Aluminum die casting is an essential process in manufacturing, known for its efficiency and versatility. Among the various aluminum alloys used, the A380 stands out as the most widely employed, thanks to its exceptional properties. With this overview of the most-used die casting material, we will take a closer look at the key characteristics of A380 aluminum, including its chemical composition, material properties, cost, common applications, and how it compares to other popular alloys like 6061. Join us as we uncover why A380 is the go-to choice for die casting applications worldwide.
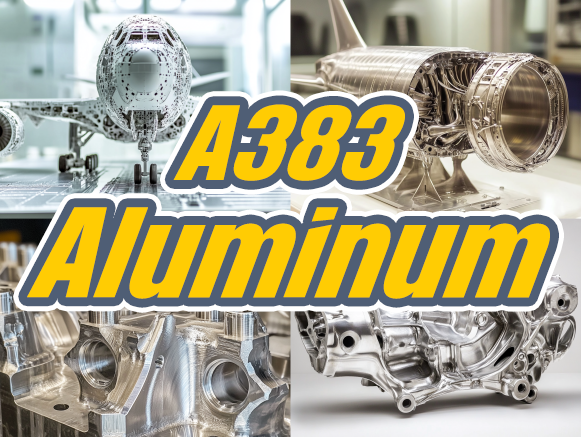
What is A380 Aluminum?
A380 Aluminumisa ASTM standard alloy for die casting, which is an Al-Si-Cu alloy. It contains a high amount of Si, which gives it excellent castability. It is also known as the ADC10 aluminum alloy in Japan and Asia based on the JIS standard. As one of the most popular aluminum die-casting alloy of the Al-Si-Cu series, the A380 has characteristics similar to A383, and excels in mechanical properties, machinability, and castability. In terms of mechanical properties such as yield strength and tensile strength, A380 is higher than A383 (ADC12), and the domestic production ratio of A380 is also higher compared to A383, which is overwhelmingly adopted in more than 50% of aluminum die castings.
A380 Aluminum Equivalents
International Equivalents of A380 Aluminum Alloy in different regions:
- Europe (EN): The closest equivalent in the European standard is EN AC-46000 (formerly known as EN AC-Al Si9Cu3(Fe)).
- Japan (JIS): The Japanese equivalent is ADC10, which also belongs to the Al-Si-Cu series.
- China (GB): In China, the equivalent material is YLDc12.
- Germany (GD): GD-AlSi9Cu3
- ISO: Under the International Organization for Standardization, it is similar to ISO Al-Si8Cu3Fe.
A380 Aluminum Chemical Compositions
Since A380 is an ASTM standard, it is operated under different standards worldwide. As similar alloys to A380, the equivalents in Japan are JIS ADC10, in Germany GD-AlSi9Cu3, and in ISO Al-Si8Cu3Fe. Below are the chemical compositions of each A380 Aluminum and its equivalents in different regions:
Alloy Name | Cu | Si | Mg | Zn | Fe | Mn | Cr | Ni | Sn | Pb | Ti | Al |
A380.0 (USA) | 3.0-4.0 | 7.5-9.5 | ≤0.10 | ≤3.0 | ≤2.0 | ≤0.50 | – | ≤0.50 | ≤0.35 | – | – | Balance |
ADC10 (Japan) | 2.0-4.0 | 7.5-9.5 | ≤0.3 | ≤1.0 | ≤1.3 | ≤0.5 | – | ≤0.5 | ≤0.2 | ≤0.2 | ≤0.30 | Balance |
GD-AlSi9Cu3(Germany) | 2.0-3.5 | 8.0-11.0 | 0.1-0.5 | ≤1.2 | ≤1.2 | 0.1-0.5 | – | ≤0.3 | ≤0.1 | ≤0.2 | ≤0.15 | Balance |
Al-Si8Cu3Fe(ISO) | 2.5-4.0 | 7.5-9.5 | ≤0.3 | ≤1.2 | ≤1.3 | ≤0.6 | – | ≤0.5 | ≤0.2 | ≤0.3 | ≤0.2 | Balance |
A380 Aluminum Density
The density of A380 aluminum, a widely used aluminum alloy for die casting, is approximately 2.71 g/cm³ or 2710 kg/m³. This specific gravity makes it suitable for various applications where lightweight and good mechanical properties are the key factor.
A380 Aluminum Material Properties
A380 aluminum alloy is a commonly used specialty aluminum alloy, due to its ease of casting, machinability, and good thermal conductivity. Its physical and mechanical properties are as follows:
A380 Mechanical Properties | Tensile Strength, Elongation, Yield Strength, Impact Strength, Shear Strength, Hardness
Mechanical Properties | A380 Aluminum |
Young’s Modulus (Elastic Modulus) | 71.0 GPa |
Tensile Strength | 320 MPa |
Yield Strength (0.2% Offset) | 160 MPa |
Elongation (at 50mm) | 3.5 % |
Impact Strength | 85 kJ/m2 |
Shear Strength | 190 MPa |
Fatigue Strength | 140 MPa |
Hardness | 51 HRB |
A380 Physical Properties | Specific Heat, Thermal Conductivity, Coefficient of Thermal Expansion, Solidification Temperature, Electrical Conductivity
Physical Properties | A380 Aluminum |
Specific Heat | 963J/(kg·K) |
Thermal Conductivity | 96 W/(m·K) |
Electrical Conductivity (based on copper) | 23% |
Coefficient of Thermal Expansion (from 293 to 473K) | 22 |
Solidification Temperature | 593 to 537℃ |
A380 Aluminum Pros & Cons
A380 aluminum alloy is a widely used specialty aluminum alloy with many notable advantages and some disadvantages.
