Patterns are replicas of the casting products with exact standards. What is a pattern in metal casting and how to make it? Today we’ll also go over the types of casting patterns.
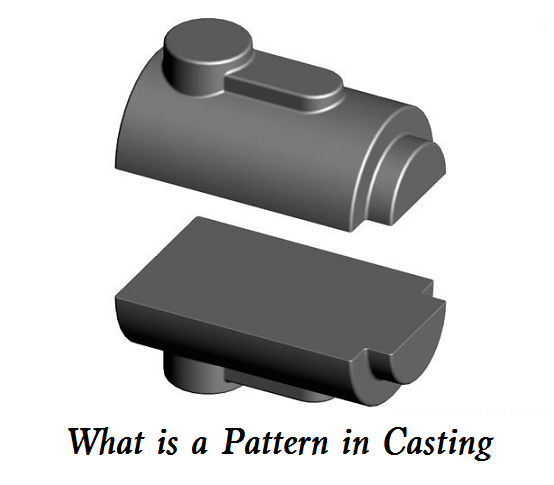
What is a Pattern in Casting?
In casting, a pattern is a replica of the final product that is used to create a mold. The pattern is typically made of wood, metal, plastic, or other materials, and is used to create a negative impression in the mold material, which is then used to cast the final product. The pattern determines the shape and dimensions of the final product. The quality of the pattern directly affects the quality of the final product, so it is important to ensure that the pattern is accurate and free from defects.
The pattern is typically made to the exact size, shape, and configuration of the final product, and is used to create a mold cavity that will produce the desired shape and dimensions of the final product. The pattern may be created manually by skilled craftsmen, or it may be created using computer-aided design (CAD) software and 3D printing technology. Once the pattern is created, it is used to make a mold by packing sand or other mold material around it. The pattern is then removed from the mold, leaving a negative impression on the mold material. Molten metal is then poured into the mold to create the final product. The mold material is then broken away from the final product, leaving a finished casting.
Types of Patterns in Metal Casting and Their Uses
There are several types of patterns used in metal casting, each with its own specific purpose and use. Here are some common types of patterns and their uses:
– Single-piece pattern: a simple pattern that is used to create a single cavity mold. It is typically made from wood, plastic, or metal and is designed to be used for low to medium production volumes.
– Split pattern: a pattern that is divided into two or more pieces that can be separated to create a multiple cavity mold. It is often used for high-volume production of small to medium-sized parts.
– Match plate pattern: a two-piece pattern that is mounted on a plate. The plate is used to create a two-part mold that can be separated to remove the casting. It is commonly used for high-volume production of small to medium-sized parts.
– Gated pattern: a pattern that includes a gate, runner, and sprue system. The gate, runner, and sprue system are used to direct molten metal into the mold cavity. It is often used for larger castings and complex shapes.
– Skeleton pattern: a pattern that is made from metal or plastic and is used to create complex shapes. It consists of a series of interconnected rods and is used to create intricate internal cavities.
– Sweep pattern: a pattern that is used to create a curved surface on a casting. It is typically made from wood and is used for low to medium production volumes.
– Matchplate Flask: a reusable mold-making flask that typically uses a match plate pattern. The flask consists of two halves that can be separated to remove the casting. It is commonly used for high-volume production of small to medium-sized parts.
– Cope and Drag pattern: a pattern that is used to create a two-part mold. The cope is the top half of the mold, while the drag is the bottom half. The pattern is typically made from wood and is used for low to medium production volumes.
How to Make a Casting Pattern?
The making of patterns is called patternmaking, which is an important step in the metal casting process, and it requires careful attention to detail to ensure that the pattern accurately reflects the final product. Here are the general steps.
1) Determine the pattern material: The first step is to determine the best material to use for the pattern. Common materials include wood, plastic, and metal. The material should be durable and easy to work with.
2) Create a drawing or model: The next step is to create a drawing or model of the final product, either manually or using computer-aided design (CAD) software. This will serve as the basis for the pattern.
3) Design the pattern: Using the drawing or model, design the pattern by adding material for shrinkage and machining allowances, as well as features such as draft angles and fillets. The pattern should be designed to ensure that it can be easily removed from the mold.
4) Create the pattern: Using the design, create the pattern using the chosen material. This may involve cutting, shaping, or machining the material to create the desired shape and dimensions.
5) Finish the pattern: Once the pattern is created, it may need to be sanded or finished to ensure that it is smooth and free from defects.
6) Test the pattern: Before using the pattern to create a mold, it is important to test it to ensure that it accurately reflects the final product. This may involve creating a test casting or using 3D scanning technology to compare the pattern to the original model.
7) Store the pattern: Once the pattern has been tested and approved, it should be stored in a safe and secure location for future use.