There are many types of casting techniques applied in the manufacturing fields, what is expendable mold casting and what are the advantages and disadvantages of using it?
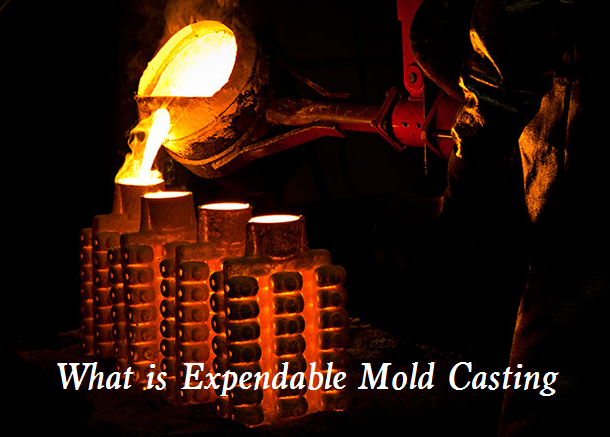
What is Expendable Mold Casting?
Expendable mold casting is a casting process in which a mold made of a non-reusable material is used to create a metal part. The mold is typically made of materials such as sand, plaster, or ceramic, which can be easily shaped and molded into the desired form. Expendable mold casting is a popular and cost-effective method for creating parts with complex geometries, as it allows for precise replication of the pattern. However, it is not suitable for high-volume production runs, as the molds are not reusable and must be remade for each part.
The process starts with the creation of a pattern of the desired part, which is then used to make the mold. The pattern is typically made of materials such as wax or plastic, which can be easily melted or dissolved away once the mold is complete. Once the mold is created, it is filled with molten metal, which is allowed to cool and solidify. The mold is then broken apart, and the part is removed.
Expendable Mold Casting Advantages, Disadvantages
Pros of Expendable Mold Casting
– Versatility: Expendable mold casting can be used to produce complex shapes and intricate designs that may not be possible with other casting methods.
– Cost-effectiveness: Since the molds used in this process are made of low-cost materials, it is an economical process for producing small to medium production runs.
– High-quality surface finish: The molds used in this process can produce parts with high-quality surface finishes, which often require little or no additional machining.
– Wide range of materials: Expendable mold casting can be used to produce parts from a wide range of materials, including aluminum, copper, magnesium, and various alloys.
Cons of Expendable Mold Casting
– Limited reusability: The molds used in expendable mold casting are typically made of non-reusable materials, which means that they must be remade for each production run, increasing the time and cost involved.
– Dimensional accuracy: While expendable mold casting can produce intricate shapes and designs, it may not be as precise in terms of dimensional accuracy as other casting methods.
– Limited scalability: Expendable mold casting is not well-suited for high-volume production runs, as it can be time-consuming to create and dispose of the molds.
– Environmental impact: The process can generate a significant amount of waste material, which can have an impact on the environment if not properly disposed of.
Types of Expendable Mold Casting
There are several types of expendable mold casting techniques, each with its own unique characteristics and advantages. Some of the most common types of expendable mold casting include:
1) Sand Casting: Sand casting is the most widely used form of expendable mold casting. It involves creating a mold made of compacted sand, into which molten metal is poured. The sand mold is then broken apart to reveal the finished part.
2) Plaster Casting: Plaster casting, also known as investment casting, involves creating a mold made of plaster or ceramic materials. The mold is created by pouring the plaster or ceramic mixture around a wax or plastic pattern. The wax or plastic is then melted or burned away, leaving behind the mold into which molten metal is poured.
3) Ceramic Mold Casting: Ceramic mold casting is similar to plaster casting, but uses ceramic materials instead of plaster. Ceramic molds can withstand higher temperatures than plaster molds, making them suitable for casting high-temperature metals.
4) Shell Mold Casting: Shell mold casting involves creating a mold made of a resin-bonded sand mixture, which is cured to form a hard shell. Molten metal is then poured into the shell, which is broken apart to reveal the finished part.
5) Vacuum Casting: Vacuum casting is a variation of sand casting that uses a vacuum to draw molten metal into the mold, rather than relying on gravity.