Casting is the process of melting metal into liquid meeting certain requirements and pouring it into the casting mold. After cooling, solidification, and cleaning, castings with a designed shape and size can be obtained. Counter gravity casting is an irreplaceable production method in the production of complex thin-walled cast components. What is counter gravity casting and what are the benefits?
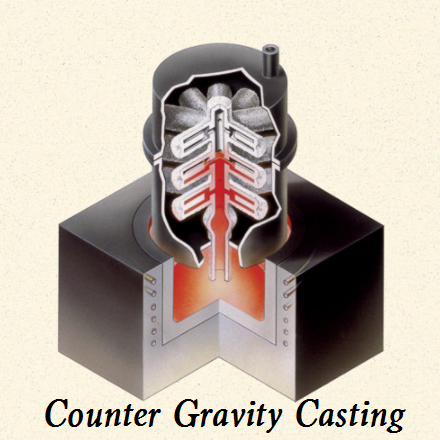
What is Counter Gravity Casting?
Counter gravity casting refers to the driving force of liquid metal filling mold that is opposite to gravity, and the metal liquid flows in the opposite direction of gravity. In counter-gravity casting, molten metal is actually filled under the combined action of gravity and external driving force. The external driving force is the dominant force in the filling process of the molten metal, which enables the molten metal to overcome its own gravity, resistance in the mold cavity, and other external forces to complete the filling mold. Due to the existence of an external driving force, counter-gravity casting has become a controllable process. During the filling process of molten metal, different filling speeds can be achieved by controlling the size of the external driving force to meet the requirements of different processes; At the same time, the casting can be solidified under a relatively strong effect to improve the feeding capacity of molten metal and reduce casting defects such as shrinkage cavity, air hole, and pinhole. Its characteristic is that the driving force of filling the mold with alloy liquid is opposite to the gravity direction. The alloy liquid flows in the opposite direction to gravity.
Advantages of Counter Gravity Casting
1) Controllable filling speed: counter gravity casting is generally used to produce non-ferrous alloy castings. The forming ability and internal quality of castings, especially the size and wall thickness, have strict requirements on the filling speed. The filling speed can be accurately controlled by a computer.
2) Good formability and smooth surface: during counter-gravity casting, the molten metal is filled and formed under pressure. With reasonable process parameters, the obtained casting contour is clear, especially for the production of thin-walled parts; During counter gravity casting, the pressurized gas fills the sand mold gap and forms a gas phase protective layer between the metal liquid and the sand mold to separate them, which can reduce the thermal and chemical effects of the metal liquid on the mold and reduce the surface roughness of the casting.
3) The casting has fine grains, dense structure, and high mechanical properties: the molten metal crystallizes and solidifies under pressure, and the primary dendrites will deform and break under pressure, and the cooling speed is fast, so the grains are small; At the same time, the pressure can improve the feeding ability and inhibit the gas precipitation in the molten metal, so that the porosity and microporosity are greatly reduced. Therefore, the mechanical properties of the castings have been significantly improved.
4) Pouring under a controllable atmosphere can be realized: during counter gravity casting, the atmosphere of the upper chamber, lower chamber or upper and lower chambers can be controlled. When using counter gravity casting to cast aluminum alloy castings, it is OK to use degreased and dry compressed air. However, for magnesium alloys, attention must be paid to the ambient atmosphere of molten metal and mold, because magnesium alloys will burn in the air. The use of a controllable atmosphere shall be determined according to the requirements of casting quality, the contour dimensions of castings, and other factors.
5) The utilization rate of metal is improved: during counter gravity casting, the solidification shrinkage of the casting can be continuously fed by the molten metal from the inner gate; In addition, the effect of pressure squeezing and plastic deformation has strengthened the feeding effect of the riser, and the riser size can be reduced accordingly or even not required.
6) The casting can be heat treated: compared with the die casting when using the counter gravity casting method to produce the casting, the mold filling speed is slow, the liquid level is stable, and the gas in the mold can be discharged smoothly. Therefore, there are few or no air holes in the casting, so the heat treatment can be carried out like the casting formed by gravity casting.
Types of Counter Gravity Casting
In counter gravity casting, it can be further divided into four different processes.
1) In low-pressure casting, when the mold is under normal pressure, the lower chamber enters the air to form a pressure difference. Under the effect of the pressure difference, the liquid raising, mold filling, and pressure maintaining processes are completed. The required equipment is simple, the operation is easy, and the filling process control is simple. In general, as long as the pressurization during pressure holding meets the requirements, the castings can also be well-fed. Compared with other counter gravity casting methods, low-pressure casting has a wider application range. Since the mold is under normal pressure, it is easy to open and close the mold and eject the casting when using the metal mold to cast. Therefore, metal mold low-pressure casting is widely used to produce castings with high-quality requirements, such as automobile wheel hubs, cylinder blocks, and other castings. In sand mold low-pressure casting, high-quality castings with large contours can be formed.
2) In vacuum casting, the lower chamber is in the normal pressure environment, and the upper chamber is vacuumed to form a pressure difference. Under the effect of the pressure difference, the liquid lifting, mold filling, and pressure-maintaining links are completed. Because the mold is in a vacuum environment, the filling ability of liquid metal is good, but the established filling pressure difference is limited, the solidification pressure is small, and the feeding ability is weak, which is suitable for forming small thin-walled castings.
3) In counter-pressure casting, not only can the mold filling and feeding be completed under pressure, but also because the mold is under pressure, the feeding of the riser can be better completed and the density of the casting can be improved. This casting method is suitable for producing large thick wall castings.
4) In adjusted pressure casting, the upper and lower chambers are vacuumized at the same time. When the specified vacuum degree is reached, the lower chamber enters the air to form a pressure difference. After the liquid lifting and mold filling are completed under the effect of the pressure difference, the upper and lower chambers enter the air at the same time according to the pressure difference when the mold filling is completed, so that the mold is under a positive pressure environment to enhance the feeding capacity of the casting. The advantages are that it not only gives full play to the filling ability of liquid metal, which is conducive to forming thin-walled castings but also can realize feeding under pressure to improve the density of castings. This casting method requires precise control of the pressure difference when pressurizing, and requires high control system.