Today we are going to talk about another metal casting process – shell mold casting, what is it and how does it work? Here we have shell mold casting definitions, advantages, disadvantages, and the steps of the process.
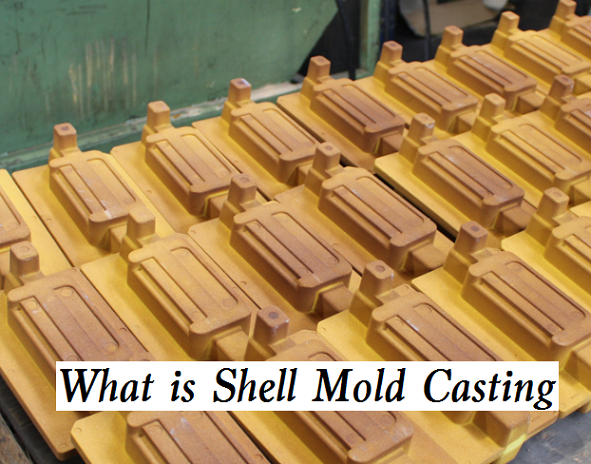
What is Shell Mold Casting - Definitions of Shell Mold Casting
Shell mold casting, also known as shell molding, is a type of metal casting process that is similar to sand casting. It can be defined as a casting method to cover the molding sand mixed with resin on the metal template with the mold and preheated, heat to melt the resin, form a thin shell, and take it off from the template after baking and hardening to be used as the casting mold, or a casting method of forming a thin shell mold with silica sand or zirconium sand and resin mixture or resin replica sand, forming a thin shell of a certain thickness on the 180 – 280 ℃ template, and then heating to solidify the thin shell, so as to reach the required temperature and stiffness.
Advantages of Shell Mold Casting
Using resin sand to make a thin shell mold or shell core can reduce the amount of molding sand used, the casting parts will get a clear profile and accurate size.
– The process can be done without machining or only a small amount
– Economical for large-batch orders
– High dimensional accuracy
– Thin-walled, complex parts can be manufactured
– Smooth surface of the shell mold cavity
– Easy flow of molten metal during the pouring
– Good surface finish of castings
– Reduced tearing and cracking of casting
– Lower labor requirements
Disadvantages of Shell Mold Casting
A drawback of shell molding is the resin-coated sand used in the process is relatively expensive, and the template must be precisely machined, which raises the total cost. In addition, it will also produce a pungent smell when pouring, which to some extent limits the wide application of this method.
What is the difference between shell mold casting and sand casting?
– Shell mold casting has higher dimensional accuracy, higher productivity, and lower requirements of labor.
– Shell molding uses resin-coated sand, which is more expensive than the mixture of raw sand, coal powder, and bentonite used in sand casting, and the resin-coated sand can’t be reused.
– The making of shell mold is more complex than sand mold and more costly.
– Shell mold casting requires specific equipment, while sand casting can be done manually as well.
Steps of Shell Mold Casting Process
1. The match-plate pattern that is composed of two pieces is created in the shape of the desired part.
2. Each pattern half is heated to 175 to 370 ℃ and coated with a lubricant to facilitate removal. The heated pattern is clamped to the dump box, which contains a mixture of sand and resin binder.
3. The dumped box is inverted to make the sand-resin mixture coat the pattern. The heated pattern partially cures the mixture, then forms a shell around the pattern. Each pattern half and the surrounding shell are cured to completion in the oven and then the shell is ejected from the pattern.
4. Two shells are joined together and securely clamped to form the complete shell mold. The shell mold is then placed in the flask and supported by the backing material.
5. Pour the molten metal, during this step, the mold is securely clamped together and molten metal fills the mold cavity. After the mold has been filled, the molten metal is allowed to cool and solidify into the shape of the final casting.
6. After molten metal has cooled, the mold can be broken and the casting removed. Trimming and cleaning processes are required to remove any excess material.