LM6 aluminum is a high-silicon casting alloy widely recognized for its exceptional corrosion resistance, excellent fluidity, and superior castability, especially in intricate or thin-walled components. In this LM6 aluminium guide, we explore the composition, properties, equivalent, price and differences between LM6 and LM9.
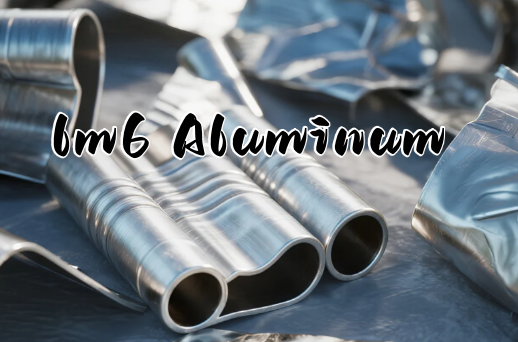
What’s LM6 Aluminum – LM6 Meaning
LM6 aluminum is a high-silicon aluminum casting alloy known for its excellent corrosion resistance, fluidity, and castability, especially in intricate or thin-walled castings. It typically contains around 10–13% silicon and small amounts of other elements like iron and copper. LM6 is commonly used in marine, automotive, and architectural applications where resistance to atmospheric and saltwater corrosion is crucial. Its good thermal conductivity and resistance to hot cracking make it ideal for pressure die casting, gravity die casting, and sand casting processes. However, it has relatively low mechanical strength compared to other aluminum alloys unless heat treated or modified.
Aluminum LM6 Composition
LM6 is a high-silicon aluminum casting alloy (also known as Al-Si12) widely used in foundries for its excellent casting characteristics and corrosion resistance. lm6 aluminium alloy composition is:
Element | Percentage (%) |
---|---|
Silicon (Si) | 10.0 – 13.0 |
Iron (Fe) | ≤ 0.6 |
Copper (Cu) | ≤ 0.1 |
Magnesium (Mg) | ≤ 0.1 |
Zinc (Zn) | ≤ 0.1 |
Manganese (Mn) | ≤ 0.5 |
Nickel (Ni) | ≤ 0.1 |
Tin (Sn) | ≤ 0.05 |
Lead (Pb) | ≤ 0.05 |
Titanium (Ti) | ≤ 0.2 |
Aluminum (Al) | Remainder (Balance) |
Aluminium LM6 Propeties
Mechanical Properties (As-Cast):
Tensile Strength: ~130–160 MPa
Yield Strength: ~70 MPa
Elongation: ~1–3%
Brinell Hardness: ~50–60 HB
Modulus of Elasticity: ~71 GPa
Thermal Properties:
Melting Range: 575–585 °C
Thermal Conductivity: ~150–180 W/m·K
Coefficient of Thermal Expansion: ~21 µm/m·°C
Casting & Processing:
Excellent castability, especially in intricate and thin-walled parts
Excellent fluidity – ideal for sand, die, and gravity casting
Not heat treatable – mechanical strength is improved by modifying the alloying process rather than solution treatment
Corrosion Resistance:
Outstanding resistance to seawater and chemical environments
Suitable for marine, automotive, and architectural applications
Machinability & Weldability:
Machinability: Fair (due to high silicon content)
Weldability: Good with gas and arc welding, but not suitable for brazing or soldering
LM6 Equivalent Material
LM6 is a high-silicon aluminum casting alloy primarily used in the UK and follows the British Standard (BS 1490). Its lm6 equivalent material in other standards are:
Standard | Equivalent Alloy |
---|---|
BS 1490 (UK) | LM6 |
ASTM (USA) | A413.0 / A356.0 (closest match) |
EN / ISO (Europe) | EN AC-44100 (AlSi12) |
DIN (Germany) | G-AlSi12 (old: G-AlSi12Fe) |
JIS (Japan) | AC-4B |
Note: While lm6 aluminum equivalent is similar in silicon content and casting properties, exact mechanical properties and corrosion resistance may vary slightly due to differences in minor alloying elements and impurity limits. Always consult material datasheets for precise application requirements.
