What Is The Effect Of Temperature On Magnesium Alloy Die Casting?
In this guide, we will cover the features of magnesium alloy die casting and explain the effect of temperature on magnesium alloy die casting.
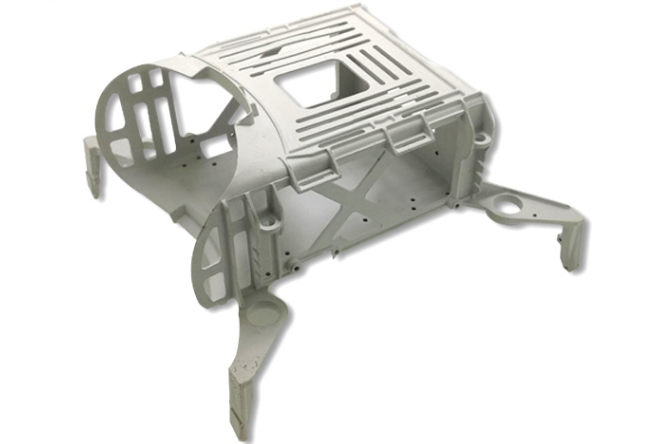
Magnesium Alloy Die Casting
Magnesium alloy is the lightest metal structural material, with a density of 1.75 ~ 1.90g/cm3. Its specific strength is higher than that of aluminum alloy and steel, and slightly lower than that of fiber-reinforced plastics with the highest specific strength. It has excellent machining performance, easy processing and low processing cost, and the processing energy is only 70% of that of aluminum alloy. Its corrosion resistance is much better than that of low carbon steel, which has exceeded that of die-casting aluminum alloy A380. Its vibration damping and electromagnetic shielding are much better than aluminum alloy. In addition, due to its low density, low melting point, low dynamic viscosity, low specific heat capacity, low phase transformation latent heat and low affinity with iron, magnesium alloy has the advantages of low melting energy consumption, fast mold filling speed, fast solidification speed, short actual die-casting cycle and long die service life. It is very suitable for forming processing with modern die-casting technology, directly prepare thin-walled and complex parts.
Moreover, the performance of magnesium alloy die castings is excellent, and the effect of replacing steel, aluminum alloy, plastic and other parts under conventional use conditions is very good. While realizing the lightweight of the product, it also makes the product have excellent special functions. After the magnesium alloy die castings are scrapped, they can be directly recycled and reused, which meets the requirements of environmental protection.
Effect Of Temperature On Magnesium Alloy Die Casting
AZ91D is a die cast magnesium alloy with good plastic toughness, certain strength and excellent corrosion resistance at room temperature. When the pouring temperature is 660 ~ 685 ℃, the tensile strength and elongation of AZ91D alloy increase with the increase of pouring temperature; However, it is obvious that the pouring temperature has a great influence on the elongation; When the pouring temperature is higher than 685 ℃, the tensile strength and elongation decrease with the increase of pouring temperature. When the pouring temperature is 700 ℃, the elongation value is abnormal, but the general trend of elongation is decreasing. When the pouring temperature is 660 ~ 680 ℃, the impact toughness and hardness of die-casting magnesium alloy AZ91D increase slightly with the increase of pouring temperature; When the pouring temperature is 680 ~ 700 ℃, the impact toughness and hardness increase greatly with the increase of temperature; When the pouring temperature is higher than 700 ℃, the hardness decreases sharply with the increase of temperature; The impact toughness reaches its peak at 700 ~ 710 ℃, and the impact toughness is likely to decrease with the continuous increase of temperature.
Considering the influence of various factors, when the injection specific pressure is 70MPa, the injection speed is 3.0m/s and the mold temperature is 200 ℃, the effect of pouring temperature on the mechanical properties of AZ91D alloy is studied. It is found that when the pouring temperature is 685 ℃, the mechanical properties of the die-casting sample are the best, the tensile strength can reach 263mpa and the elongation can reach 225%; Too low pouring temperature is not conducive to mold filling, and it is easy to produce defects such as cold shut and insufficient mold filling; If the pouring temperature is too high, it is easy to produce splash, burr and serious shrinkage cavity and porosity defects in magnesium alloy die castings, which reduces the mechanical properties of magnesium alloy die castings and aggravates the thermal impact on the die castings. Therefore, the pouring temperature is 685 ℃.
When other die-casting process parameters are fixed, the effect of mold temperature on the mechanical properties of die-casting magnesium alloy AZ91D. The tensile strength and hardness of die-casting magnesium alloy AZ91D first increase with the increase of mold temperature. When the mold temperature exceeds 200 ℃, it decreases with the increase of mold temperature, but it is obvious that the tensile strength curve changes more violently than the hardness curve. When the tensile strength and hardness reach the maximum, the mold temperature is 200 ℃ and 197 ℃ respectively. Although the elongation of magnesium alloy decreases with the increase of mold temperature, it can be seen that the elongation value changes little in the range of 180 ~ 210 ℃, which shows that the mold temperature has little effect on the elongation of the alloy. The impact toughness of the alloy changes little in the range of 180 ~ 190 ℃, then the impact toughness of the alloy increases with the increase of temperature, and its value is relatively stable at 200 ~ 210 ℃.
To sum up, the influence of die casting mold temperature on the mechanical properties of AZ91D alloy is basically the same as that of pouring temperature. Too low mold temperature will make the cooling speed too fast, resulting in the rapid formation of hard shell on the surface of magnesium alloy die castings, which is not conducive to mold filling and solidification feeding, and is easy to form cold barrier; If the mold temperature is too high, it is easy to cause adhesive strain. The test and analysis show that the influence of die-casting process temperature parameters on the mechanical properties of AZ91D alloy is pouring temperature and mold temperature from strong to weak; When the die-casting process parameters (injection specific pressure 70MPa, injection speed 3.0m/s, mold temperature 200 ℃, pouring temperature 685 ℃) are appropriate, the mechanical properties of die-casting AZ91D alloy can be achieved stably σ b=263MPa, δ 5=225%.
Conclusion
1. AZ91D alloy, the most significant factor is the pouring temperature, followed by the mold temperature; The mechanical properties of die-casting AZ91D alloy can be stably achieved under appropriate die-casting process parameters (injection specific pressure 70MPa, mold temperature 200 ℃, pouring temperature 685 ℃) σ b=263MPa, δ 5=225%。
2. When the metallurgical quality of magnesium alloy is strictly controlled and other conditions are certain, the suitable pouring temperature of die-casting magnesium alloy AZ91D is 685 ℃; The suitable mold temperature is 200 ℃.