Pressure die casting is a metal casting process that is commonly used to produce complex products with close dimensional tolerances. In pressure die casting, molten metal is injected under high pressure into a steel mold cavity using a hydraulic piston or plunger. The molten metal is forced into the mold cavity and solidifies to take on the exact shape of the mold. This allows for intricate and precise geometries to be replicated. The ability to fill the mold cavity very quickly allows for rapid solidification and thinner walls compared to other casting methods. Pressure die casting is capable of producing parts with details as small as 2-3 millimeters thick. It is well suited for casting metals with lower melting points like zinc, aluminum, magnesium, and copper alloys. Some common applications of pressure die casting include automotive components, appliances, valves, hardware, and various structural parts that require precision dimensions and surfaces.
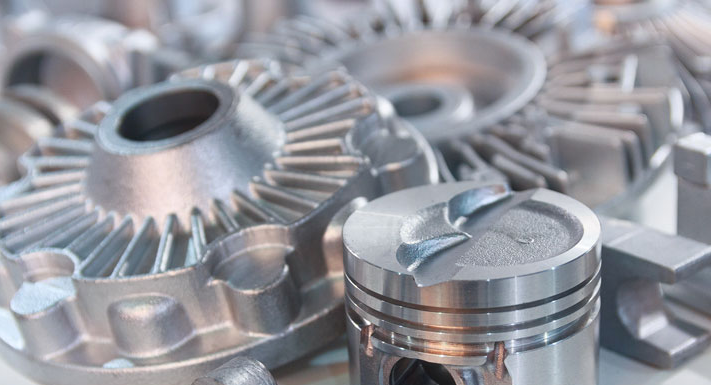
Materials Are Used in the Process of High-Pressure Die-casting
The main materials are aluminum and magnesium alloys for the cast parts, with tool/die steel used for the dies and lubricants applied to enhance the casting process.
- – Aluminum Alloys
Aluminum is the most commonly cast material due to its lightweight, corrosion resistance, and ability to take on complex shapes. Common aluminum alloys include Aluminum 380, 390, 356, 443, etc.
- – Magnesium Alloys
Magnesium alloys are also die-cast but to a lesser extent than aluminum due to higher cost. They provide an improved strength-to-weight ratio over aluminum.
- – Zinc Alloys
Zinc alloys are die-cast for parts that require good detail, strength, and corrosion resistance at a lower cost than aluminum or magnesium.
- – Tool Steel
Die steel (usually heat-treated H-13 tool steel) is used to fabricate the dies due to its high hardness, wear resistance, and ability to withstand the heat and pressures of molten metal injection.
- – Polymers
Some thermoplastics like nylon and PBT can also be die-cast but require lower temperatures and pressures than metal casting.
- – Lubricants
Lubricants like diesel oil or water-soluble oils are applied to the die cavities to aid ejection and reduce die wear during high-speed casting cycles.
Types of Pressure Die Casting
The key types are distinguished by the pressures used, hot/cold die temperatures, and mold materials like sand versus metal dies.
Type | Pressure Range | Die Temperature | Mold Material | Key Features |
High-Pressure Die Casting (HPDC) | Above 600 tons | Cold | Metal dies | Very fast cycles, fine details |
Low-Pressure Die Casting | 20-200 tons | Cold | Metal dies | Thicker sections, looser tolerances |
Cold Chamber Die Casting | High | Water-cooled dies | Metal dies | Minimal shrinkage, accurate parts |
Hot Chamber Die Casting | High | Heated dies | Metal dies | Continuous process, low tolerances |
Pressure Sand Casting | Gas pressure | N/A | Sand molds | Made using sand instead of metal dies |
Vacuum Die Casting | Partial vacuum | Cold | Metal dies | Eliminates porosity in aluminum |
Key Factors Affecting Mold Design in Pressure Die Casting
- – Part design: Simple vs complex geometries, wall thicknesses, draft angles, location of feed ports/vents.
- – Material: Thermal properties of the alloy being cast determine cooling requirements.
- – Tolerances: Required dimensional accuracy dictates detail/precision of the cavity.
- – Volume/quantity: Larger cavity size for high volumes but limits piece weight.
- – Flow balancing: Proper gate and riser placement/sizing for uniform filling of the part.
- – Cooling capacity: Sufficient cooling lines/channels in die to solidify metal before next shot.
- – Ejection requirements: Easy/reliable part removal dictates tie bars, slide rails, knockout mechanisms.
- – Surfaces finishes: Critical surfaces may need special treatments like polish plating.
- – Machining access: For secondary ops,cores/cavities designed to allow drill/mill access.
- – Die material/construction: Steel type for inserts, water lines, and ability to withstand cycles/pressure.
- – Maintenance access: Cavities designed considering die disassembly/repair needs over lifespan.
- – Automation interfaces: For robotic/CNC handling, locators for end effectors are required.
Applications of Pressure Die Casting
Essentially, any part that needs complex shapes in high volumes is a candidate for pressure die casting. It’s all about speed, precision, and net shape-forming capabilities.
- 1. Automotive components: Engine parts, transmission components, wheels, brake components, aluminum trim pieces.
- 2. Hardware: Door locks, hinges, hand tools, switches.
- 3. Appliances: Washing machine tubs, refrigerator parts, small kitchen appliances.
- 4. Electronics: Housings for power tools, cameras, cell phones, laptops, and TVs.
- 5. Bicycles: Frames, crank arms, brake levers, pedals.
- 6. Industrial machinery: Pump housings, hydraulic fittings, fasteners, valves.
- 7. Agriculture equipment: Implements, tractor parts, water pumps.
- 8. Aerospace: Bracketry, housing, ducting, small structural components.
- 9. Firearms: Gun frames, magazines, small moving parts.
- 10. Jewelry: Mass-produced pendants, charms, and rings.
- 11. Sports equipment: Golf club heads, baseball bats, ski/snowboard components.
- 12. Medical devices: Instrument housings, implants, surgical tools.