If you are a knife enthusiast or even just a housewife, you definitely want to own a MagnaCut steel knife, and if you are a mechanical manufacturing master, you also want to install one MagnaCut steel cutting tool on your lathe. Designed specifically for knives, born out of a passion for both steel and knive, MagnaCut steel Not only is it one of the best blade materials, but it is also leveraging its advantages in other industrial manufacturing fields, especially in industries that require high steel performance such as mold making, machinery manufacturing, aerospace, etc! So what makes MagnaCut Steel so great? We will provide answers by explaining the Chemical Composition, Hardness and Properties, Pros and Cons of this advanced tool material, and we will discuss Equivalent, Price, Applications, and its differences from S30V steel to help you better understand it!
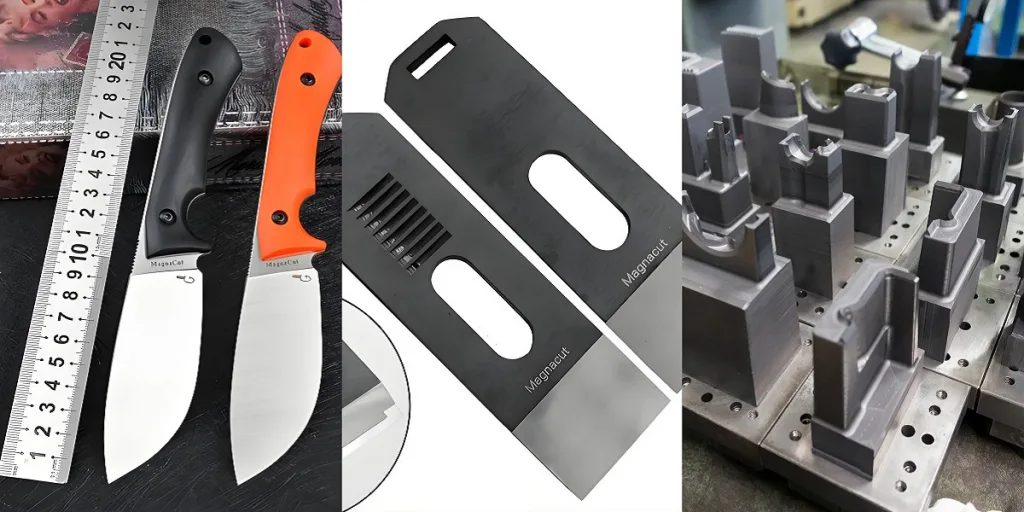
What is MagnaCut Steel?
MagnaCut Steel, meaning CMP MagnaCut Steel, is a powder stainless steel developed specifically for the knife industry by Dr. Larrin Thomas, a metallurgist with a PhD, well known in the blade community for his research and his blog, Knife Steel Nerds. Unlike many steels adapted from other industries, MagnaCut was designed from the ground up for knives.
Dr. Thomas grew up immersed in the world of steel, being the son of Devin Thomas, a respected maker of high-end stainless Damascus. Combining academic expertise with a lifelong passion for knives, he set out to create a steel that offered a strong balance of edge retention, toughness, and corrosion resistance, qualities that rarely coexist in one alloy.
You may have heard that CPM MagnaCut Steel is known as a leader in high-end blade steel. The cutting tools made from it are highly sought after and in short supply, seemingly becoming the new favorite of the cutting tool industry. So what makes the four top factory tool brands Mircrotech, Hogue, Fox ATCFGangster, Benchmade, and Dead Reckon Ridgeback, all choose to use MagnaCut steel? What makes MagnaCut Steel the preferred material for high-strength components such as molds? Keep reading, and we will give you the answer in detail!
MagnaCut Steel Chemical Composition
How is MagnaCut steel made? To answer this question, we first need to understand its chemical composition, which determines how it possesses unique properties that other steels do not have. Below is what the MagnaCut steel is made of:
- Carbon: ~1.2%
- Chromium: ~10.7%
- Vanadium: ~4.0%
- Molybdenum: ~2.0%
- Nitrogen: ~0.2%
- Niobium: ~2.0%
The made of MagnaCut Steel adopts an advanced and unique metallurgical model design, and after final heat treatment, the chromium content in the alloy mixture is relatively low. This has a unique function – it allows vanadium and niobium to form more carbides in the fine microstructure of the cutting edge, and increases the presence of chromium in the steel matrix, thereby providing anti fouling properties.
