Shape carving 10mm-50mm aluminum relief crafts Aluminum relief carving aluminum plate is a kind of metal sculpture that carves a low fluctuation image on the plane. It is an artistic embodiment between round carving and painting. Its spatial structure can use a three-dimensional shape or some plane shape, which can not only be attached to a certain carrier but also exist relatively immediately. The two-dimensional or planarity of aluminum relief sculpture after body tightening treatment. The relief technology used is mainly line, supplemented by surface; Combined with relief, thin relief, and shallow relief. The mature technology of Yin relief, line engraving and hollowing out. The spatial shape of aluminum plate relief sculpture is the so-called compact space between the two-dimensional virtual space possessed by painting and the three-dimensional solid space possessed by round sculpture. The compact space reduces the free development of aluminum plate relief space. With the support of plane scenery, the sense of entity of round sculpture is weakened and adopted more.
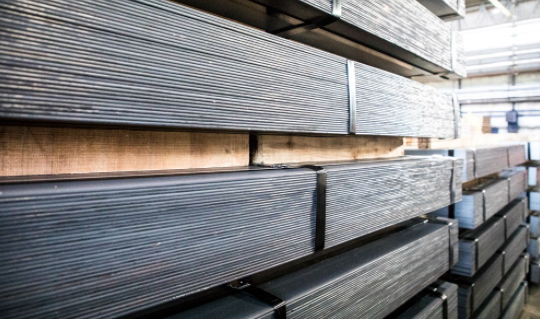
The Casting Process Of Zinc Alloy Crafts
Based on the product technology accumulated over the years, ball screw bearings are managed by strict quality assurance system from the material, thermal external treatment, manufacturing, inspection to shipment, so they have high reliability In order to adapt to various purposes, the ball screw bearing of advertising engraving machine provides a wide range of standardized products. The circulation modes of balls include circulating conduit type, circulator type, and end cover type. The preloading methods include positioning preloading (double nut preloading, position preloading) and constant pressure preloading. The appropriate type can be selected according to the purpose. The screw rod has an accurate ball screw with high-precision grinding (precision is divided into 6 grades from co-c7) and cold-rolled ball screw bearing formed by high-precision cold rolling (precision is divided into 3 grades from C7-C10).
In addition, in order to meet the urgent need of users for delivery, there are also the prices of finished products that have been processed at the shaft end, semi-finished products that can be processed at the shaft end freely, and cold-rolled double headstone engraving machines. And aluminum-based alloys. The main alloy elements are copper, silicon, magnesium, zinc, and manganese, and the secondary alloy elements are nickel, iron, titanium, chromium, lithium, etc. Aluminum alloy has low density, high strength, close to or higher than excellent steel, good plasticity, and can be processed into various profiles. It has excellent conductivity, thermal conductivity, and corrosion resistance. It is widely used in industry, and its usage is only second to that of steel.
Aluminum Alloys Divided Into Two Categories
Cast aluminum alloy, used in as cast state; Deformed aluminum alloy can withstand pressure processing, and its mechanical properties are higher than those of as cast. It can be processed into aluminum alloy materials of various shapes and specifications. It is mainly used for manufacturing aviation equipment, daily necessities, building doors, and windows, etc. An alloy composed of zinc-based and other elements. Commonly added alloy elements include aluminum, copper, magnesium, cadmium, lead, titanium, etc. Zinc alloy has a low melting point, good fluidity, easy fusion welding and brazing
Casting Process Of Zinc Alloy Crafts
General term for aluminum-based alloys. The main alloy elements are copper, silicon, magnesium, zinc and manganese, and the secondary alloy elements are nickel, iron, titanium, chromium, lithium, etc. Aluminum alloy has low density, high strength, close to or higher than excellent steel, good plasticity, and can be processed into various profiles. It has excellent conductivity, thermal conductivity, and corrosion resistance. It is widely used in industry, and its usage is only second to that of steel. Aluminum alloy is divided into two categories: cast aluminum alloy, which is used in as cast state; Deformed aluminum alloy can withstand pressure processing, and its mechanical properties are higher than those of as cast. It can be processed into aluminum alloy materials of various shapes and specifications. It is mainly used for manufacturing aviation equipment, daily necessities, building doors, and windows, etc.
An Alloy Composed Of Zinc Based And Other Elements
Commonly added alloy elements include aluminum, copper, magnesium, cadmium, lead, titanium, etc. Zinc alloy has a low melting point, good fluidity, easy fusion welding, brazing and plastic copper-clad aluminum row bank loan processing, corrosion resistance in the atmosphere, easy recovery and re-casting of residual wastes, and die casting are important processes in the processing of EPC equipment. Sometimes there will be some defects after this work, which need to be repaired. What should be done with this process?
1. Preparation before welding repair. Carefully recover the defects to be repaired, mark the position, and completely remove all defects. Under the condition of ensuring full penetration, the size of the groove shall be reduced as far as possible, and the welding equipment and welding materials must be prepared and dried.
