Centrifugal casting is a metal casting method that is different from pressure die casting in working. Now let’s get into the basics focus on what is centrifugal casting, types, advantages, disadvantages, and applications of the centrifugal casting process.
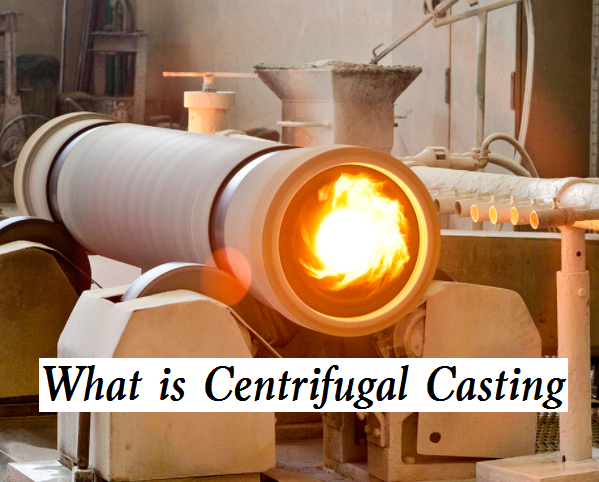
What is Centrifugal Casting?
Centrifugal casting is a process that involves putting liquid metal into a high-speed spinning mold in order to fill it and make the casting using centrifugal force. Centrifugal force causes the liquid metal to fill the mold completely in the radial direction and produce the casting’s free surface. The cylindrical inner hole may be formed without a core, which aids in the removal of gases and impurities from the liquid metal and influences the crystallization process of the metal, hence improving the mechanical and physical qualities of the casting parts. The rotating speed of centrifugal mold shall at least ensure that the liquid metal can form a cylindrical color and rotate around the axis immediately after entering the mold, make full use of the effect of centrifugal force to ensure the good internal quality of castings and avoid shrinkage cavities, porosity, inclusions and pores in castings.
Types of Centrifugal Casting Process
According to the spatial position of the mold rotation axis, common centrifugal casting can be divided into horizontal centrifugal casting and vertical centrifugal casting. The centrifugal casting in which the rotation axis of the mold is in the horizontal state or the included angle with the horizontal line is very small is called horizontal centrifugal casting, and the centrifugal casting in which the rotation axis of the mold is in the vertical state is called vertical centrifugal casting. Simply, the rotation axis of vertical centrifugal casting is parallel to the gravity direction, and the horizontal rotation axis is perpendicular to the gravity direction. Centrifugal casting with a large angle between the mold rotation axis and the horizontal and vertical lines is called inclined shaft centrifugal casting, but it is rarely used.
Pros and Cons of Centrifugal Casting
Centrifugal Casting Advantages
– There is almost no metal consumption of gating system and riser system to improve the process yield.
– The core can not be used in the production of hollow castings, so the metal filling capacity can be greatly improved, the ratio of casting wall thickness to length or diameter can be reduced, and the production process of sleeve and pipe castings can be simplified.
– The casting has high density, few defects such as pores and slag inclusion, and high mechanical properties.
– It is convenient to manufacture barrel and sleeve composite metal castings, such as copper sleeves, bimetallic rolls, etc. when forming castings, centrifugal movement can be used to improve the metal filling capacity, so thin-walled castings can be produced.
Centrifugal Casting Disadvantages
– It may have certain limitations when used in the production of dissimilar castings
– The inner hole diameter of the casting is inaccurate, the inner hole surface is rough, the quality is poor, and the machining allowance is large.
– Castings are prone to proportional segregation, so it is not suitable for castings with alloy prone to specific gravity segregation (such as lead bronze), especially for alloys with impurity specific gravity in liquid metal.
Applications of Centrifugal Casting
Centrifugal casting was first employed to manufacture cast pipes, but the method quickly expanded. At the moment, centrifugal casting technology is used to manufacture steel, iron, and non-ferrous carbon alloy castings in metallurgy, mining, transportation, drainage and irrigation equipment, aviation, national defense, and automotive sectors both at home and abroad. Among these, the most frequent are centrifugal cast iron pipe, cylinder liner, and shaft sleeve for internal combustion engines. Centrifugal force pouring may also be employed for the melt mold shell in some forming tools and gear castings, which improves not only the precision of the casting but also its mechanical qualities.
Below are some common applications and uses of centrifugal casting:
– Iron pipe: nearly 1/2 of the total output of nodular iron castings in the world every year is iron pipe produced by centrifugal casting
– Cylinder liners for diesel and gasoline engines
– Various types of steel sleeves and steel pipes
– Paper machine roller
– Bimetal cast iron roll
– Heating furnace bottom heat-resistant steel roller table
– Special steel seamless steel pipe
– Piston ring blank, copper alloy worm gear
– Specially shaped castings such as impellers, metal dentures, gold silver mesons, small valves, and cast aluminum motor rotors