Die casting is a type of casting and die forging that is commonly used in the automotive industry. On a specific die casting die forging machine, die casting die forging is done. A low-speed or high-speed casting method is used to fill the mold cavity with liquid metal, and the mold has a moveable cavity surface. The shrinkage cavity and porosity flaws of the blank are eliminated, and the internal structure of the blank reaches the broken grains in the forging state, by pressurizing and forging the liquid metal during the cooling process. Almost all of the blank’s mechanical qualities have been enhanced. This procedure also produces blanks with a surface polish of grade 7 (Ra1.6), the same as that generated by cold extrusion or machining, and this surface features a metallic shine. Die casting and die forging processes are referred to as “limit forming processes” instead of “no cutting and less allowance forming processes” for this reason. Another benefit of the die casting and forging process is that it can also employ deformation alloy and forging alloy to manufacture pieces with more intricate structures. Hard aluminum, ultra hard aluminum alloy, and wrought aluminum alloy (LY11, LY12, 6061, 6063, LYC, LD, etc.) are among the alloy grades available. They have a far higher tensile strength than cast alloys, which has a good influence on aluminum alloy automotive wheels, frames, and other parts that need high-strength, impact-resistant materials. Here is everything you should know about demoulding slope for zinc alloy die castings.
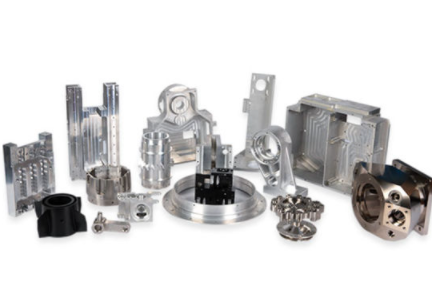
What Is The Demoulding Slope For Zinc Die Castings
Die casting is a shortened form of die casting. Alloy liquid is cast by pouring it into an alloy chamber, where the steel mold is filled at fast speed, and the alloy liquid solidifies under high pressure to make the casting. Die casting differs from other casting procedures in that it uses high pressure and rapid movement. In most cases, the metal liquid fills the mold cavity at speeds of 10-50 M/s, however it has been seen to go as high as 80 M/S. (the linear speed of introducing the mold cavity through the inner gate – the speed of the inner gate). With such a quick time for loading the metal liquid, it is possible to completely fill the mold cavity in about 0.001-0.002 seconds (depending on the size of the casting). Die-casting manufacturing relies on three main components: a die casting machine, a die-casting alloy, and a die-casting die. Because of its organic and thorough application of these three characteristics, the process known as die casting is able to consistently create high-quality castings with good appearance and internal quality, as well as castings that satisfy the specifications of drawings or agreements.
A machine for making castings
Die casting machine categorization It’s possible to categorize the pressing chamber temperatures of a die casting machine into two types: hot and cold. These machines can be split into vertical, horizontal, and full-vertical cold chamber die-casting machines based on their mold locations. Cold chamber vertical die casting machine entire vertical cold chamber
The clamping force is one of the most important die casting machine characteristics (KN) The maximum opening distance between the KNC moving and setting plates (measured in KN) – the distance between the moving and setting plates of the MMD system moving plates of the MME – the distance (horizontal vertical) between MMF bars Bigger bar diameters are available on the MMG line – The jacking force of MMH is – kni expulsion – Position for MMJ injections (center, eccentricity) Amount of Zn, Al, and Cu poured into the MMK main metal chamber () Note: Installation dimension drawings for both the moveable and permanent plates must be given in addition to the Sn casting’s projected surface area under various pressure situations on the separating surface.
Due to mold materials and other issues, ferrous metal (steel, iron, etc.) is rarely utilized in die castings at this time. Die casting alloy Non-ferrous alloy die castings most commonly employ aluminum alloy, followed by zinc alloy. An overview of the current state of die-casting non-ferrous metals is provided below.
Die casting non-ferrous alloy classification Lead alloy with inhibited shrinkage and mixed shrinkage but no shrinkage- 0.2-0.3% 0.3-0.4% 0.4-0.5% low melting point alloy tin zinc alloy 0.3-0.4 % 0.4-0.6 % 0.6-0.8 % aluminum silicon non-ferrous alloy die casting 0.3-0.5% 0.5-0.7% 0.7-0.9% a metal alloy of aluminum and other elements a system made of aluminum, copper, and magnesium high melting point alloy aluminum zinc system magnesium alloy 0.7-0.9 percent 0.9-1.1 percent copper alloy. For die casting alloys, the temperature at which they should be cast Casting wall thickness ranges from 3mm to >3mm, with the latter being the most common. a construction that is both simple and complicated
-Anodized aluminum is an alloy of aluminum and System of aluminum and silicon at 610-650 degrees Celsius, 640-680 degrees Celsius, 600-620 degrees Celsius, or even higher
Aluminum copper system 630-660°C 660-700°C 600-640°C 630-660°C
- The aluminum-magnesium temperature ranges from 640-680 degrees Celsius to 660-700 degrees Celsius to 640-670 degrees Celsius to 650-690 degrees Celsius.
