When processing sheet metal parts or designing sheet metal components, encountering problems such as aluminum plate cannot be bent or cracking during bending is common. Whether aluminum plate can be bent depends mainly on the material state. The states are divided into fully hard, half hard, and soft (usually soft state is called O state). Fully hard bending effect is basically not good (aluminum plate state such as H18, H19, H38, etc. are all fully hard). Aluminum plates in the half-hard state can basically be bent (such as H24). O-state bending is definitely not a problem, but because it is too soft, it is basically less used for bending in this state. When processing sheet metal parts, the situation of using pure aluminum materials is still very rare. Basically, all are aluminum alloys (because the hardness of pure aluminum is not very good). The selection of aluminum alloy for sheet metal parts can use 3003, 3005, 5052 and other half-hard state for sheet metal bending parts. If 6061, 2024, 7075 are used, they cannot be bent because the hardness is too high, especially T6 state. They cannot be bent unless they are heated and then bent. The difference between good aluminum plates and poor aluminum plates lies in oxidation performance, tolerance, surface effect, crystal accuracy, and uniform stability. There is not much difference in bending effect alone.
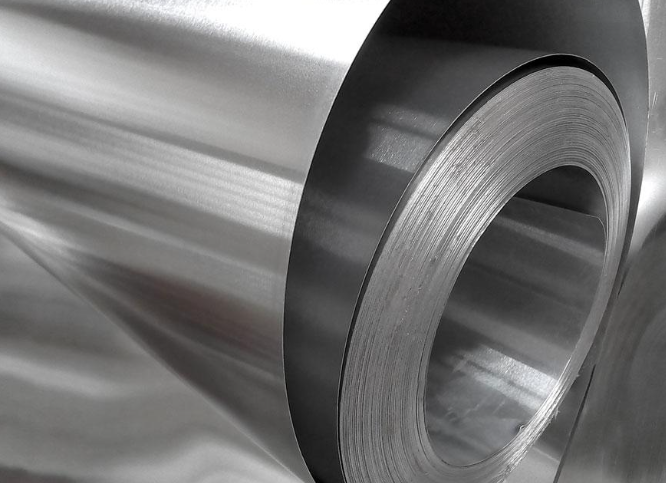
Best Aluminum For Bending
The bending coefficient of aluminum plate is basically similar to that of carbon steel. A simple algorithm can be used: plate thickness x 1.6. That is to say, for a 1mm thick 5052 aluminum plate bending, the outermost dimension plus the outermost dimension minus 1.6mm is the unfolded length. Try to bend against the grain when bending, and aluminum plates have rolled grain patterns. The best intersection of bending tools and rolled grain patterns is 90 degrees, which is not easy to crack.
1. 1000 Series
Represents 1050 1060 1070 1000 series aluminum plates are also called pure aluminum plates, and the 1000 series is the series with the highest aluminum content in all series. The purity can reach over 99.00%. Due to the absence of other technical elements, the production process is relatively simple, and the price is relatively cheap. It is currently the most commonly used series in conventional industry. Most of the products circulating in the market are 1050 and 1060 series. The last two digits of the 1000 series aluminum plate determine the minimum aluminum content of this series. For example, the last two digits of the 1050 series are 50. According to the international grade naming principle, the aluminum content must reach 99.5% or more to be qualified products.
The aluminum alloy technical standard (GB/T3880-2006) also clearly stipulates that the aluminum content of 1050 must reach 99.5%. Similarly, the aluminum content of the 1060 series aluminum plate must reach 99.6% or more. Typical grades and uses of the 1000 series: Pure aluminum plate 1060 is mainly used in occasions requiring high corrosion resistance and formability, but low-strength parts, such as chemical equipment, ship equipment, railway tank cars, conductive materials, instrument materials, welding rods, etc.