CPM MagnaCut Steel Properties
Why is MagnaCut steel so good? From the above Chemical Composition, it can be seen that as a high-quality powder metallurgy stainless steel, MagnaCut Steel balances its main performance characteristics by controlling the structure of the titanium compound, and then uses an appropriate amount of chromium to ensure high corrosion resistance while avoiding the formation of excessive chromium carbide and reducing toughness. Until now, it was impossible to combine hardness, toughness, and corrosion resistance in a single blade steel, but Lalin Thomas achieved a real breakthrough with MagnaCut steel with the following physical and mechanical properties:
MagnaCut Steel Rockwell Hardness (HRC)
The Rockwell Hardness (HRC) of MagnaCut steel can reach 59~65HRC after cryogenic treatment, which is very high for many carbon steels and stainless steels. However, in order to maintain toughness, most tool brands that use this steel will choose to reduce the hardness to 60-62HRC to achieve a balanced performance. Its hard alloy structure is very fine, with very small particles, which helps to provide excellent performance. Therefore, CPM MagnaCut can support high-performance, ultra-thin, polished cutting edges, and can withstand high pressure and harsh use even at lower hardness. Some knife enthusiasts have conducted actual tests on CPM MagnaCut. As an outdoor straight knife, its hardness after heat treatment is maintained at 62-63HRC, and the blade thickness is over 3.5MM. This steel can easily cut through 3MM nails and even No. 5 screws without damaging the blade, showing excellent performance.
MagnaCut Steel Heat Treatment
Due to its toughness, MagnaCut’s recommended heat treatment hardness reaches the highest level of tool steel. The hardness range is between 60-64 HRC. According to the Crucible steel data sheet, the optimal equilibrium heat treatment hardness for toughness balance is 62.5 HRC. For some Japanese kitchen knives that do not place much emphasis on blade toughness, Thomas stated that MagnaCut can be heat treated to 62-64 HRC.
MagnaCut Steel Corrosion Resistance
One of MagnaCut’s standout traits is its near-immunity to corrosion. It resists rust even in high-humidity environments or prolonged saltwater exposure, making it an excellent choice for outdoor, marine, or survival use.
MagnaCut Steel Edge Retention
MagnaCut provides solid edge retention. It performs slightly better than CPM 3V and S35VN in this area but doesn’t match the endurance of high wear-resistant steels like S90V or M390. It’s ideal for users who value a compromise between edge retention and ease of sharpening.
MagnaCut Steel Toughness
The toughness of this stainless steel is comparable to some of the most impressive tool steels, such as CruWear, CPM 3V, and CPM 4V. This stainless steel can withstand impacts that only niche steels such as 3V and 4V can withstand. Thomas said, “The new design eliminates chromium carbides, giving MagnaCut better edge toughness balance than previous PM stainless steels, and performance similar to the best non stainless steel PM steels. ”The combination of smaller and harder vanadium/niobium carbides with CPM process can improve strength while eliminating larger and more fragile chromium carbides. Thomas commented, ‘One of MagnaCut’s main innovations is that it aims to mimic the microstructure of the best non stainless steels such as Vanadis 4 Extra and CPM-4V.’. The chromium content decreases and the carbon content is balanced, so all chromium is “dissolved” in the solution, which has corrosion resistance and avoids the formation of chromium carbides. Other powder metallurgy stainless steels contain a large amount of chromium carbides, which can reduce toughness and corrosion resistance. On the contrary, MagnaCut only has small and high hardness vanadium and niobium carbides, achieving a better balance between toughness and wear resistance.
MagnaCut Steel Yield Strength
Although Crucible and Dr. Larrin Thomas have not specified the exact yield strength of MagnaCut, the combination of its high hardness and toughness indicates that MagnaCut Steel has a strong yield strength, making it highly suitable for demanding applications.
MagnaCut Steel Machinability
Compared to some high hardness steels, MagnaCut steel is easier to process and grind. This is an important advantage for tool manufacturers and knife makers, as it can reduce production costs and improve production efficiency.
MagnaCut Steel Sharpening
While not as easy to sharpen as simple carbon steels, MagnaCut isn’t particularly difficult to maintain. Its fine carbide structure helps make sharpening more approachable compared to harder, wear-resistant steels.
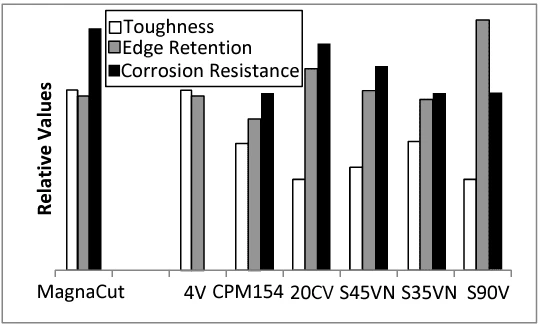
This comparison chart shows the difference in performance between CPM Magnacut steel and similar knife steels (Source: Crucible datasheet)
MagnaCut Steel Pros and Cons
Based on the above performance analysis and market application feedback, we summarized the benefits and disadvantages of Magnacut:
Pros:
- Excellent corrosion resistance, nearly on par with marine-grade steels.