2. Determine the method of welding. The welding method shall be reasonably selected according to the structure and size of EPC equipment, defects, and whether the processing is required after welding repair.
3. Welding repair process parameters. During arc cold welding, DC reverse connection, short arc and intermittent welding shall be adopted. Under the condition of a good turnout, small current and fast welding shall be adopted, and the temperature of the repair welding area shall generally be lower than 60 ℃.
4. Welding shield inspection and heat treatment. After welding, check whether there are defects in the repair welding area and repair welding
Casting Method Of Babbitt Bearing Bush
In the maintenance workshop, the worn Babbitt alloy bearing bush is often re-cast with a new lining and then continue to be used. The technological process includes preparation of bottom pad, melting of Babbitt alloy, clamping, casting and inspection of the bottom pad. The working experience of our factory over the years is summarized as follows.
Preparation of Bottom Tile
1. Melt the old Babbitt alloy lining
Clean up the old bearing bush, and then heat the back of the Bush evenly on the carbon furnace. When heated to 250 ~ 300 ℃, the tin coating begins to soften, gently knock down the alloy layer with tools, and then remove the remaining alloy with shovels, scrapers and other tools.
2. Cleaning of bottom tile surface
After removing the alloy layer, check whether the surface of the bottom tile to be tinned is clean. If it is not clean, it will make tinning difficult and the bonding quality between the alloy and the bottom tile is difficult to guarantee. If there is dirt or oxide on the tinned surface of the bottom tile, sand and anti-corrosion zinc rod can be used. There are many kinds of zinc alloys and different classification methods. According to habits and application methods, there are roughly three classification methods.
Classification By Alloy Composition
Zinc alloys can be divided into four categories according to their composition: Zn Al system, Zn Cu system, Zn Pb system, and Zn Pb al system. Zn Al alloys generally contain a small amount of Cu and Mg to improve the hardness and corrosion resistance. Zn Cu alloys generally also contain Ti, also known as Zn Cu Ti alloys. This alloy is a creep-resistant alloy. Sometimes a small amount of Cr is added to further improve the creep resistance. Zn Pb alloys are generally used for punching battery shells and can be made into various hardware and sports equipment.
Various Casting Process Of Zinc Alloy Crafts
Material is an economic entity mainly engaged in industrial materials. Equipped with an advanced electric display Vickers hardness tester, accurate slitting and shearing equipment, and advanced engineering and technical personnel, we provide customers with high-quality batching and processing services. Mainly engaged in the following materials:
1. Magnesium alloy plate – aviation materials imported from the United States, mainly AZ31, AZ91, and MB8. Thickness: 0.4mm-200mm—— High standards ensure no sand holes and cracks.
2. Magnesium alloy bar – supply specification is Φ 10mm – 1 specification. Other specifications need to be customized in advance.
3. Special material for electrolysis in water plant
4.AZ91D magnesium ingot – can be ordered in small quantities
5. Magnesium rod specially used for extrusion —- bar for extrusion.
6. Magnesium alloy oxide board —– the supply specifications of the following colored samples are based on the actual standard, which can be customized and increased advertising woodworking multi-head crafts antique furniture carving machine and small automatic three-dimensional relief machine
Preparation, Mastery And 4 Inspections Before Casting
1. Check the sand mold: whether the box clamp or bolt is tightened; Whether the amount of pressed iron is sufficient and whether the placement position affects the pouring operation; Whether the gate cup or gate ring is placed stably. So as to avoid fire during the pouring
2. Check whether the ladle is dried and preheated; Whether the lining is complete; Whether the quantity is sufficient and whether the operating mechanism of the lifting bag is flexible and reliable
3. Check the thermal insulation materials and appliances: whether the thermal insulation, slag accumulation, and ignition materials are ready, and whether the materials and appliances required to prevent fire escape are in place. In order to make the tense pouring operation busy and not disorderly and orderly
4. Site inspection: there shall be no ponding on the ground of the pouring site, and the pouring channel must be unblocked for casting and slag removal
After the molten metal is discharged from the furnace, the molten slag on the liquid level shall be removed from the back or side of the nozzle and covered with thermal insulation slag accumulating material. Do not damage the coating layer on the nozzle to affect the pouring. Before pouring and zinc alloy handle dry streamer gold/zinc alloy die casting fine polishing machine zinc alloy dry polishing machine zinc alloy die castings are more and more recognized, the scope of application is more and more extensive, and the method of the natural surface treatment process is constantly updated. The dry centrifugal polishing machine aims at accurate grinding operations such as removing burrs, grinding and cleaning, finished product surface polishing, removing oxide film, dirt, and corrosion, sintering trace treatment, etc. for zinc alloy handle, zinc alloy die casting, zinc alloy anti-theft window, various zinc alloy precision casting accessories; It mainly makes the inner hole, dead corner and some concave joints of hardware workpiece play an obvious polishing effect of deburring, scale removal and polishing. Fast processing speed, simple and safe operation, low use cost and low consumption of consumables.