2. 2000 Series
The representative is 2A16 (LY16) 2A06 (LY6) The characteristic of the 2000 series aluminum plate is high hardness, among which copper belongs to the highest content, about 3-5%. 2A12 aluminum alloy is a kind of high-strength hard aluminum that can be heat-treated; 2A12 aluminum alloy spot welding has good weldability, and tends to form intergranular cracks when gas welding and argon arc welding; 2A12 aluminum alloy has good machinability after cold work hardening. Corrosion resistance is not high, it is often treated with anodizing and painting methods or surface-coated with aluminum layer to improve corrosion resistance. The 2000 series aluminum plate belongs to the aviation aluminum material, which is not commonly used in conventional industry at present.
3. 3000 Series
Aluminum plate 3003 3003 3A21 is the main one. It can also be called rust-proof aluminum plate. The production process of 3000 series aluminum plate is excellent. The 3000 series aluminum plate is mainly composed of manganese as the main component. The content is between 1.0-1.5. It is a series with good rust-proof function. It is commonly used in wet environments such as air conditioners, refrigerators, and car bottoms. The price is higher than that of the 1000 series. It is a commonly used alloy series.
Typical grades and uses of the 3000 series: 3003 aluminum is mainly used for processing parts that require good forming performance, high corrosion resistance, or good weldability, or require higher strength than 1000 series alloys, such as tanks and tanks for transporting liquids, pressure tanks, storage devices, heat exchangers, Chemical equipment, aircraft fuel tanks, oil pipelines, reflection panels, kitchen equipment, washing machine cylinders, rivets, welding wires. 3004 aluminum requires higher parts than 3003 alloy, chemical products production and storage equipment, thin plate processing parts, building panels, cable pipes, sewers, various lamp parts.
4. 4000 Series
The representative is 4A01 The 4000 series aluminum plate belongs to the series with a higher silicon content. Usually, the silicon content is between 4.5-6.0%. It belongs to building materials, mechanical parts, forging materials, welding materials; low melting point, good corrosion resistance, product characteristics: heat resistance, wear resistance.
5. 5000 Series
It represents 5052.5005.5083.5A05 series. The 5000 series aluminum plate belongs to a relatively commonly used alloy aluminum plate series, with magnesium as the main element, and the magnesium content is between 3-5%. It can also be called aluminum-magnesium alloy. The main features are low density, high tensile strength, and high elongation. Under the same area, the weight of aluminum-magnesium alloy is lower than that of other series.
6. 6000 Series
Represents 6061, which mainly contains magnesium and silicon. Therefore, it combines the advantages of 4000 series and 5000 series. 6061 is a cold-processed aluminum forged product, suitable for applications with high requirements for corrosion resistance and oxidation resistance. Good workability, excellent interface characteristics, easy coating, and good processability.
Can be used on low voltage weapons and aircraft joints. General features of 6061: excellent interface characteristics, easy coating, high strength, good workability, and strong corrosion resistance. Typical uses of 6061 aluminum: aircraft parts, camera parts, couplers, ship accessories and hardware, electronic accessories and joints, decorative or various hardware, hinge heads, magnetic heads, brake pistons, hydraulic pistons, electrical accessories, valves and valve parts .
7. 7000 Series
Represents 7075, which mainly contains zinc. It also belongs to the aviation series. It is an aluminum-magnesium-zinc-copper alloy. It is a heat-treatable alloy. It is a super-hard aluminum alloy and has good wear resistance. 7075 aluminum plate is stress-relieved and will not deform or warp after processing. All ultra-large and ultra-thick 7075 aluminum plates have been ultrasonic tested to ensure there are no blisters or impurities. 7075 aluminum plate has high thermal conductivity, which can shorten molding time and improve work efficiency.
The main feature of 7075 is hardness. 7075 is a high-hardness, high-strength aluminum alloy commonly used in manufacturing aircraft structures and futures. It requires high-stress structural parts and mold manufacturing with high strength and strong corrosion resistance.
8. 8000 Series
The more commonly used one is 8011, which belongs to other series. The aluminum plate whose main function is to make bottle caps is also used in radiators, most of which are aluminum foil. Not commonly used.