7075 is the lightest and strongest aluminum material, and its price is also super expensive! The strength of 7075 is no less than that of steel. 7075 aluminum plate belongs to the AL-An-Mg Cu series superhard alloy. 7075 aluminum plate is a product launched by Alcoa in 1943. In the aerospace industry, 7075 aluminum plate has been the main product of the 7xxx series alloy. Adding chromium alloy to the high-strength alloy of the AL-Zn-Mg Cu series makes it a good plate product with resistance to stress corrosion cracking. Because 7075 aluminum plate is the best product among aluminum alloy products, it generally has good mechanical properties and anodic reaction. So, 7075 aluminum plate is a good performance route for balancing aerospace applications. In our 7075 aluminum guide, we’ll talk about its advantages, uses, and differences between 6061 or steel.
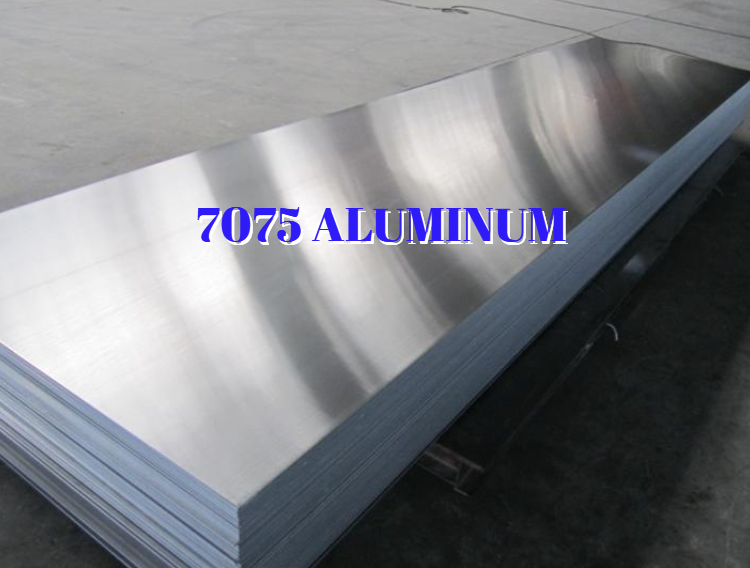
7075 Aluminum Properties
- High strength heat-treatable alloy
- Good mechanical performance
- Good usability
- Easy to process, good wear resistance
- Good corrosion resistance and oxidation resistance
Applications of 7075 Aluminum
Al pure aluminum
Features: Contains over 99.00% aluminum, has good conductivity, corrosion resistance, good welding performance, low strength, and cannot be strengthened by heat treatment.
Application scope: High purity aluminum (with an aluminum content of over 99.9%) is mainly used in lighting fixtures, reflective panels, decorations, chemical industry containers, heat sinks, solder joints, conductive materials, and special purposes.
Typical grade: 1050 (aluminum content above 99.5%) is used for extruded coils in the food, chemical, and brewing industries. 1060 (aluminum content above 99.6%) is used in situations where high corrosion resistance and formability are required, but low strength is not required.
Al Cu aluminum copper alloy
Features: Aluminum containing alloy with copper as the main alloying element. Manganese, magnesium, lead, and bismuth are also added for cutting properties. The disadvantage is that intergranular corrosion tends to be severe.
Application scope: Aviation industry (2014 alloy), screws (2011 alloy), and industries with higher operating temperatures (2017 alloy).
Typical grade: 2011 alloy, aluminum plate fast cutting alloy, with good cutting performance and high strength, but poor corrosion resistance. 2014 alloy is used in the aerospace industry with high strength. The strength of 2017 alloy is slightly lower than that of 2014 alloy, but it is relatively easy to process. 2618 aluminum plate forging alloy. Superior high-temperature strength but poor corrosion resistance. Pistons, rubber forming molds, and general heat-resistant components. 2219 aluminum plate has high strength, good low-temperature and high-temperature characteristics, and superior solubility, but poor corrosion resistance. Low temperature containers and aerospace machinery.
Al Mn aluminum manganese alloy
Features: Aluminum alloy with manganese as the main alloying element, which cannot be strengthened by heat treatment, has good corrosion resistance, and can also be called rust proof aluminum. It has good welding performance and good plasticity. The disadvantage is low strength, but it can be strengthened by cold work hardening. During annealing, it is easy to produce coarse grains.
Application scope: Seamless oil guide tubes (3003 alloy) and cans (3004 alloy) used on aircraft.
Al Si aluminum silicon alloy
Features: Mainly made of silicon, not commonly used. Some 4-series alloys can be heat treated for strengthening, but there are also some 4-series alloys that cannot be heat treated.
Typical grade: 4032 has good heat resistance, friction resistance, and low coefficient of thermal expansion. Pistons, cylinder heads. 4043 has less solidification shrinkage and is treated with sulfuric acid anodizing, resulting in a natural gray color. Fusion wiring, building panels.
Al Mg aluminum magnesium alloy
Features: Mainly composed of magnesium. Good durability, good welding performance, good fatigue strength, cannot be strengthened by heat treatment, can only be improved by cold processing to enhance strength.
Application scope: handle of lawn mower, aircraft fuel tank duct, bulletproof vest.