- Temperatures in the range of 580 to 680 °C are used for aluminum zinc alloys.
- Zinc alloy 420-440 °C 430-450 °C 400-420 °C 420-440 °C
- Alloy of magnesium 640-680 °C 660-700 ℃ 640-670 ℃ 650-690 ℃
- Brass made of copper alloy temperatures ranging from 910-930 degrees Celsius to 940-980 degrees Celsius and from 900 to 950 degrees Celsius
- 930-970°C 910-940°C 910-940°C 910-940°C Silicon brass
For the most part, the temperature of molten metal in a furnace holding furnace is used to measure casting temperature. To avoid coarse grains, the zinc alloy casting temperature should not be higher than 450 °C. 2、 It is one of the three main components in die casting manufacture. Die casting manufacturing cannot proceed without a die with a proper and appropriate structure, and this plays a significant part in assuring the quality of the casts (off machine qualification rate). Die-unique casting’s properties necessitate that the mold be used as a starting point for fine-tuning the process parameters in order to produce high-quality castings. Die-casting mold design is an all-encompassing representation of the variables that might affect the process. When the mold design is acceptable, there are fewer issues in the actual manufacturing, and the quality of the casting is great. However, the mold design is a complete waste of time and money. During the design of the casting, for example, the wrapping force of the dynamic fixed mold is basically the same, while the gating system is primarily produced on the fixed mold and placed on the Guannan die casting machine where the punch cannot feed after injection, so it cannot be produced normally and the casting has been stuck to the fixed mold. Even though the mold cavity has a smooth surface, the deep hollow means it still adheres to the mold.
Because of this, mold design requires a thorough examination of the casting structure, familiarity with the operation process of the die casting machine, an understanding of the pressure relief casting machine and process parameters, and an understanding of the filling characteristics under various conditions, so that a mold that is practical and meets the production requirements can be designed. Die-casting dies have exceptionally poor working conditions because of the short filling time and high specific pressure and flow rate of liquid metal, as previously stated. Alternating temperatures can also have a significant influence on the die’s service life. As a general rule of thumb, a die’s service life relates to how long it can be fixed or scrapped before it can no longer be repaired or scrapped owing to natural deterioration under regular usage circumstances and meticulous design and manufacturing. There are three primary types of die failure in real production: thermal fatigue cracking, fragmentation, and corrosion. Die failure can be caused by a variety of factors, including some that are outside the control of the manufacturer (such as casting temperature, whether the die is preheated, the amount of water spray coating, whether the tonnage of the die-casting machine is matched, the die-casting pressure is too high, the inner gate speed is too fast, the cooling water is not opened synchronously with the die-casting production, the type of casting material and the content of Fe, casting size and shape, wall thickness, coating type, etc.).
Also, there are internal causes (such as, for example, the metallurgical quality and forging process of the blank; rationality of die design; rationality of gating system design; internal stress generated during machining of die machine (electric machining); heat treatment process, including various matching accuracy and cleanliness requirements, etc.). The root cause(s) of early die failure must be determined in order to make required alterations in the future. It is common for microcracks to emerge when the mold is repeatedly chilled before use and heated thereafter. This causes repetitive cyclic thermal stress, which damages the mold’s structure and reduces its toughness, leading to microcracks appearing and expanding over time. The expansion of the fracture is accelerated by molten metal being pressed into the crack as it expands. In order to ensure a successful die casting process, the die must be thoroughly warmed at the start of the process. In order to avoid early cracking failure during the die-casting process, the mold must be kept at a specific operating temperature range. Prior to the mold going into production and during the manufacturing process, it’s critical to check for any issues with the internal reasons. Thermal fatigue cracking is the most common cause of die failure in production.
Failure of fragmentation Injection forces cause the mold to break at its most vulnerable point, especially if the scribed lines or electric machining traces on the mold-forming surface are not polished. Otherwise, the small cracks would develop at the clear corners of the molding first. The weakest section. Fracture is more likely when there is a brittle phase at the grain boundary when the grain is coarse. Brittle fracture, on the other hand, causes the crack to spread fast, which is a significant risk to the die’s failure. Consequently, the mold surface must be polished, even if it is in the pouring system, to remove any scratches and machining marks. Additional requirements include strong strength, excellent plasticity, good impact toughness and fracture toughness for the die materials utilized in the production process. ③ Zinc alloy, aluminum alloy, magnesium alloy, and copper alloy, as well as pure aluminum die-casting, are among the most often used die-casting alloys. Among the moderately active metal elements, Zn, Al, and Mg have an excellent affinity for mold materials, notably Al, which is easy to bite the mold Corrosion resistance is improved when the die has a high degree of hardness, whereas it is harmed when the forming surface has soft places. However, in practice, corrosion is limited to a specific area of the mold. As a result, the core and cavity are susceptible to corrosion, while the components with a soft hardness (such as the flanges) are susceptible to die sticking.
The issues and precautions to take when working in the die casting industry:
Gating systems and overflow drainage systems are two examples.
