Cooling of dies is necessary during the die casting process, today we are going to talk about the cooling system in mold, as well as the cooling rate and cooling time.
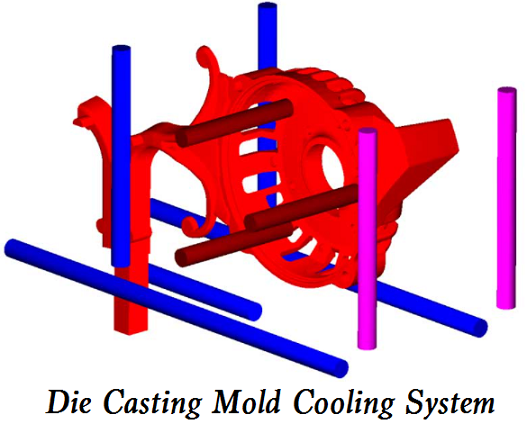
What is Cooling System in Die Casting Mold?
A cooling system in a die casting mold is a network of channels or passages designed to remove heat from the mold during the die casting process. The cooling system helps to control the temperature of the mold and the molten metal, which is important for producing high-quality parts and reducing cycle times.
The cooling system in a die casting mold typically consists of a series of channels or passages that are machined or drilled into the mold. These channels can be designed to follow the contours of the mold or to be placed in specific locations where heat buildup is most likely to occur.
During the die casting process, molten metal is injected into the mold under high pressure. As the metal enters the mold, it begins to solidify and cool. The cooling system channels allow a coolant, such as water or oil, to circulate through the mold to remove heat from the mold and the molten metal. The coolant absorbs heat from the mold and the molten metal, carrying it away from the mold and into a cooling unit or heat exchanger. The cooled coolant is then recirculated back into the mold to remove more heat.
The cooling system plays a critical role in the die casting process because it helps to maintain a consistent temperature throughout the mold, reducing the risk of warping, cracking, or other defects. It can also help to reduce cycle times by enabling faster cooling of the molten metal, which allows for the faster ejection of the finished part. Overall, the cooling system in a die casting mold is a critical component of the die casting process, helping to ensure consistent quality and productivity.
What are Cooling Rate and Cooling Time in Die Casting?
The cooling rate is the rate at which the metal cools and solidifies. The cooling time is the amount of time it takes for the metal to cool and solidify to a point where it can be safely ejected from the die.
In general, the cooling rate in die casting is very fast, typically measured in seconds. During the die casting process, molten metal is injected into a mold under high pressure. As the metal enters the mold, it begins to solidify and cool. The cooling rate is influenced by several factors, including the temperature of the mold, the flow rate and pressure of the metal, and the thermal conductivity of the mold and metal. For small and simple parts, the cooling rate in die casting can be very fast, often taking only a few seconds to complete. However, for larger and more complex parts, the cooling rate may be slower due to the greater amount of material that needs to be cooled.
Controlling the cooling rate is important in die casting because it can affect the quality of the finished part. If the cooling rate is too fast, the part may not fully fill out the mold, resulting in defects such as shrinkage or porosity. On the other hand, if the cooling rate is too slow, the part may become distorted or warped, resulting in dimensional inaccuracies.
What Affects the Cooling Rate?
The cooling rate in die casting depends on several factors, including the size and complexity of the part being cast, the type of metal being used, and the design of the mold.
– Temperature difference: The greater the temperature difference between the material and its surroundings, the faster the cooling rate will be.
– Thermal conductivity: The higher the thermal conductivity of the material, the faster it will conduct heat away and cool.
– Surface area: The larger the surface area of the material, the faster it will cool, as there is more area for heat to dissipate.
– Shape and size: The shape and size of the material can affect the cooling rate, as materials with more complex shapes or larger sizes may have more areas where heat is trapped, resulting in slower cooling.
– Type of material: Different materials have different thermal properties, which can affect the cooling rate. For example, metals generally have high thermal conductivity, which means they can cool faster than non-metallic materials like plastics.
– Surrounding environment: The surrounding environment can affect the cooling rate, as materials in cooler environments will generally cool faster than those in warmer environments.
– Heat transfer medium: The type of medium used to remove heat from the material can also affect the cooling rate. For example, materials cooled by water will generally cool faster than those cooled by air.