M390 is a super high alloy powder stainless steel, which is regarded as one of the best knife steels currently available. Many knife fans call it “God Steel”. Although the term “God Steel” is a big exaggeration, M390 is used as a high-quality kitchen knife and outdoor knife, and can also be used as a mold steel. It is indeed a “super steel” recognized by knife lovers and highly praised by cutting tool manufacturers, due to it has many advantages. So what makes the M390 so good for knife and cutting tools? Here, we will explain what M390 Steel is in detail by talking about its composition, properties, equivalent, price, applications, and differences with Magnacut steel!
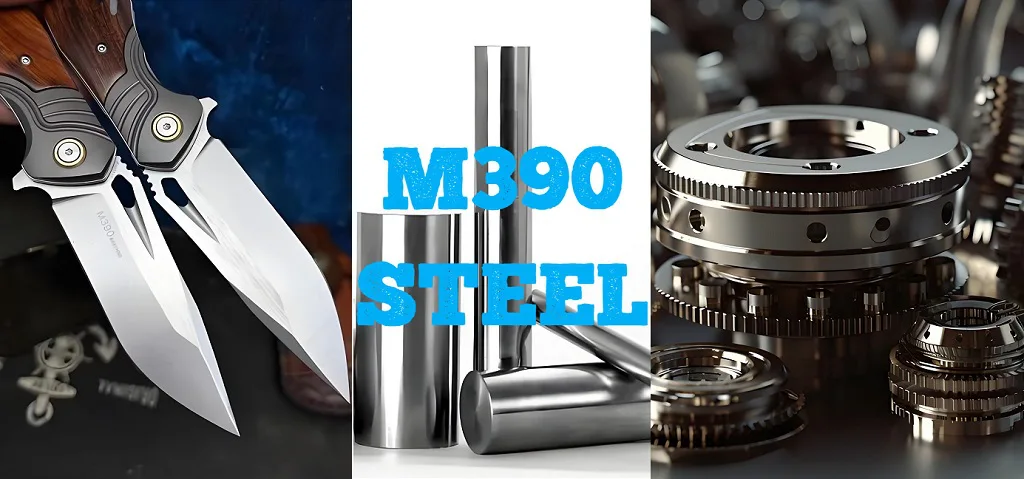
What is M390 Steel?
M390 steel is a high-alloy stainless steel that has earned a solid reputation in the knife and tool industry. Developed by Böhler-Uddeholm, a European company formed from the merger of Austria’s Böhler and Sweden’s Uddeholm, M390 combines excellent wear resistance, hardness, and corrosion resistance into one advanced material. It’s often referred to as a “super steel” due to its outstanding performance, especially in premium knives.
This steel is manufactured using third-generation powder metallurgy (PM), which results in a fine-grained, ultra-clean microstructure. Originally developed for industrial applications like injection molding, M390 later found its way into high-end knives, surgical tools, and precision instruments. Böhler also markets it under the name “Microclean”, highlighting its high purity and polishability.
With a basic understanding of M390’s background, let’s take a closer look at what it’s made of.
M390 Steel Chemical Composition
The secret to M390’s performance lies in its carefully balanced chemical composition. This blend of elements gives it the hardness, corrosion resistance, and wear resistance that users appreciate.
Element | Content (%) |
---|---|
Carbon (C) | 1.90 |
Chromium (Cr) | 20.00 |
Molybdenum (Mo) | 1.00 |
Vanadium (V) | 4.00 |
Tungsten (W) | 0.60 |
Silicon (Si) | 0.70 |
Manganese (Mn) | 0.30 |
Iron (Fe) | Balance |
Now that we’ve explored what’s inside M390 steel, let’s examine how these elements translate into real-world performance.
M390 Steel Properties
Thanks to its advanced composition and PM manufacturing method, M390 offers a well-rounded set of properties – well-balanced set of mechanical and physical properties, which make it a favorite among knife makers and users alike.
Hardness
After proper heat treatment, the steel reaches 60–62 HRC Rockwell hardness, which makes it able to hold onto a cutting edge for a long period. This high hardness is one reason M390 excels at edge retention.
Tensile Strength
M390 has high tensile strength, around 1900–2000 MPa (squeeze straight 275,000–290,000 psi), therefore it resists deformation under tension. Which is part of reason why the blades are able to cut heavily without bending or deformation.
Yield Strength
Its yield strength is also very high, with supporting strength supporting the steel’s ability in pressurized situations to hold up without permanent deformation.
Elongation
M390’s elongation value was quite low (~3–4%), which means while it is strong, it will break without a significant amount of stretching in the process. This characteristic is common in high-hardness tool steels.
Toughness
Though not the toughest steel available, M390 shows moderate toughness, normally ranking about 3.5 out of 10 in industry comparison tests. It takes everyday sort of use in stride but does not do well with extreme impacts or prying.
