Good corrosion resistance, excellent weldability, good cold workability, medium strength. The main alloy element of 5052 aluminum alloy is magnesium, which has good formability, corrosion resistance, weldability and medium strength. It is used to manufacture sheet metal parts, instruments, street lamp supports, rivets, hardware products, electrical appliances, etc. for aircraft fuel tanks, oil pipes, transport vehicles and ships.
5052 aluminum plate is AL Mg series alloy aluminum plate. Magnesium is the main alloy element of 5052 alloy aluminum plate. It is the most widely used anti rust aluminum material. This alloy has high strength, especially fatigue strength: plasticity and corrosion resistance. High performance, can not be strengthened by heat treatment, good plasticity in semi cold work hardening, low plasticity in cold work hardening, good corrosion resistance, good weldability, poor machinability, and can be polished.
Aluminum magnesium alloy also contains a small amount of manganese, chromium, beryllium, titanium, etc. Except for a small amount of solid solution, most of the manganese in the alloy forms MnAl6. The role of chromium in 5052 aluminum plate is similar to that of manganese, which improves the ability to resist stress corrosion cracking, increases the strength of base metal and weld, and reduces the tendency of welding cracks, but its content generally does not exceed 0.35%.
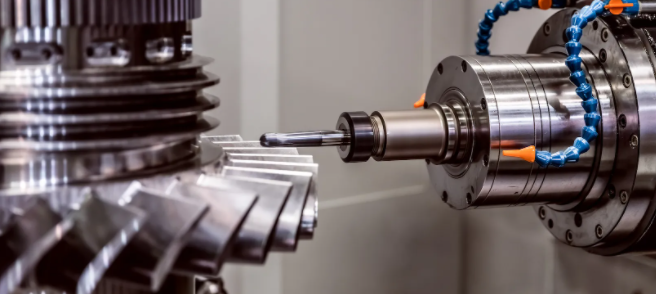
Chemical Composition Of Aluminum 5052
- Aluminum Al: allowance
- Silicon Si: ≤ 0.25
- Copper Cu: ≤ 0.10
- Magnesium: 2.2~2.8
- Zinc: ≤ 0.10
- Manganese Mn: ≤ 0.10
- Chromium Cr: 0.15 ~ 0.35
- Iron: ≤ 0.40
Process Properties of Aluminum 5052
- Molding performance – the alloy has good hot working plasticity. Forging and die forging temperature is 420~475 ℃, and hot deformation with deformation rate>80% is conducted within this temperature range The cold stamping property is related to the alloy state. The cold stamping performance of annealed (O) state is good, followed by H32 and H34 state, and H36/H38 state is poor.
- Welding performance – the alloy has good performance in gas welding, electric arc welding, resistance welding, spot welding and seam welding. Crystallization cracks are easy to occur during secondary argon arc welding. Soldering performance is acceptable, but soft soldering performance is poor. – The weld has high strength and plasticity, and the weld strength is 90% – 95% of the base metal strength. However, the air tightness of welds is not high. It is recommended to use 5A03 alloy as solder to improve its air tightness and eliminate the tendency of cracks.
- Machinability – The machinability of the alloy is not good in the annealing state, but it is improved in the cold work hardening state.
Surface Requirements of Aluminum 5052
The surface shall be free of cracks, corrosion spots and traces of nitrate. The surface is allowed to have peeling, bubble, surface roughness and local mechanical damage, and the depth shall not exceed 8% of the nominal wall thickness of the defect location, but the maximum depth of the defect shall not exceed 0.5mm, and the total area of the defect shall not exceed the total area of the plate. 5%。 The supplier is allowed to polish the profile longitudinally to a smooth surface.