Cold chamber horizontal die casting machine mold sprue requirements: The pressure chamber’s inner diameter should be chosen based on the needed pressure and the pressure chamber’s fullness. The inner diameter deviation of the sprue sleeve should be increased by a few wires compared to the pressure chamber’s inner diameter deviation, so that the punch jamming or substantial wear caused by the non-coaxial inner diameter of the sprue sleeve and the pressure chamber may be avoided. In order to remove the coating from the pressure chamber, the sprue sleeve should be shorter than the delivery lead of the injection punch. Once the pressure chamber and sprue sleeve have been heated and treated, the inner holes must be finely ground and then axis ground. Ra0.2 m is the desired level of surface roughness. The diverter’s concave depth and cavity diameter are matched to the inner diameter of the sprue sleeve, with a 5° slope in the demoulding direction, and together they produce the coating. Using the coated guide sprue, the pressure chamber filling degree may be enhanced because the capacity of the effective length of the pressure chamber is reduced.
A mold runner’s specifications.
With an inner diameter more than two-thirds (63%) of the pressure chamber, the transverse runner of cold horizontal mold should be positioned to avoid metal liquid from entering the transverse runner prematurely and beginning to harden in advance. From the sprue to the inner gate, the runner’s cross-sectional area will be gradually decreased. An increase in the eddy current air wrapping and an expansion of the cross-sectional area can be achieved by negative pressure when molten metal flows over it. The output segment is typically 10% to 30% smaller than the intake section. Both the runner’s length and depth must be specified. To stabilize and guide the flow, it is necessary to keep the length at a given length. The molten metal’s temperature will drop rapidly if the depth is inadequate. Increasing the depth of the condenser will not only reduce production, but also increase the amount of material that is returned. Faster molten metal entry into mold is ensured by a transverse runner with a larger cross-sectional area than an inner gate. Main runner cross-sectional area should be larger than that of each branch runner. To avoid early cracks, the two sides of the runner’s bottom should be rounded. It is possible to adjust the angle of the two sides by around 5 degrees.
Runner surface roughness Ra0.4 m
When molten metal enters a mold, the separating surface must not be instantly closed, and the overflow and exhaust grooves must not contact the core in the front. As much as feasible, the molten metal should flow into the mold in a direction parallel to that of the cast ribs and fins, and fill the cavity in a clockwise manner. The molten metal flow should be as brief as feasible when determining the ingate position. In order to avoid flaws such as eddy current aeration and oxidation inclusions while utilizing multi-strand ingate, it is vital to keep the molten metal from converging and hitting after molding. Filling speed can be maintained by making the inner gate of thin-walled components smaller. The setting of the inner gate should be simple to cut, and the casting body should not be affected.
The sewage overflow container
In order to avoid damaging the casting, the overflow tank should be easy to remove from the casting. Be careful not to get an overflow port too far out of place while setting up an exhaust slot on the overflow port, since this will make the exhaust slot useless. Due to the risk of casting problems caused by the cold liquid, slag, gas and paint returning to the mold cavity, several overflow ports or an extremely broad and thick overflow port should not be used on a single tank.
Cast a fillet (including corner)
Undeclared fillet R2 is frequently specified in the casting design. Unnamed fillets play an important function while opening the mold, and we should not produce clean corners or too little fillets when we do so. Mold life may be extended by using a fillet to smooth out the flow of liquid metal, allowing gas to be released sequentially, reducing stress concentration, and increasing mold life. Improper filling makes it difficult for the casting to break or develop faults of any kind). For example, the conventional oil pan mold has a lot of neat edges. Currently, the Brother oil pan mold is the best, but there are also a number of heavy-duty oil pans on the market. Side concaveness in the demoulding direction is absolutely banned on the demoulding slope (it is often that the casting is stuck in the mold during mold test, and local concave is caused by drilling, hard chisel, etc. when incorrect methods are used for treatment).
Surface
The demoulding direction should be followed while polishing the roughness producing portion and pouring system. Only 0.01-0.2 seconds are required for the molten metal to enter the pouring system from the pressure chamber and fill the mold cavity. A high surface polish is important to lower the flow resistance of liquid metal and limit the loss of pressure. The gating system’s heating and eroding conditions are also unsatisfactory. Mold can be damaged more easily if the polish is poor.
The toughness of the aluminum alloy used to make the mold
When working with copper that has a hardness of hrc46 or above, it is best to leave the mold with some repair allowance in order to limit the maximum size and avoid welding. Parallelism between the mold separating surface and template plane is required for die-casting mold assembly. Guide post, guide sleeve, and formwork perpendicularity requirements. There is a 0.1-0.05mm difference in height between the moveable and fixed die insert planes on the separating surface. Parting surfaces are completely flush with the push plates and reset rods. As a rule of thumb, the push rod is recessed by 0.1 millimeters or as requested by the user. There should be no stagnation in any of the die’s moving sections, and no pins should be moved in series. Slide blocks must be positioned accurately, core distances must be maintained, and the sliding block-to-block match must be more than two-thirds of a millimeter. Roughness on the sprue is seamless and smooth. During mold closure, the insert’s separating surface has a local clearance of 0.05mm. Signs have been installed at the intake and outflow of the cooling water channel. Roughness rs=0.04, no small damage to the surface.