While the type of plastic material used plays a crucial role in determining the ultimate strength of the final product, several other factors also influence the overall strength and durability of 3D printed parts. Understanding these factors is essential for optimizing the printing process to create parts with the required mechanical properties. In this section, we will discuss three main factors that impact the tensile strength of 3D printed plastics: print temperature, print orientation, and fill pattern.
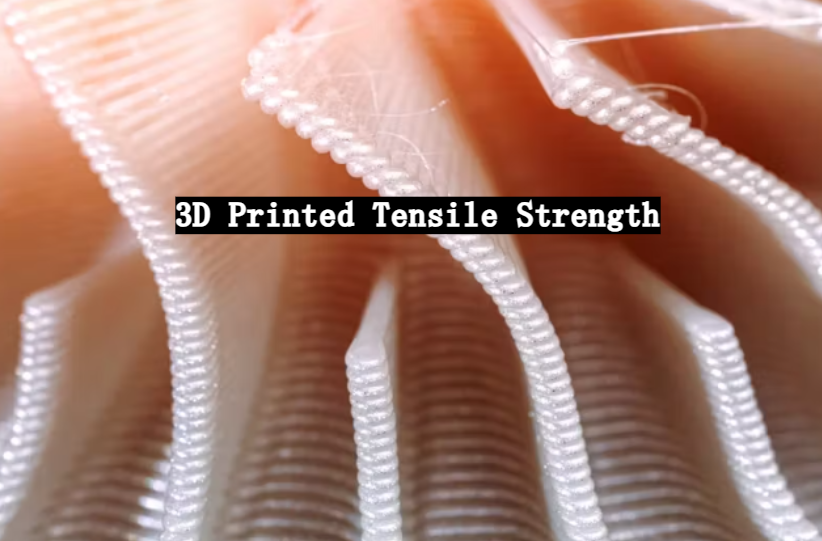
Factors That Impact 3D Printed Tensile Strength
1. Print Temperature
The selection of print temperature can greatly impact the strength of 3D printed plastic parts. The optimal temperature varies depending on the type of plastic used, and finding the right setting is crucial for achieving solid layer bonding and maximizing defect minimization.
If the print temperature is too low, the plastic filament will not melt sufficiently to form robust bonds between layers. Low temperatures can cause layers to delaminate or parts to fracture easily under pressure. If the temperature is too high, the plastic will melt too quickly, leading to drooling from the nozzle tip and stringing. The deposited filament also takes longer to cool, which can cause warping of the printed part.
To find the best print temperature for a particular material, refer to the instructions provided by your filament brand manufacturer. Another way is to perform a temperature tower test, which involves printing a vertical tower with each section printed at a different temperature. This experiment allows you to observe differences in layer adhesion, surface quality, and overall strength. Comparing the results can help determine the ideal print temperature for the filament, which will maximize part strength and durability.
2. Layer Height and Line Width
Layer height, also called layer thickness, refers to the vertical distance between each printed layer. This setting selected in the slicer software directly impacts the overall strength, surface finish, and print time of the printed part.
Smaller layer heights generally produce smoother surface quality and finer detail parts but increase print time. Larger layer heights print faster since the nozzle has fewer total layers to deposit, but result in rougher surface finish less suitable for small features or details.
In terms of strength, parts printed with smaller layer heights typically exhibit better layer bonding and are thus stronger and more durable. Generally, a layer height corresponding to 25-75% of the nozzle diameter is recommended.
Line width relates to the nozzle diameter and also influences strength. Wider lines (>nozzle diameter) can provide stronger parts as there is more plastic bonding each layer, but lower resolution. Narrower lines produce finer detailed parts with higher dimensional accuracy but possibly lack the same level of strength. The key is finding the right balance between layer height, line thickness, and print time for best strength results in your specific application.
3. Fill Pattern and Density
Another important consideration when discussing the strength of 3D printed plastics is the fill pattern and fill density. Parts are typically not solid but instead contain an internal lattice structure to save material and maximize weight reduction. Fill refers to the internal structure of empty space within printed parts, which can consist of repeated grid-like patterns. Generally, the fill provides support and strength to the outer shells of parts. Fill patterns and density can be adjusted in slicer software to control part weight, strength, and material usage.