Advantages:
- Easy to Cast: A380 aluminum alloy is easy to mold, making it suitable for die casting processes.
- Good Machinability: This alloy has very good surface processing effects in the cast state, with good hardness and mechanical strength, and can be used to produce automotive spare tire lifting gears and handles for electric tools.
- Good Thermal Conductivity: A380 aluminum alloy has excellent thermal conductivity, making it suitable for applications that require heat dissipation.
- Strong Corrosion Resistance: This aluminum alloy has strong corrosion resistance, suitable for applications in various environments.
- High Strength and Pressure Resistance: It has high strength and resistance to high temperature cracking, able to withstand significant stress.
- Widespread Applications: Due to its superior performance, A380 aluminum alloy is widely used in motor equipment chassis, engine mounts, gearboxes, furniture, generators, control arms, and many other products.
Disadvantages:
- Rough Surface: Although A380 aluminum alloy is easy to machine, its higher silicon content makes it somewhat rough.
- Aging Effect: If it is left to stand at room temperature after quenching before age hardening, it may adversely affect the strength.
- Casting Defects: During the die casting process, it is prone to defects such as shrinkage porosity, sand holes, gas porosity, and slag inclusion. These defects can affect the quality and performance of the final product.
- Cold Shuts Problem: Cold shuts are one of the main defects in die castings, usually located under the skin of the casting or embedded inside the casting, related to poor design of the casting system or too fast casting speed.
A380 Aluminum Alloy Applications
A380 aluminum alloy is known for its excellent combination of properties, making it a popular choice for die casting applications:
- Automotive Parts
Rocker arms, water passages, motor covers, cam holders, subarm chain tensioners, engine mount brackets, carburetors, cylinder blocks, chain covers, air compressor housings, clutch housings, converter housings, torque converter stators, wheel caps, adapter cases, cam brackets, power steering pumps, transmission cases
- Motorcycle Parts
Final flange driven, crankcases, cylinder bodies, head cylinders, housing shaft drives, brake shoe plates, housing chains, brackets, wheel hubs, lower cases, cylinder barrels, shock absorber cases
- Outboard Motors
Bottom couplings, casing lowers, casing uppers, extensions, block head covers
- Agricultural Machinery
Power take-off cases, differential gear cases, transfer cases, rocker covers, valve bodies
- AV Equipment & Electrical Appliances
VTR frames, VTR cameras, stereo turntables, DVD pick-ups, disk drive frames, optical heads, printer platen rollers, copiers, cable joints, drum flanges, gas appliance cocks
A380 Aluminum Alloy Cost (Price)
The A380 aluminum alloy is commonly used in die casting due to its balance of cost and performance. Here are a few points regarding its cost-effectiveness compared to other materials:
- Material Properties: A380 offers good corrosion resistance, high thermal and electrical conductivity, and excellent strength-to-weight ratio. These properties make it a popular choice for a wide range of applications.
- Cost: A380 is generally more cost-effective than other aluminum alloys for die casting, due to its lower silicon content and good castability, which reduces production costs.
- Machinability: It has good machinability, which can lower post-processing costs compared to other materials that might require more extensive machining.
- Recycling: Aluminum is highly recyclable, which can further reduce material costs and environmental impact.
- Comparison to Other Materials: While zinc can offer better precision and thin-wall capabilities, it is generally heavier and might be more expensive, especially for larger parts. Magnesium Alloys are lighter than aluminum but can be more expensive and have more complex processing requirements. Other Aluminum Alloys may offer better specific properties (like higher strength or better thermal resistance) but often at a higher cost.
Typical A380 AluminumPrice Range:
As a rough estimate, A380 aluminum alloy can range in price from around $1 to $3 per pound, depending on the factors mentioned earlier. However, this is a general range and can vary significantly in real-time market conditions.
A380 Aluminum vs 6061: What are Differences?
The main differences between A380 aluminum alloy and 6061 aluminum alloy are reflected in the following aspects:
- Alloy Composition and Characteristics:
A380 aluminum alloy is a specialty aluminum alloy known for its ease of casting, machinability, and good heat conductivity. It contains a higher silicon content, which makes its surface somewhat rough.
The primary alloying elements of 6061 aluminum alloy are magnesium and silicon, belonging to the Al-Mg-Si series alloy. It has medium strength, good corrosion resistance, and weldability.
- Mechanical Properties:
Due to its higher silicon content, A380 aluminum alloy performs better in terms of pressure resistance and resistance to high temperature cracking.
The mechanical properties of 6061 aluminum alloy can vary significantly depending on the tempering process it undergoes. The most commonly used state is 6061-T6, which indicates that the alloy has undergone solution heat treatment and artificial aging, providing good strength and machinability.
- Application Areas:
A380 aluminum alloy is commonly used in applications that require easy casting and machinability due to these characteristics.
6061 aluminum alloy, with its good strength, corrosion resistance, and weldability, is widely used in industries such as construction, aerospace, and transportation.
- Physical and Chemical Properties:
A380 aluminum alloy has good heat resistance and high mechanical and mechanical properties.
6061 aluminum alloy is known for its excellent machinability, welding characteristics, electroplating properties, and good corrosion resistance.
A380 aluminum alloy and 6061 aluminum alloy have significant differences in alloy composition, mechanical properties, application areas, and physical and chemical properties. The choice of which material to use should be based on specific application requirements.
In this article, we have introduced the features of A380 aluminum die casting. Based on our track record of delivering aluminum die cast products to domestic and international automobile parts and home equipment manufacturers, we offer various proposals such as optimal material selection and conversion to die casting methods. We can also handle die casting of zinc and magnesium, not just aluminum. If you have any issues with die casting, please feel free to consult with us. Thank you for reading until the end!