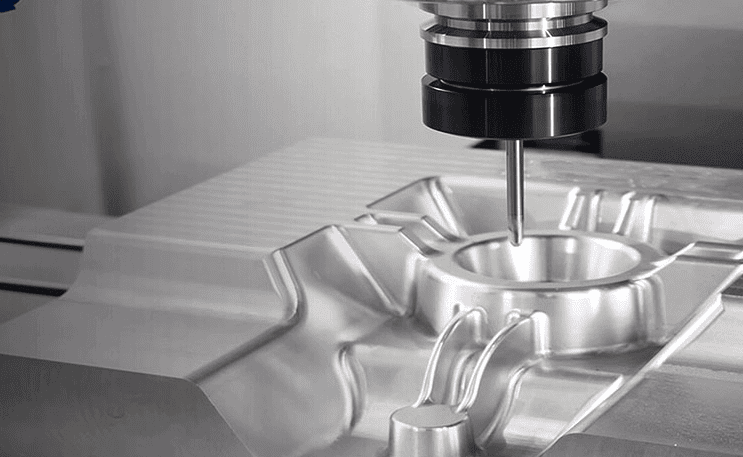
In what ways is it important that an aluminum casting meet certain quality standards? Let’s now offer you a thorough introduction:
1. The rate at which aluminum castings may be produced is directly related to the volume of liquid contained inside the ingot. Increasing the casting speed increases the ingot liquid cavity and temperature gradient, leading to the formation of a liquid cavity section at the bottom of the liquid cavity and, in turn, to an increase in shrinkage stress and an increase in the likelihood of hot cracks in the ingot.
2. A proper casting temperature of aluminum castings will retain the liquid metal in excellent fluidity, lowering the organizational stress and avoiding fractures. The ingot specification and material type will dictate the standard casting temperature. Incorrect heat treatment may lead to increased internal tension, which in turn can cause fractures or breaks in the casting. If the temperature is too low, the ingot may develop surface defects such cold shuts, slag inclusions, and fractures. If it’s a big problem, casting has to stop.
3. The third factor is the height of the liquid level, which is crucial. If it’s too low, the material’s propensity to hot crack will rise, which will have a negative impact on the casting process. A higher ingot segregation degree results from an excessive liquid level. Keeping the right amount of fluids is, thus, crucial. It’s not permitted if the height or depth is deemed inappropriate.
4. It is unacceptable for castings to have flaws such cracks, cold shuts, sand holes, air holes, slag holes, shrinkage porosity, or oxidized slag inclusions.
5. The casting’s non-machined surface must be smooth, clean, and straight, and the casting markings must be legible. After cleaning, the pouring and riser should sit at the same level as the casting surface.
6. The castings must be in accordance with the applicable requirements of GB/T6414 or GB/T11351 or the dimensions and variations specified by the Demander’s drawings or patterns.
7. No hammering, blocking, or dipping of the casting is permitted to remedy leaks.
Equipment and components manufactured of aluminum or aluminum alloy via the casting process are referred to as “aluminum casting.” Most aluminum castings are made by pouring molten aluminum or aluminum alloy into a sand mold or metal mold, depending on the desired form and size. The mechanical product’s characteristics are significantly impacted by the quality of the aluminum castings used in their construction. Strength and heat resistance of aluminum castings, such as cylinder block, cylinder head, and engine blocks, directly affect the working rate, energy consumption, and cavitation development of pumps and hydraulic systems. Dimensional stability of the machine tool’s aluminum casting directly affects the machine tool’s accuracy retention life.
It is important to keep in mind the following parameters while die-casting aluminum:
1. After age, the billet has passed the hardness, and the profile is no longer so simple and tortuous, but special care must be taken while storing it because of the treatment it received to improve its outward look. Avoid violent up and down shaking while lifting the material at both ends; this will avoid the aged metal profile from being twisted and bent.
2. This connection between extrusion and frame is equally crucial. The metal profile will be framed after being sawn to a certain length. The framer should consider whether or not the material is big or tiny, and whether or not it uses a tube or a plane die. Lifting both ends of a huge object or an object with tubes is a cumbersome process, whereas lifting both ends of a tiny object or an object drawn out by a plane die is a straightforward process. Now is the time to frame the elements from both ends in toward the middle. Shutters, window panes, glands, etc., should be placed on the aging profiles and hoisted into the frame even if they are not readily accessible.
3. The straightening process after extrusion is a crucial link in the chain that leads to the production of complex profile twists and turns. When straightening, employees should be mindful of the force they use. Excessive force might cause profiles to distort, neck, orange peel, etc. If not applied with sufficient power, the profile may twist and turn instead of being straightened.