Typical grade: The strength of 5005 aluminum plate is the same as that of 3003 aluminum plate, and it has good processability, solubility, and corrosion resistance. The modification and processing after anodizing are good, and it matches the color of 6063 shaped material. Usage: Interior and exterior decoration for construction, interior decoration for vehicles, and interior decoration for ships. 5052 aluminum plate is the most representative alloy of medium strength, with good corrosion resistance, solubility, and formability, especially high fatigue strength and good seawater resistance. Usage: General sheet metal, ships, vehicles, construction, bottle caps, honeycomb panels. 5652 aluminum plate restricts impure elements in 5052 aluminum plate and inhibits the separation of hydrogen peroxide. Other characteristics are the same as 5052 hydrogen peroxide container.
Al Mg Si aluminum magnesium silicon alloy
Features: Mainly composed of magnesium and silicon. Mg2Si is the main strengthening phase and is currently the most widely used alloy. Medium strength, good corrosion resistance, good welding performance, good process performance (easy to extrude), and good oxidation coloring performance.
Application scope: Currently the most widely used alloy for energy tools, such as car luggage racks, doors, windows, car bodies, heat sinks, and compartment shells.
Typical grades: 6063 and 6061 are the most commonly used. 6061 is mainly used for aircraft parts, camera parts, ship parts, valve parts, various hardware and electronic accessories, etc. 6063, 6060, and 6463 have relatively low strength in the 6 series. 6262, 6005, 6082, and 6061 have relatively high strength in the 6 series.
Al Mg Zn Cu aluminum magnesium zinc copper alloy
Features: Mainly zinc, with a small amount of magnesium and copper added. It belongs to the aviation series and is an aluminum magnesium zinc copper alloy that can be heat treated. It is a superhard aluminum alloy with good wear resistance and good weldability, but poor corrosion resistance. The hardness of superhard aluminum alloy is close to that of steel. The extrusion speed is slower than that of 6 series alloys, and the welding performance is good.
Application scope: aviation (load-bearing components and landing gear of aircraft), rockets, propellers, and aerospace spacecraft.
Typical grade: 7050 is used for medium thick plates, extruded parts, free forgings, and die forgings for aircraft structural components. 7075 is used for manufacturing aircraft structural components, as well as high stress structural components with high strength and strong corrosion resistance, and mold manufacturing.
6061 vs 7075 Aluminum
Composition difference
In the 6061 specification aluminum alloy, aluminum alloy element accounts for 97.9%, magnesium element accounts for 1%, silicon element accounts for 0.6%, and 0.28% copper and 0.2% chromium are added. The composition of 7075 aluminum alloy roughly includes 5.6-6.1% of zinc, 1.2-1.6% of magnesium, copper, less than half a percentage point, silicon, iron, manganese, titanium, chromium, and other metals. It usually produces several levels of hot temper, 7075-O, 7075-T67075-T651.
Hardness difference
6061 has a hardness of 90HB.
The hardness of 7075 can reach 150HB
Series differences
6061 belongs to the 6000 series aluminum alloy
7075 belongs to the 7000 series aluminum alloy and is a zinc magnesium aluminum alloy.
Differences in mechanical performance
Aluminum alloy yield strength, shear force, tension
Yield (Shear) (Tensile)
6065 7KSI 10KSI 13KSI
7075 15KSI 22KSI 33KSI
Aluminum alloy code: Yield, Shear, Tensile
6061 7KSI 10KSI 13KSI
7075 15KSI 22KSI 33KSI
6061-T6 31KSI 17KSI 35KSI
7075– T6 73KSI 48KSI 83KSI
Usage difference
6061 material can be used in various places where aluminum alloy materials are not required due to price issues. 7075 and 7005 are usually used in commercial applications such as aerospace, which require high hardness and low density. Therefore, 7075 is also commonly used as a commercial aluminum alloy.
Price difference
In sheet form, 6061 typically costs $2-4/lb while 7075 will be $3-6/lb, up to 50% more expensive. As extruded or machined parts, the price difference may narrow, with 7075 costing 10-30% more than an equivalent 6061 component.
6061 vs 7075 Aluminum
- Density – 7075 aluminum has a density of around 2.8 g/cm3, while steel is around 7.8 g/cm3. So aluminum is significantly lighter than steel.
- Strength – While high-strength steels can rival 7075 aluminum in yield strength, the alloy generally has higher strength-to-weight properties, making it stronger for its weight.
- Corrosion Resistance – Aluminum corrosion resistance is better than carbon steels, though some high-alloy steels may be comparable. 7075 needs proper seals/coatings for corrosion-prone environments.
- Machinability – Steel machines much easier than 7075 aluminum due to aluminum’s work-hardening nature. It requires frequent tool changes and proper machining parameters.
- Weldability – In general, steel is easier to weld than 7075 aluminum which requires specific filler alloys and heat treatments to prevent cracking during welding and afterward.
- Cost – 7075 aluminum typically costs 2-3 times as much per pound as common structural steels like A36, due to material and processing costs.
- Applications – Due to its high strength-to-weight, 7075 is often used in aerospace where weight is critical, and some military vehicles. Steel continues to be common for buildings, machinery, vehicles.