- Good balance of toughness and edge retention for a stainless steel.
- Suitable for both fixed blades and EDC knives.
- Allows thin grinds due to high edge stability.
- Made in the USA via Crucible’s powder metallurgy process.
Cons:
- Not the toughest among stainless steels, outperformed by AEB-L and 14C28N.
- Edge retention is good but doesn’t compete with ultra-high-wear steels.
- Its performance depends heavily on heat treatment and blade geometry.
- May not be ideal for large chopping blades due to shock resistance limits.
CPM MagnaCut Steel Equivalent Chart
Because of the unique features of CPM MagnaCut steel that set it apart from its competitors, we are unable to find a perfect one-to-one equivalent for it, but it competes favorably with several popular steels:
Steel | Toughness | Corrosion Resistance | Edge Retention |
---|---|---|---|
S35VN | Moderate | Good | Moderate |
CPM 154 | Lower | Good | Moderate |
AEB-L | High | Good | Low-Moderate |
Nitro-V | High | Moderate | Moderate |
CPM 3V | Very High | Low | Moderate |
Magnacut | High | Excellent | Moderate-High |
CPM MagnaCut Steel Applications
Due to its excellent comprehensive performance, MagnaCut steel is not only widely used in the production of various types of cutting tools – suitable for all uses from heavy-duty blades to high-performance, fine edge cutting tools, but also has become an ideal material for manufacturing high-strength, high wear resistant components in the manufacturing industry. The following are its main applications at present:
- Daily knives: whether it’s nail clippers, gentleman’s folding knives, or survival knives. MagnaCut Steel can cover all application areas, whether it is a strapping machine, frame lock folding knife, or kitchen knife.
- Cutting tools: Due to the high strength and wear resistance of Magnacut powder steel, it is an ideal material for manufacturing cutting tools such as drill bits, milling cutters, planers, cutters, etc.
- Mold manufacturing: The high strength and corrosion resistance of Magnacut powder steel make it superior in the manufacture of various molds, such as injection molds, die-casting molds, etc.
- Aerospace: The high strength and lightweight properties of Magnacut powder steel make it widely used in the aerospace industry, such as turbine blades, wings, and other components.
- Magnacut steel, as a new type of alloy steel, will have a wider range of applications in the future with the continuous development of industry and technological progress, providing strong support for the development of various fields.
MagnaCut Steel Price & Cost-Efficient
Is MagnaCut Steel ecxpensive? In the market, the price of MagnaCut steel is usually around $100 per pound, and the specific price may fluctuate due to changes in suppliers and market demand Cutting tools made of MagnaCut material are usually considered high-end products. Its price reflects the complexity of production and the balance of performance provided by steel, typically ranging from $100 to $500.
However, MagnaCut steel is a cost-effective knife steel. It reduces storage and logistics costs, machines do not need to be converted to other tools, and heat treatment does not need to be adapted to other materials. MagnaCut enables knife manufacturers to reduce costs in many ways, even though the price per ton of MagnaCut steel should be slightly higher than M390 and S35V powder steels.
Magnacut Steel vs S30V, What are the Differences & Which is Better?
Above, we have discussed how Magnacum Steel, as the latest super steel, has become the new favorite of the cutting tool industry in a short period of time. So what are the improvements and shortcomings compared to the old powder metallurgy steel S30V Steel that has dominated the market for many years? Let’s take a close look at the differences between Magnacut Steel vs S30V Steel:
1. Composition and design concept
CPM S30V – Developed by Dick Barber in collaboration with tool manufacturer Chris Reeve, the main components include 1.45% carbon, 14% chromium, 4% vanadium, and 2% molybdenum-59. The core of its design is to enhance wear resistance and blade retention through uniformly distributed vanadium carbide particles, but high chromium content results in some chromium forming chromium carbide, sacrificing some corrosion resistance and toughness.
CPM MagnaCut – designed by metallurgist Dr. Larrin Thomas, with an adjusted composition of 1.15% carbon, 10.7% chromium, 0.2% nitrogen, and an increased proportion of vanadium and niobium. By reducing the chromium content and optimizing the carbide structure, MagnaCut avoids the formation of chromium carbide, allowing more chromium to remain in the steel matrix to improve corrosion resistance, while enhancing toughness and wear resistance through finer vanadium/niobium carbides.