Edge Retention
M390 is well known for its excellent edge retention, usually rated 6.5 out of 10. With a fine microstructure and high vanadium content, it keeps sharp during prolonged cutting tasks. This outperforms several common stainless steels.
Wear Resistance
With its high hardness and alloying content, especially vanadium and molybdenum, M390 offers high wear resistance so that it can handle abrasive applications and prolonged cutting just as readily.
Corrosion Resistance
Thanks to its 20% chromium, M390 has excellent corrosion resistance, often rated 9 out of 10. It does well in humid, wet, or salty environments and can be useful for EDC, kitchen, and outdoor knives.
Modulus of Elasticity (Young’s Modulus)
M390’s Young’s Modulus is about 200 GPa. This reflects its stiffness and resistance to elastic deformation under stress, both typical of hardened tool steels.
Thermal Conductivity
M390 has low thermal conductivity, about 20–25 W/m·K, so it doesn’t lose heat quickly. This is an advantage in cutting tools because the edge does not get too hot easily during use.
Coefficient of Thermal Expansion
M390’s coefficient of thermal expansion is about 10.4 µm/m·K, within the ordinary range for stainless steels. It expands moderately with changes in temperature, an essential quality in applications needing with dimensional accuracy.
Heat Treatment
In order to get the optimum combination of properties, M390 goes through a complex heat treatment process that involves vacuum hardening and optional cryogenic treatment. Proper treatment is important, as suboptimal hardness can severely reduce performance.
Polishability
Thanks to its fine microstructure, M390 can be polished to a true mirror finish. This makes it popular with collectors and for high-end custom knives.
M390 Steel Pros & Cons
Like all materials, M390 has its strengths and weaknesses. Understanding both sides helps determine whether it’s the right choice for a specific purpose.
Pros:
- Outstanding corrosion resistance
- Excellent edge retention
- High hardness and wear resistance
- Fine grain for precise edges
- Great for mirror polishing
Cons:
- High production cost
- Not easy to sharpen with basic tools
- Lower toughness compared to some modern alternatives
- Complicated heat treatment process
While M390 performs exceptionally well in many areas, some users may ask how it compares to similar steels. That’s where the equivalent chart comes in.
M390 Steel Equivalent Chart
M390 is often compared to other high-end stainless steels that offer similar properties. Here’s how it stacks up:
Steel Name | Manufacturer | Notes |
---|---|---|
M390 | Böhler-Uddeholm | European-made powder steel |
CPM 20CV | Crucible Industries | Nearly identical in chemistry and performance |
CTS 204P | Carpenter | American-made equivalent |
These steels share almost identical compositions and are often used interchangeably in both knives and industrial tools.
With its strong performance across the board, M390 finds use in a wide range of applications. Let’s take a closer look at where this steel is most commonly used.
M390 Steel Applications
Thanks to its durability and corrosion resistance, M390 is used in a variety of demanding environments:
- Premium folding knives
- Outdoor and tactical blades
- Hunting and survival knives
- Surgical instruments
- Industrial tools such as molds and screws
Its combination of edge retention and resistance to the elements makes it especially valuable in situations where reliability and longevity are key.
Of course, performance comes at a price. So how much does M390 cost?
M390 Steel Price
M390 sits at the higher end of the steel market due to its complex production and performance level. Knives featuring this steel typically start around $150 and can easily reach several hundred dollars—especially for custom or handmade models.
However, as more manufacturers adopt M390, pricing has become more competitive, making it increasingly accessible to enthusiasts and professionals alike.
Speaking of alternatives, one steel has recently gained attention for challenging M390’s dominance: Magnacut. How do they compare?
Magnacut Steel vs M390 Steel
What is Magnacut Steel?
Designed especially for blades, Magnacut is a quite recent stainless steel invented by Dr. Larrin Thomas. Built from the ground up for cutting tools, Magnacut aims to balance wear resistance, hardness, and corrosion protection unlike M390, which started in the plastics sector.
M390 Steel vs Magnacut: What are the Differences?
M390 has several major differences from Magnacut. These include chemical content and performance, ease of heat treatment, pricing, and likely use cases.
Composition of Steel and Manufacturing Background
M390 was developed by Böhler in the late 1980s, with a high carbon (1.90%) and high chromium (20%) content added to vanadium, molybdenum, tungsten. Just like Magnacut, it is produced via powder metallurgy. This gives it a very fine grain structure with improved wear and corrosion resistance properties. Originally aimed at industrial uses, it was later adopted by the knife industry for its good stainless properties and hold on edge.
Magnacut, however, is a modern steel created specifically for knives. Dr. Larrin Thomas developed it to balance the demands of toughness, corrosion resistance, and wear resistance. These three qualities are difficult to achieve in a single steel. With its stainless nature and great toughness, Magnacut is one of the unique offerings of recent years.
