What is Low Pressure Die Casting - Advantages, Disadvantages & Process of LPDC | Diecasting-mould
Low pressure casting is the earliest anti-gravity casting technology, typically used to produce metal casting parts for the automotive industry. In this post, we’ll highlight what is low pressure die casting, the advantages and disadvantages of the LPDC process, as well as how it works.
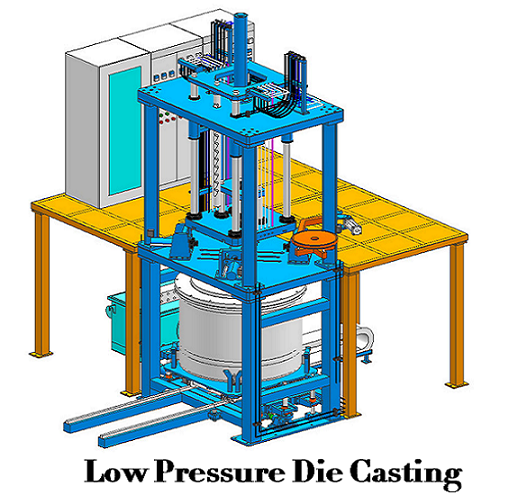
What is Low Pressure Die Casting & Low Pressure Die Casting Mold
Low pressure die casting (LPDC) is a casting method generally used to produce metal parts that are symmetrical in shape and design, for example, wheel rims and steering knuckles for automobiles may be cast using the LPDC casting process. Aluminum is the most commonly applied alloy in the low pressure die casting process, LPDC castings can also be made from other non-ferrous metals, such as zinc, brass, and magnesium alloys. LDPC is characterized as the low-pressure air is used to force molten metal from a holding furnace up into a mold cavity, LPDC is considered a permanent mold casting process since the molds that make the castings are permanent and can be reused for many cycles. Permanent molds are also referred to as dies, in contrast to permanent molds, destructible molds are broken up to retrieve the castings, these molds include bonded sand molds made from ceramics or similar materials. However, bonded sand molds may be used for some low-pressure die casting processes.
Advantages of Low Pressure Die Casting
– The filling of pure molten metal improves the purity of castings. The slag generally floats on the surface of the liquid metal, and the mold filling is realized by the liquid metal at the lower part of the crucible through the riser in low-pressure casting, which completely avoids the possibility of the slag entering the mold cavity.
– The filling of molten metal is stable, which reduces or avoids the tumbling, impact and splash of metal liquid during filling, reduces the formation of oxidation slag.
– LPDC casting has good formability. The filling of liquid metal under pressure can improve the fluidity of liquid metal, which is beneficial to the formation of castings with a clear outline and smooth surface, and is more favorable for the forming of large thin-wall castings.
– When the casting crystallizes and solidifies under pressure, it can get sufficient feeding and compact structure.
– The recovery rate of liquid metal is improved. Generally, a riser is not required, and the noncondensed metal in the riser can be refluxed to the crucible for reuse, which greatly improves the recovery rate of liquid metal.
– Convenient production and operation, good working conditions, high production efficiency, easy to realize mechanization and automation.
Disadvantages of Low Pressure Die Casting
– Large investment in equipment and molds
– In the production of aluminum alloy castings, the crucible and riser are in contact with the liquid metal for a long time, which is easy to be eroded and scrapped, and will also increase the iron content of the liquid metal and deteriorate the performance.
Applications of Low Pressure Die Casting
Low-pressure die casting is mainly used to produce aluminum alloy and magnesium alloy parts, such as automobile hub in the automobile industry, cylinder block, cylinder head, piston, missile shell, impeller, wind guide wheel and other castings with complex shape and high-quality requirements. Low-pressure casting can also be applied to small copper alloy castings, such as pipe fittings, faucets in bathrooms, etc. When low-pressure casting is used to produce cast steel, such as cast steel wheels and liquid riser, special refractory materials should be used.
How Does Low Pressure Die Casting Work? - LPDC Casting Process
LPDC foundries typically require several pieces of equipment for each step in the process, the melting furnace is required to melt the charged materials and bring the molten metal to the required temperature, the molten metal is then typically transferred to a holding furnace that is present within the LPDC machinery or located nearby the holding furnace maintains the molten metal at casting temperatures, once the holding furnace is secured in position, low-pressure air is used to force the molten metal into the mold cavity, the pressurized metal fills the die cavity which is then allowed to cool and solidify to form a casting. The casting is ejected after solidification and moved on for further processing, once the pressure is released, the molten metal in the feeding tube returns to the furnace and is ready for the next cycle for the best performance and consistency, almost all low pressure die casting machines are controlled by a programmable logic controller or PLC.