Mineral material casting is a new type of composite energy-saving and environment-friendly casting with improved properties. In this article, let’s have a basic understanding of mineral castings.
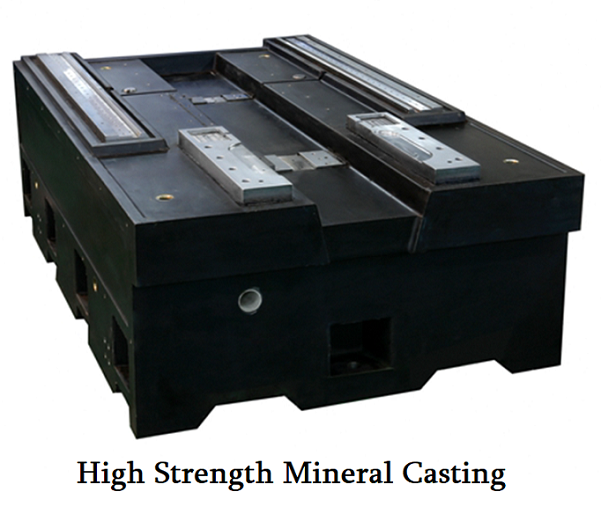
What is High Strength Mineral Casting?
High strength mineral casting materials, also known as mineral castings, are relative to ordinary strength mineral casting materials. This high-strength mineral casting mainly consists of quartz stone, rain flower stone, basalt, filler, high-performance epoxy resin adhesive and additives, and a certain proportion of ultra-fine and ultra short steel fibers. The process of mixing, mixing, pouring and tamping is also significantly different from that of ordinary mineral castings.
Advantages of Mineral Castings:
High strength mineral casting conforms to the material’s high compressive strength, bending strength, elastic modulus and other characteristics, as well as all the performance advantages of ordinary mineral castings in the following aspects:
– Excellent vibration absorption: Mineral casting has 6 to 10 times better vibration absorption performance than gray cast iron and steel.
– Low thermal conductivity and good thermal stability: the mineral casting materials reflect the change of external temperature very slowly, which improves the dimensional accuracy of the whole machine and ensures the processing accuracy of the parts to be processed.
– Good chemical and mechanical stability and can resist the corrosion of corrosive media, such as engine oil, corrosive solution, acid and common coolant.
– The casting process at room temperature does not require additional heating measures and consumes less energy.
– High casting precision, low internal stress and low internal shrinkage.
– It integrates various mechanical parts, such as anchor bolts, hydraulic pipes, coolant pipes and grounding wires, which can be integrated into the casting.
– The mineral casting materials can optimize the design and production, the cost of machining, assembly and logistics is reduced, which makes the cost before final assembly lower than that of welding structure or gray cast iron bed.
Manufacturing Process of Mineral Castings
Although the manufacturing process flow of mineral material castings for different purposes will be different, in general, the manufacturing process flow is roughly the same, which can be divided into: raw material proportioning, mixing, mold making, component assembly, casting, tamping castings, and forming.
1) Raw material proportioning mineral castings are made of sand, filler, resin adhesive, curing agent, retarder and other raw materials in a certain percentage. The ratio of raw materials often has a greater impact on mineral castings. In addition, the type, hardness, particle size, shape and moisture content of sand and gravel will have a greater impact on the strength of mineral castings. Therefore, only through continuous research and development, testing and optimization of raw material ratio can better mineral castings be produced.
2) The process of uniform distribution and full mixing of various sands, fillers, adhesives and additives through a mixer or a CNC continuous mixer. The mixing time shall not be too short, otherwise the mixing is insufficient; At the same time, it is required to stir evenly to make the sand and gravel filler fully wetted, otherwise the performance of the products after casting will be affected.
3) The mold fabrication and component assembly shall pre fabricate the corresponding special mold, and integrate the damping characteristics of mineral casting materials such as wire pipes, hydraulic pipes, forklift grooves, cooling water pipes, chip removal grooves, steel parts and cast iron materials in other links into the mold in advance, so as to facilitate the overall casting and molding of the castings.
4) Pouring: Pour the fully mixed raw materials into the pre prepared mold. Similar to ordinary cast iron casting, this process should be completed as quickly as possible. At the same time, it is necessary to reduce bubbles through mechanical vibration, so that raw materials can be quickly and tightly combined. Compared with the casting of cast iron, the casting is completed at room temperature, with low energy consumption, meeting the requirements of low-carbon, energy-saving and environmental protection.
5) Curing.