2. Performance comparison
Resilience – MagnaCut has significantly better toughness than S30V, and even approaches or exceeds non stainless steels such as CPM 4V and CruWear. Experimental data shows that MagnaCut has twice the impact toughness of S30V and can withstand the impact force in high-intensity usage scenarios.
Blade retention – S30V is known for its high wear resistance, but MagnaCut’s blade retention is close to between S35VN and S45VN through a more uniform distribution of carbides, slightly inferior to S45VN but better than S30V.
Corrosion resistance – MagnaCut’s corrosion resistance far exceeds S30V, approaching “saltwater grade” stainless steels such as Vanax and LC200N, while S30V’s corrosion resistance is only comparable to 440C.
Hardness and heat treatment – MagnaCut can be heat treated to 62-64 HRC and maintain high corrosion resistance and toughness at 60-61 HRC; The hardness of S30V is usually controlled between 58-61 HRC, and brittleness significantly increases after exceeding 58 HRC.
3. Processing and polishing characteristics
S30V – Known for its difficulty in grinding, it requires the use of high cutting force grinding tools (such as diamond grinding stones), and the original sand belt machine has deep marks, resulting in low efficiency for ordinary grinding.
MagnaCut – Due to the finer and more evenly distributed carbides, grinding is relatively easy and can be efficiently achieved through conventional grinding stones, making it suitable for users to maintain on their own.
4. Application scenarios
S30V – High wear resistant cutting tools suitable for daily use (such as folding knives, tactical knives), especially perform well in scenarios where frequent cutting of hard objects is required.
MagnaCut – With its high toughness, corrosion resistance, and hardness balance, it has become the preferred choice for outdoor knives, diving knives, and kitchen knives, especially suitable for humid or saltwater environments.
5. Market positioning and cost
S30V – As an early representative of high-end steel, it had a higher cost, but due to its mature technology, it has now been widely adopted.
MagnaCut – as a new generation of “all rounder steel”, it quickly became the focus of the market after its launch in 2022. with orders scheduled until 2025. The price is higher, but its comprehensive performance makes it a new favorite of high-end brands such as Benchmark and Spyderco.
FAQs of CPM MagnaCut Steel
If you have persisted reading this far, you should now know enough about MagnaCut steel, but perhaps you still have some doubts, so we list the answers to the following frequently asked questions about this super steel:
What does CPM Stand For?
CPM stands for crucible particle metallurgy. This is the proprietary trademark name for a specific process, known as powder metallurgy (PM) steel. CPM makes steel very uniform. This is accomplished using complex and expensive manufacturing processes. This process allows for uniform distribution of carbides. The CPM steelmaking process makes steel stronger and reduces the likelihood of failure or change in the final product. This means that it is unlikely to fracture, break or break at weak points in the microstructure of the steel. Magnacum is perfect for humid, damp, or coastal environments where you also need excellent performance and resilience. In the past, tool users had to sacrifice performance when choosing highly rust resistant tools, but now with Magnacum tools, users can benefit from very high-quality cutting tools without sacrificing excellent rust resistance.
Does MagnaCut Steel Rust?
No! CPM MagnaCut is made of stainless steel and has many advantages, one of which is its amazing anti rust, anti fouling, and anti-corrosion performance. MagnaCut has extremely strong corrosion resistance, but its chromium content is relatively low at 10.7%. This is because the chromium content in the steel matrix is high, not in the form of carbides. This releases available chromium, forming a protective chromium oxide layer on the steel surface. All these characteristics mean that it is highly suitable for various uses, including outdoor activities, survival, humid and coastal environments.
When Did MagnaCut Steel Come Out?
Magnacut steel was developed by metallurgist Larrin Thomas in 2021. and he subsequently sought assistance from Crucible Industries for mass production. MagnaCut Steel was subsequently launched between 2021 and 2023. Since 2024. Kexiao 17. Spyderco Para2Salt, Fox ATCFGangster, Dead Reckon Ridgeback, Chris Reeve Knives, today’s leading factory tools are gradually adopting MagnaCut steel!
Is MagnaCut Steel Magnetic?
Yes, CPM MagnaCut steel has weak magnetism, which originates from the microstructure of its martensitic stainless steel. After heat treatment, it forms a crystal structure mainly composed of martensite. Martensite is essentially a ferromagnetic phase, so steel exhibits weak magnetism after quenching.