Advantages of LM6 Material
Thanks to its high silicon content (around 10–13%), LM6 offers outstanding resistance to corrosion, especially in marine and outdoor environments. LM6 is ideal for complex shapes due to its high fluidity, making it suitable for pressure die casting and sand casting. This makes it suitable for use in hazardous environments, such as oil refineries and chemical plants. The alloy offers good wear properties, especially when treated or reinforced, increasing its durability in service. While as-cast LM6 can be gummy, it machines reasonably well when heat treated or aged.
Applications of Aluminium Alloy LM6
Automotive Parts: Used for engine components, housings, and gearboxes due to its light weight and corrosion resistance.
Marine Industry: Ideal for boat parts, pumps, and valves exposed to salt water.
Electrical and Lighting Fixtures: Its corrosion resistance and ability to hold fine details make it great for fittings and enclosures.
General Engineering: Used for intricate and thin-walled castings in equipment requiring high dimensional accuracy.
Food and Chemical Equipment: Its non-reactive and non-corrosive nature makes it suitable for certain food-grade applications.
LM6 Aluminium Price
The current price for LM6 aluminum in the USA market is roughly £6.50 per kilogram (about $8–9 USD/kg) according to a UK supplier listing that includes international orders. For comparison, commodity aluminum is trading around $2.60 USD/kg (~$2,600 per tonne) on global exchanges. The higher price for LM6 reflects its status as a specialized aluminum–silicon–lithium casting alloy, which offers improved strength and corrosion resistance. As a result, sourcing LM6 typically incurs a premium over standard aluminum, with U.S. buyers commonly paying in the $8‑10/kg range depending on supplier and order volume.
LM6 vs LM9 Aluminium Alloy: What’s the Difference?
LM6 and LM9 are both aluminum casting alloys commonly used in die casting and sand casting, but they differ significantly in composition, mechanical properties, and applications:
Feature | LM6 | LM9 |
---|---|---|
Primary Alloying Element | High Silicon (approx. 10–13%) | High Silicon with Nickel (approx. 4–5%) |
Composition | Al–12Si (with small amounts of Mg, Fe, Cu) | Al–12Si–4Ni–0.5Mg (plus Fe, Cu) |
Corrosion Resistance | Excellent, especially in marine environments | Good, but slightly less than LM6 |
Mechanical Strength | Lower than LM9 | Higher tensile and fatigue strength due to Ni |
Wear Resistance | Moderate | Better than LM6 due to added Nickel |
Castability | Excellent (fluid, low shrinkage) | Good, but may require more controlled casting |
Heat Resistance | Fair | Better heat resistance (thanks to Nickel) |
Applications | Marine parts, pump housings, cookware, streetlight casings | Engine components, pistons, cylinder heads, brake parts |
LM9 vs LM6, Which should you Choose?
Choose LM6 when you need excellent corrosion resistance, especially in marine or outdoor applications. Choose LM9 when you need better mechanical strength, wear resistance, and heat resistance, especially in automotive and engineering applications.
lm9 Chemical Composition vs lm6 chemical composition
LM9 (Al-Si-Cu)
Element | % Composition (Approx.) |
Silicon (Si) | 11.0 – 13.0% |
Copper (Cu) | 0.5 – 1.5% |
Magnesium (Mg) | 0.1 – 0.6% |
Iron (Fe) | ≤ 1.0% |
Manganese (Mn) | ≤ 0.5% |
Nickel (Ni) | ≤ 0.5% |
Zinc (Zn) | ≤ 1.0% |
Aluminum (Al) | Balance |
LM6 (Al-Si)
Element | % Composition (Approx.) |
Silicon (Si) | 10.0 – 13.0% |
Copper (Cu) | ≤ 0.1% |
Magnesium (Mg) | ≤ 0.1% |
Iron (Fe) | ≤ 0.6% |
Manganese (Mn) | ≤ 0.5% |
Nickel (Ni) | ≤ 0.1% |
Zinc (Zn) | ≤ 0.1% |
Aluminum (Al) | Balance |
What is the Color Code for Aluminium LM6 Alloy?
According to BS1490:1988, the colour code for Aluminium LM6 is yellow. This identification helps distinguish LM6 aluminium alloy from other aluminum casting grades during manufacturing and inspection.