What is Lost Wax Casting & How It Works | Lost Wax Casting vs Die Casting
Die casting and lost wax casting are both precision casting methods, what’s the difference between them? Lost wax is an old metal casting process with a long history, and commonly used in modern industrial applications due to its unique advantages. Now, we’ll introduce what is lost wax casting and how does the process work, as well as lost wax vs die casting, which process should you choose.
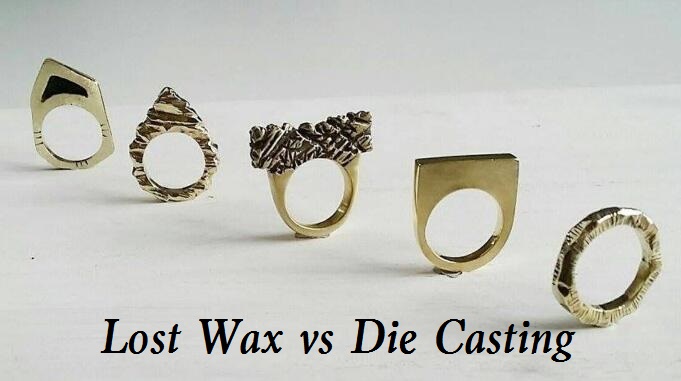
What is Lost Wax Casting?
Lost-wax casting, also called investment casting, is a type of metal casting method in which the molten metal is poured into a mold created by means of a wax model, a duplicate metal sculpture is often cast from an original sculpture. Lost-wax casting is one of the oldest known metal-forming techniques and widely used for intricate works, such as producing jewelry, dentistry, and art.
What Is the Process of Lost Wax Casting - How Does Lost Wax Casting Work?
Casts can be made from a wax model itself (direct) or from the copy of the original wax model (indirect). The lost wax process varies according to the industry and application, here are the basic stages of the indirect process.
1. Model making: create an original model from wax, clay, or other materials.
2. Mold making: a casting mold should be made from the original model or sculpture.
3. Wax patterns: once the mold is finished, pour the molten wax into it and swish around until even coating covers the inner surface of the mould.
4. Remove wax: remove the hollow wax copy of the original model from the model. Use a heated metal tool to rub out the marks that show the parting line or flashing where the pieces of the mould came together.
5. Spruing: spruing the wax copy with a treelike structure of wax, provide paths for the molten casting material to flow and for air to escape.
6. Ceramic shell: dip the sprued wax copy into a slurry of silica then into a sand-like stucco, make the shell consists of slurry and grit dry until a half-inch coating covers the entire piece.
7. Burnout: put the ceramic shell-coated piece in a kiln, whose heat hardens the silica coatings into a shell, and the wax melts and runs out.
8. Test: test the ceramic shell.
9. Pour: heat the mold to reduce its temperature difference with the molten metal. Metal is melted and then poured into the cavity.
10. Release: once the molten metal is cooled, quench the mold in water to dissolve the refractory plaster and release the rough casting.
11. Finishing: second processing of the casting parts, these casts may need to be machined, polished, ground, sandblasted, or gone through other finishing processes to achieve better surface finish or other requirements.
Difference Between Lost Wax Casting and Die Casting - Lost Wax vs Die Casting
Die casting and lost wax casting is completely different casting techniques, in die casting, the molten metal is poured into the steel mold on the die casting machine and extrude, the process is relatively simple and suitable for non-ferrous metal pieces with low melting points. Lost wax casting is to make a wax pattern and then make a shell on the wax pattern, melt the wax pattern, finally pour the molten metal into the empty shell after melting the wax pattern, and solidify it.
1. Cost
Die casting: Die casting machine and mold, mold-related components relative to other casting methods are expensive. Therefore, it is more economical to produce a large number of products when manufacturing die castings.
Lost wax casting: the investment of lost wax casting is small, and the whole process can be replaced by manual or automatic equipment. However, compared with die casting, even if a full set of automatic equipment is used, the cost of lost wax casting is 4-6 times lower than that of die casting.
2. Applications
Die casting: this process is only applicable to metals with high fluidity, and the casting quality must be between 30g and 10kg.
Lost wax casting: the lost wax precision casting process can not only achieve mass production, ensure the consistency of castings, but also avoid the stress concentration of residual knife marks after machining.
3. Advantages and disadvantages
Die casting: it is more economical when mass production is needed. In normal die casting, there are always pores in the last batch of castings. Therefore, no heat treatment or welding can be carried out, because the gas in the gap will expand under the effect of heat, resulting in internal micro defects and surface peeling. There are usually sand holes and rough edges in die castings, and the later processing capacity is relatively large. However, die casting produces parts that are durable and dimensionally stable, while maintaining close tolerances.
Lost wax casting: due to the high dimensional accuracy and surface finish of lost wax casting, the machining work can be reduced. Only a small amount of machining allowance can be left on the parts with high requirements, and even some castings can be used without mechanical processing. It can be seen that the investment casting method can save a lot of machine tools, processing time and metal raw materials.