Galvanized steel is made by coating steel with a thin layer of zinc. The process involves immersing steel products or structures into a bath of molten zinc. As the steel is withdrawn from the bath, a thin coating of zinc metallurgically bonds to the surface of the steel. This zinc coating provides excellent corrosion protection because zinc is a sacrificial anode that corrodes preferentially over iron or steel. The zinc forms a barrier on the steel’s surface that blocks oxygen and water from reaching the underlying iron. This allows galvanized steel to withstand exposure to weather and humid, corrosive environments much better than uncoated steel. The zinc coating can increase the lifespan of steel structures and products significantly by preventing corrosion damage over long periods.
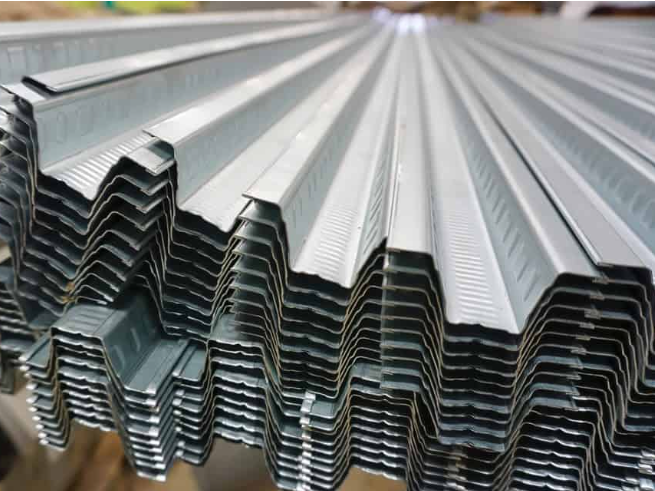
Differences between Galvanized Steel and Regular Steel
The key difference is the zinc coating that gives galvanized steel superb corrosion resistance compared to uncoated regular steel, at the cost of a higher price. Both have similar strength characteristics.
- – Coating
Galvanized steel has a thin coating of zinc bonded to the surface, while regular steel does not have any protective coating. The zinc coating is what provides galvanized steel its corrosion resistance.
- – Corrosion resistance
Thanks to the zinc coating, galvanized steel has much higher corrosion resistance than uncoated regular steel when exposed to weathering, moisture, saltwater, etc. Regular steel is more prone to rusting.
- – Lifespan
The zinc coating extends the functional lifespan of galvanized steel substantially compared to regular steel in corrosive outdoor environments. Regular steel may only last a few years before corroding.
- – Appearance
Right after galvanizing, the steel takes on a shiny silver/gray appearance from the zinc coating. Over time it may develop a dull patina. Regular steel eventually develops rust marks as it corrodes.
- – Strength
The zinc coating does not significantly affect the strength of the underlying steel. Galvanized and regular steel have similar strength properties.
- – Cost
Galvanized steel costs more than regular steel due to the galvanizing process involved. However, the increased lifespan often makes it more cost-effective in the long run.
How Does the Galvanizing Steel Process Work?
The galvanizing process starts with thoroughly cleaning and rinsing the steel surfaces to remove any dirt, oils, grease, rust, or other contaminants that could prevent proper bonding of the zinc coating. The steel may then be dipped in an acid solution to slightly etch the surface. Next, the cleaned steel pieces are gradually heated in a furnace up to temperatures between 840-848°F, at which point they are immersed in a bath of molten zinc inside a continuous galvanizing line. The zinc and steel then metallurgically bond as the steel reacts with the molten zinc. Once coated, the galvanized steel is lifted from the zinc bath where excess zinc drips off back into the reservoir. The pieces are then rapidly cooled in the air, causing the zinc to solidify and become tightly bonded to the steel surface. Finally, the galvanized steel undergoes visual inspection to ensure a uniform, well-adhered coating is achieved throughout the process.
Methods of Galvanizing Steel
There are a few main methods used for galvanizing steel. Hot-dip galvanizing is the most effective method, while electro-galvanizing is suitable for complex parts.
- –Hot-dip galvanizing: This is the most common and traditional method. It involves dipping steel parts into a bath of molten zinc at around 840°F. As the name suggests, it’s a hot process where the steel is heated before immersion. This results in a metallurgical bond between the zinc coating and the steel base.
- –Electrodeposition (electro galvanizing): An electric current is used to plate a thin, uniform zinc coating onto steel through electrolysis in a water solution. It allows for close-tolerance parts to be coated. The coating thickness is easily controlled.
- –Mechanical galvanizing: Zinc spray or powder is sprayed onto steel surfaces through mechanical means without melting the zinc. The coating isn’t as uniform or durable as hot-dip or electrodeposition methods. It’s used for repairing damage to existing galvanized coatings.
