What Influence Will High Speed Machining Technology Of Mold Have On Aluminum Alloy Die Casting
With the engineering application of HSM (high-speed machining technology) in the early 1990s, especially the continuous deepening of China’s research on high-speed machining technology in recent ten years, and the continuous research on high-speed machining machine tools, high-speed machining tools and tool handles, high-speed machining technology and CAD / CAM software, high-speed machining technology has been more and more applied to the machining and manufacturing of precision and complex molds, The technological process of aluminum alloy die casting is getting shorter and shorter, so it can be proofed and shipped faster. In this guide, we detail what influence will high speed machining technology of mold have on aluminum alloy die casting.
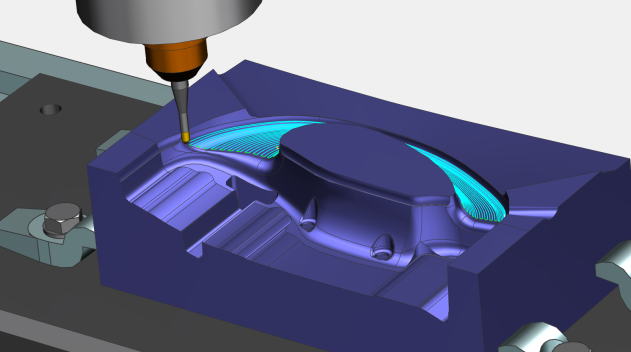
What Influence Will High Speed Machining Technology Of Mold Have On Aluminum Alloy Die Casting
Precision and complex molds have higher precision requirements and particularly complex geometry. In the traditional mold processing technology, the processing cycle is long and the production efficiency is low. The precision machining of hardened molds usually adopts EDM and fitter polishing, so the order of an aluminum alloy die-casting order also inevitably has a long cycle. In order to shorten the mold manufacturing cycle and improve the mold quality, high-speed machining technology attracts attention in the mold manufacturing process. It uses the high speed and high feed speed of machine tools to bring positive effects to the technical and process innovation of precision and complex mold manufacturing, and has been rapidly popularized.
(1) High speed machining technology is applied to die rough machining and semi finishing, which greatly improves the metal removal rate.
(2) During mold manufacturing, high-speed cutting machine tools, high-speed machining tools and processes can be used for quenching and hardening. For small molds, after heat treatment, they can be clamped for rough and finish machining at one time. For large and medium-sized molds, roughing and semi finishing can be carried out before heat treatment, and hardening and finishing can be carried out after heat treatment.
(3) High speed and high precision hardening machining can replace the commonly used processes such as EDM and fitter polishing in traditional mold manufacturing, and can improve the efficiency by more than 50% compared with traditional EDM.
(4) The use of high-speed machining technology and hardening process can significantly improve the surface quality and shape accuracy, realize the surface finish of machining, and the surface is particularly bright. It can be said that milling instead of grinding and turning instead of grinding have been realized to a certain extent. For molds with complex surfaces, its advantages have been obviously displayed.
(5) Adopting high-speed machining technology can eliminate decarburization, burns and microcracks caused by traditional EDM and grinding, greatly reduce the surface damage after die finishing, and improve the service life of the die by more than 20%.
(6) During high-speed machining, the workpiece has less heating, less cutting force, less thermal deformation, and the quality of the die is stable and significantly improved. Even if local EDM is needed, high-speed machining technology and CAD / CAM technology can also be used to improve the accuracy of electrodes, manufacture high-precision electrodes with complex shape and thin-wall deformation, and change the characteristics of poor quality of traditional EDM.