Squeeze casting is an energy-saving metal forming technique that combines the benefits of traditional casting processes, what is squeeze die casting and how does it work? Follow us to learn about the definition, basic process, advantages, and characteristics of squeeze die casting.
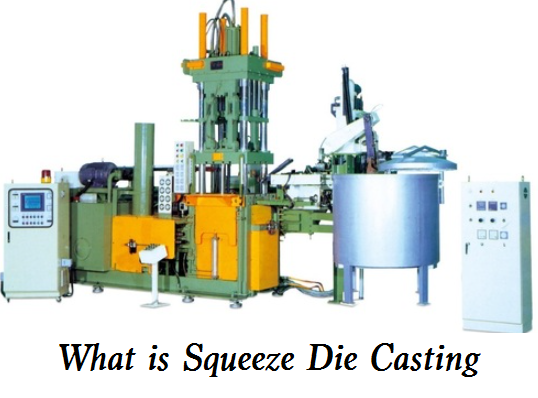
What is Squeeze Die Casting?
Squeeze die casting is a method to directly inject molten metal or semi-solid alloy into the open mold, then close the mold to produce filling flow and reach the external shape of the workpiece, and then apply high pressure to make the solidified metal (shell) produce plastic deformation. The non solidified metal bears isostatic pressure and solidifies under high pressure, and finally obtain the workpiece or blank.
Squeeze casting or liquid forging is a process in which molten aluminum is filled from bottom to top at low speed under pressure, and then solidified and fed in sequence under high pressure (> 100MPa).
– Low-speed filling: there is no air entrainment during mold filling, and there is no air hole defect inside the casting.
– High-pressure solidification: the cavity alloy obtains a fine, dense structure without defects such as porosity and shrinkage porosity. The resulting castings have high comprehensive properties, close to forgings, and are more cost-effective.
Advantages of Squeeze Die Casting
Squeeze casting technology is proposed to solve the main problems existing in the two technologies of ordinary die casting and traditional liquid forging.
Due to the simultaneous existence of high-pressure solidification and plastic deformation, the workpiece has no shrinkage cavity, shrinkage porosity and other defects, fine structure, and mechanical properties are higher than those of casting method, which is close to or equivalent to forging method. No riser feeding and final cleaning are required, so the utilization rate of liquid metal or alloy is high and the process is simplified. It is a new metal processing process with potential application prospects.
Process of Squeeze Die Casting
Raw material -> Smelting -> De-gas & De-slag – Squeeze casting -> Cutting -> Polishing -> X-Ray -> Heat treatment -> LPI -> Shot Blasting -> Package
Characteristics and Features of Squeeze Die Casting Process
Ordinary die casting filling, squeeze casting feeding. It solves the quality problems of airtightness (mainly shrinkage and porosity) commonly existing in traditional die-casting and vacuum die-casting technology by adding extrusion feeding steps after die-casting filling, and eliminating various shrinkage defects. Squeeze casting can also be said to be the technology of squeeze casting on the die casting machine. This extrusion die casting technology not only puts forward a process principle but also puts forward the equipment to realize the process. It is simple and practical, which fully expresses the technical and economic value of the extrusion die casting process.
Squeeze die casting is a combination of casting technology and hot die forging technology. This technology makes use of the characteristics of easy liquid flow and easy forming in metal casting, combined with the hot die forging technology to make the solidified closed metal hard shell plastic deformation under the action of pressure, and forcibly eliminate the shrinkage cavity and porosity formed by metal liquid shrinkage and solidification shrinkage, so as to obtain various liquid die forgings without any casting defects. Therefore, compared with castings, liquid die forgings have complete feeding and are easy to eliminate various defects; Compared with hot die forging, it is easy to form and requires less forming force, that is, the new technology of liquid die forging makes full use of the advantages of casting and hot die forging, and also makes up for the shortcomings of these two processes. The metal products produced by liquid die forging technology are not only light and durable, but also low price and strong market competitiveness.
For some specific products that are difficult to meet the performance requirements by casting process and difficult to form due to complex shape and forging process, it may be the best solution to use extrusion die casting process. The shrinkage porosity of the blank produced by this process and equipment is much higher than that of the traditional low-pressure casting process with sufficient feeding measures.