- –Zinc-rich paint: A zinc-rich epoxy or acrylic paint can be applied to steel as a non-metallurgical coating. It doesn’t provide the corrosion protection of hot-dip galvanizing but offers some barrier protection on parts not suited for heat galvanizing methods.
- –Galvannealing: Similar to hot-dip galvanizing but involves adding other elements like aluminum to the molten zinc. This forms a corrosion-resistant alloy coating on the steel after dipping.
Chemical Properties of Galvanized Steel
1. Chemical Composition:
– Base steel: 95-98% iron (Fe) and trace amounts of carbon, manganese, phosphorus, sulfur, and other elements.
– Zinc coating: 2-5% zinc (Zn) bonded to the surface.
2. Coating Properties:
– Coating thickness: 12-102 μm or 0.0005-0.004 inches for normal hot-dip galvanizing.
– Coating appearance: Smooth silvery gray color initially, develops a dull gray patina over time.
– Coating hardness: 350-400 Vickers hardness (HV). Zinc coating is slightly softer than base steel.
– Coating composition: Essentially pure zinc with some trace iron diffusion from the steel base. Less than 5% iron content.
Physical Properties of Galvanized Steel
- 1. Density: The density of galvanized steel is around 7.85 g/cm3. This is slightly higher than plain carbon steel due to the additional zinc coating.
- 2. Melting Point:
– The melting point of the base steel is 1500-1600°C, depending on the specific carbon content and alloy.
– The melting point of the zinc coating is around 420°C.
- 3. Hardness:
– The Vickers hardness of galvanized steel’s base metal matches comparable carbon steel, usually in the 140-350 HV range.
– The zinc coating itself has a lower hardness of around 350-400 HV.
- 4. Magnetism: Galvanized steel is magnetic like plain carbon steel since it has a ferrous base metal content of over 95%.
Advantages and Disadvantages of Galvanized Steels
Advantages of Galvanized Steel:
- – Excellent corrosion resistance: Zinc coating protects the base steel from rusting for many years.
- – Low maintenance: Once coated, galvanized steel requires no painting or other coatings to prevent corrosion damage.
- – Durable: The zinc layer withstands abrasion, scratching, and minor impacts without compromising its barrier properties.
- – Recyclable: Both the steel substrate and zinc coating can be recycled at the end of product life.
- – Cost-effective: Although more expensive initially than bare steel, galvanizing provides longevity that outweighs the higher upfront cost.
- – Aesthetic: The silver-gray color of galvanized steel has an attractive, polished appearance commonly used for railings, hardware, etc.
Disadvantages of Galvanized Steel:
- – Higher material cost: Galvanizing processing adds to the original cost of the steel.
- – Heat limitations: Cannot be welded or formed at temperatures over 300°C without risking zinc vaporization.
- – Embrittlement: Prolonged heating over time may cause the zinc layer to embrittle the underlying steel sheet.
- – Coating imperfections: Surface scratches or scruffs in galvanizing expose bare steel to corrosion.
- – Surface roughness: The galvanizing process causes the steel to become rougher textured compared to oiled/painted surfaces.
- – Toxic fumes: Hot galvanizing involves hazardous zinc fumes that need adequate ventilation and controls.
Uses of Galvanized Steel
Anywhere steel needs durable corrosion protection for outdoor use – especially in wet or coastal environments – galvanized steel is often the material of choice due to its superior resilience. Here are some common uses and applications of galvanized steel.
- – Construction
Beams, bolts, fasteners, joists, pipes, poles, scaffolding, rebar, wall panels, roofing, stairs, etc.
- – Agriculture
Grain silos, barns, fences, livestock equipment, agricultural structures.
- – Infrastructure
Guardrails, signs, traffic barriers, lamp posts, utility poles, transmission towers.
- – Industrial
Storage tanks, process equipment, ductwork, conveyors, and machine components.
- – Appliances
Washers, dryers, water heaters, refrigerators, freezers, microwave ovens.
- – Automotive
Truck beds, cargo areas, vehicle frames, outdoor trim pieces.
- – Shipping
Shipping containers, cargo vessels, ocean rigs, and port equipment.
- – Outdoor Furniture
Patio tables, chairs, umbrellas, playground equipment.
- – Hardware
Nails, screws, nuts/bolts, plumbing fixtures, HVAC elements.
- – Residential
Rain gutters, downspouts, siding, shed kits, windows, doors.
- – Marine
Docks, boats, buoys, anchors, locks, bridges, ship decks.
- – Transportation
Traffic signs, light poles, railroad ties, and handrails.