There are various fill patterns to choose from, each with unique characteristics. More complex patterns like honeycomb or body-conforming geometries provide greater strength and deformation resistance due to their geometries but may take longer to print and use more material than simpler patterns like grids.
Fill density refers to the percentage of the part’s interior volume occupied by fill material. For example, a hollow part has 0% density while a solid part has 100% density. Higher densities lead to heavier and stronger parts but also increase material usage and print time. Conversely, lower densities reduce material and time but risk producing more brittle parts prone to fracture or deformation. Fill density also influences the modulus and elongation properties of prints.
Careful consideration of fill pattern and density is crucial for achieving the required strength and durability in 3D printed plastic parts. Optimizing for your specific application by selecting appropriate patterns and densities allows maximizing part strength, weight, and material efficiency.
How To Increase 3D Printed Tensile Strength?
While the inherent characteristics of different polymer types play an important role in determining tensile strength of 3D printed parts, other techniques can be employed to enhance the mechanical properties of these parts. These methods help overcome limitations of the 3D printing process and produce parts with higher strength, durability, and resistance to stresses. In this section, we will explore techniques that can be used to improve the strength of 3D printed plastic parts: annealing, coating, and fiber reinforcement.
Annealing
Annealing is a common heat treatment process used in traditional manufacturing to improve the mechanical properties of materials, including plastics. In 3D printing, annealing involves heating the printed part to near its glass transition temperature (but below its melting point). At this temperature, the material has not melted or lost its structure but softens, allowing the internal structure to reorganize, relieve residual stresses, and increase its strength, stiffness, and dimensional stability.
The steps for annealing 3D printed plastic parts include:
- Placing the part in a temperature-controlled oven or chamber.
- Setting the temperature between the material’s glass transition temperature and melting point. Specific temperatures and hold times depend on the plastic type used.
- Heating for 30 minutes to an hour then gradually cooling back to room temperature.
Annealing may cause some dimensional changes to parts so consideration of these changes should be made in the design process. 100% infill assists with maintaining dimensional accuracy. Requirements also vary between materials, so researching specifics of the material used is important to determine optimal annealing conditions.
Coatings
Applying coatings in 3D printing can also increase the ultimate strength of plastic end parts. This process involves depositing a protective shell or coating onto the printed part’s surface to effectively shield it from external stresses and boost overall durability.
Various materials can be used for coating 3D printed parts including epoxy resins, polyurethane coatings, and thermoplastic films. Coating material selection depends on the specific application and performance required. Generally, coating processes include:
Preparing the coating according to manufacturer instructions.
- Applying the material to coat the surface of the 3D printed part, ensuring complete and even coverage. This can be achieved through brushing, spraying, or dipping.
- Allowing the encapsulating material to cure or harden under manufacturer-recommended time and conditions.
- Applying coatings not only strengthens 3D printed part mechanics but provides other benefits like enhanced chemical resistance, improved UV protection, and better abrasion resistance. Be sure coatings are compatible with the 3D printing material before application.
Fiber Reinforcement
Rather than a technique, fiber reinforcement is more like a class of materials that integrates high-strength fibers like carbon or glass into a polymer matrix to enhance printed part mechanical properties. Adding these fibers enables composite materials with exceptional strength, stiffness, and durability for demanding applications. Ultimately, fiber reinforcement materials can produce parts on par mechanically with traditional manufacturing methods.
There are two main approaches fiber reinforcement can benefit FDM 3D printing:
Composite filaments: These are specialty filaments composed of fiber-reinforced plastic matrices specifically designed for printing. Parts produced with these fine fibers exhibit higher mechanical performance than those made with standard (or pure) plastic filaments alone. Popular composite filaments include carbon fiber-reinforced PLA, ABS, and PETG.
Continuous fiber reinforcement: This method involves directly laying continuous fibers within the printed part during the printing process. Specialized 3D printers are designed to handle continuous fibers, placing them along deposited plastic filament to fabricate parts with outstanding strength and rigidity. This technique is more complex requiring dedicated equipment but can produce parts matching performance of conventional manufacturing.
Fiber reinforcement is an effective way to boost strength, durability, and stress resistance of 3D printed plastic parts. Not all desktop 3D printers can handle fiber-reinforced 3D printing filaments or require hardened steel nozzles to withstand abrasion from fill materials.