Although China is not the inventor of EPC technology, it is the country with the largest EPC production and one of the countries with relatively mature EPC technology applications. Today, we are going to talk about the prospect of EPC casting.
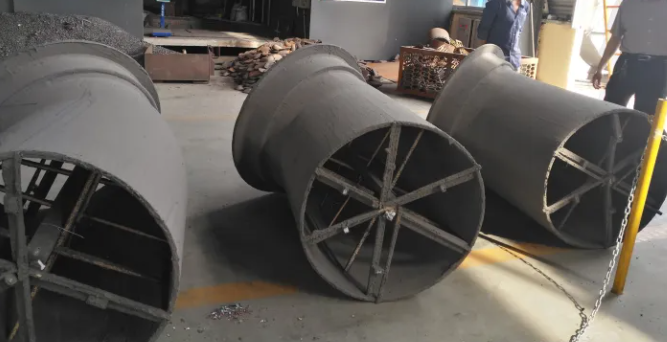
At present, China’s EPC casting output is about 5 million tons, accounting for 10% of China’s casting output. The research on EPC technology in China originated in Shanghai. As early as 1970, the Shanghai foundry had poured 52 tons of steel castings and 32.5 tons of iron castings in 1974. Pouring such large EPC castings can only be realized by top EPC foundries up to now. Although the lost foam technology was invented by the American Sloan in 1956. But between 1970 and 1980, China’s lost foam technology was no worse than that of the United States.
In fact, it was Chinese foundry scholars who laid a solid foundation in that period that gave China’s lost foam casting its strength and position in the world today. China follows the United States closely, and the Western countries are heavily blocked. Mr. Liang Guangze, a casting expert, began to study EPC process at Shanghai Machinery Manufacturing Technology Research Institute in 1965. With his rich casting knowledge, Mr. Liang has made great achievements in EPC field. The largest EPC steel castings and EPC iron castings in China mentioned in the above article were completed under the leadership of Mr. Liang.
Since 1980, China has entered the era of reform and opening up, and private foundries have sprung up everywhere. The construction of EPC foundry has also entered a new era. Private EPC foundries began to increase. However, private enterprises lack professional EPC technicians. In order to obtain talents, private enterprises began to recruit talents from state-owned casting enterprises at high prices. At that time, the technicians of state-owned casting could only earn dozens of yuan a month. Once you get to a private enterprise, you can get more than ten times the salary. The market economy has led some EPC technicians to the market. Some technicians entered private enterprises, while others started their own businesses.
In the first ten years of reform and opening up, many controls in the economic field were liberalized, and everything looked to money. Under this idea, it is more and more serious to pay more attention to business, less attention to research and development, and less attention to technology. Therefore, it was said that it was better to sell tea eggs than to make atomic bombs. This income imbalance has led to the loss of a large number of technical researchers. This has to say the loss of China’s scientific research. In terms of EPC, a decade long technological stagnation has widened the gap between China’s EPC technology and that of developed countries.
Outside, there was a sound of ticket speculation. In the EPC Research Institute, a state-owned enterprise, many technicians began to go into the sea, stirred by the sound of ticket speculation outside. During the period from 1990 to 2000, the world’s EPC has entered the era of machinery and automation. Developed countries, mainly the United States, Japan, Germany and Britain, have made leaps and bounds in EPC. The application of EPC is more and more extensive. It is also called environmental protection casting and green casting.
During this period, domestic EPC also developed rapidly. By 2000, there were nearly 200 EPC foundries registered by industry and commerce. Although many small and medium-sized foundries were not registered as EPC foundries, they were also on the EPC production line. In 2000, there were about 500 foundries with EPC production lines in China.
Entering the 21st century, that is, from 2000 to 2010, this period is the blowout period of China’s EPC foundry. From 2000 to 2010, a large number of domestic foundries started to build EPC production lines. This is related to China’s increasing awareness of environmental protection after its accession to the WTO. In the 21st century, the contradiction between industrial production and environmental protection is growing. Environmental protection issues in the foundry industry have gradually been paid attention to. The state began to intentionally guide the foundry industry to transform into a green foundry with low pollution and high output.
In addition, the development of EPC technology makes the cost and quality of EPC castings more and more outstanding. In order to pursue greater casting profits. Domestic foundries follow the trend to launch EPC production lines. However, the domestic EPC technology began to lag behind the developed countries after the 1980s. The research and development of materials and equipment such as white mold, EPC equipment, coating and adhesive is slow. It can’t keep up with the rapidly increasing speed of EPC foundry.
More importantly, there is a shortage of talents in EPC technology, which leads to the blind start syndrome of newly launched EPC casting. Although many foundries have been on the EPC production line, they cannot produce normally and the scrap rate remains high. The EPC production line launched can not only bring profits to the foundry, but also become the source of losses.
So the fanatical pursuit of lost foam casting began to enter a period of reflection. However, from 2000 to 2010, the number of industrial and commercial registered EPC foundries in China rose to more than 500, and the number of non industrial and commercial registered EPC foundries exceeded the number of registered factories. By 2010, the number of actual EPC foundries in China exceeded 1000. During the five years from 2010 to 2015, the speed of EPC has decreased. The EPC production line is no longer crazy.
China has started to develop a concentration area of EPC industry.
For example, Pingyao, Shanxi Province, has begun to form a gathering area of EPC with supporting motor shells as the main industry. Its EPC casting output is close to 2 million tons.
The concentrated EPC industry has made the EPC in Pingyao, Shanxi better developed. A large number of EPC foundries are concentrated in one area, so that material matching, technical services, and equipment manufacturing are rising simultaneously. At the same time, comprehensive costs have been reduced. Pingyao lost foam casting has shown the Chinese foundry people the great advantages of lost foam casting.
1、 Batch Advantages
2、 Cost advantage
3、 Quality advantage
4、 Environmental advantages
It is these four advantages that make Pingyao become a world supplier in the field of motor shell casting. In China, Pingyao motor shell accounts for more than 55% of the market, and in the world, Pingyao motor shell accounts for 25% of the market share. Pingyao EPC has become a model of EPC technology in China and a beneficiary of EPC technology.
However, the life of EPC foundries scattered in various provinces of the country is relatively worse than that of Pingyao. Because of dispersion, the matching rate of upstream and downstream materials is low and the material cost is high. Moreover, due to the lack of technology, the waste rate has been high, which makes many foundries stop using EPC production lines and return to clay sand process.
Most foundries that abandoned the EPC production line lost a lot of money. This is a bloody lesson for the foundry. If China’s environmental protection storm does not come, EPC may enter a silent period in China. However, since 2016, China’s environmental protection has entered a super rectification period. Environmental protection began to say no to the traditional clay sand process. In many traditional casting production areas, it is explicitly stipulated to eliminate clay sand process to reduce the production of casting solid waste.
The lost foam process was once again respected by the foundry.
From 2016 to the first half of 2019, many foundries in Zhejiang, Jiangsu, Shandong, Anhui and Henan started to use EPC process. From the perspective of environmental protection and long-term development trend of casting, the proportion of EPC in the casting process will gradually increas