Toughness
Toughness is the ability of a steel to resist chipping, cracking, bending, breaking, and so on under stress. This is an area where Magnacut is in a class of its own. Compared to M390. in this category it has a significantly better score. Therefore the steel is better for heavy-use tasks (such as chopping and slashing), and those situations where a blade may encounter shock loading and side stresses. M390. by comparison, is more susceptible to chipping. And thin edge geometries are especially liable to this.
Wear Resistance
Magnacut has less tolerance for wear than M390; this means it will have more difficulty keeping an edge during hard use. For this reason M390 is generally better suited to cutting jobs involving cardboard, rope, or rough materials. Magnacut may be a teeny bit lower in this category, but when it goes to higher hardness levels (62-65 HRC) after heat treatment, the difference is becoming less and less significant. Still not in its favor; M390 still wins out here simply because of phosphorus content alone.
Corrosion Resistance
Both steels stand out for their excellent corrosion resistance, but in this case Magnacut just noses in ahead. M390 already ranks high among stainless steels in this category, but Magnacut has been rated even higher, particularly at lower temperatures, so it is especially suitable for muggy places where the sea air might blow in.
Heat Treatment Flexibility
Heat treatment is a big factor in whatever steel does. M390 should normally be around 60-62 HRC if done right, but many knives factory made don’t achieve it due to mass production limitations. With Magnacut, though, manufacturers can spread widely in Rockwell hardness and not markedly sacrifice any property. With more knife makers getting Magnacut to these higher hardnesses out of the box, the result will be better performance.
Application Suitability
M390 is most commonly found in high-end folders and precision tools. Its high wear resistance and corrosion resistance make it a good general choice for EDC (Everyday Carry) knives where holding an edge is top priority. On the other hand, its low toughness limits its dependability in heavy-duty fixed blades.
Magnacut, because of its high toughness and stainless qualities, works well in both folding and fixed blades. It is particularly good for sojourns outside, survival situations or tactical use where you need to rely on the elements. Its ability to avoid both chipping and rust makes it especially versatile.
Price and Availability
For decades, M390 was such a premium steel that knives made from it would frequently cost over $150 and sometimes well up into the hundreds or even thousands at custom shops. Despite its wide use and popularity, it remains relatively expensive due to a powder metallurgy production process and the brand that it has established over time.
Newcomer Magnacut has given the market some more affordable choices. Knives using Magnacut now cost not all that much over $100 each, and this makes them accessible to a considerably broader selection of end users. Once it becomes widespread, expected even better heat treated blades at prices that are more reasonable for all parties concerned thanks to lower manufacturing costs. This affordability in conjunction with good all-round performance makes Magnacut a very attractive material indeed for both users and manufacturers.
Magnacut vs. M390 Steel: Which Is Better?
Priorities and usage determine M390 or Magnacut. M390 is known for its wear endurance and superior knife repute. This folding knife is good for edge holding and corrosion resistance. Because of its poor durability, it is not appropriate for hard-impact operations or rough-condition fixed blades.
Magnacut excels in numerous areas. Despite having lower wear resistance than M390. it has superior toughness and practically unmatched corrosion resistance. Heat treatment and knife type versatility are also better.
M390 has typically been pricey, appearing in $150-plus knives and high-end bespoke knives. As a younger brand, Magnacut is offering knives in the low hundreds at more reasonable pricing. As manufacturing increases, alternatives may get cheaper.
Magnacut outperforms M390 in toughness, wear resistance, and corrosion resistance. Add that more manufacturers are meeting heat treatment standards, and Magnacut becomes a more balanced and accessible option for more customers.
FAQs
Is M390 Steel Good Knife Steel?
Certainly. Premium knives often use it as it provides a good blend of edge holding, corrosion resistance, and toughness.
How Good is M390 Steel?
It works well in practical terms, especially with folding knives where long-term sharpness and rust resistance take front stage.
Is M390 a Super Steel?
M390’s qualities—high hardness, wear, and corrosion resistance—place it in the “super steel” category even if the phrase is marketing-driven.
How to Sharpen M390 Steel?
Standard whetstones may suffer with their hardness, hence use diamond or ceramic sharpening tools. Though it takes time, sharpening produces very great effects.
Is M390 Steel Stainless?
Absolutely. It is a stainless steel that resists rust really remarkably with 20% chromium.
What Steel is Better Than M390?
In particular, in:
S90V provides greater edge retention.
Magnacut gives improved corrosion resistance and durability.
S35VN is simpler to sharpen.
How Tough is M390 Steel?
Its intermediate hardness makes it appropriate for everyday usage blades but not for heavy impact or prying work.
Where is M390 Steel Made?
M390 is produced in Austria by Böhler-Uddeholm.