With the continuous development of the machinery manufacturing industry, the requirements for the quality of gray cast iron parts are getting higher and higher. When processing gray cast iron parts, the surface brightness, smoothness and flatness of form and location tolerance are the most basic guarantees of processing quality; And the processing efficiency also determines the competitiveness of the auto parts industry. Using NC lathe to process gray cast iron parts can improve processing efficiency, and selecting correct tool materials can ensure the quality requirements of gray cast iron.
The following is a brief introduction to the characteristics of gray cast iron and how to select NC tool materials to process gray cast iron parts to obtain higher processing quality.
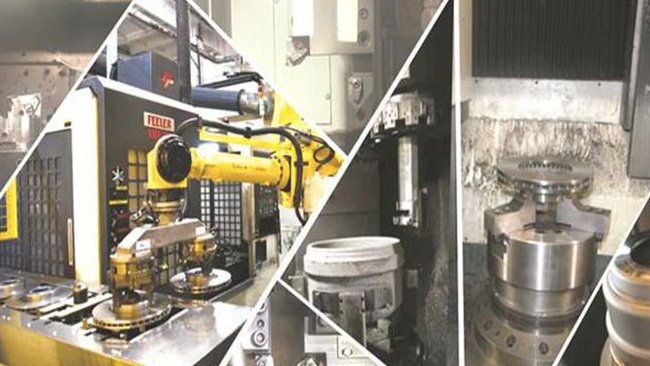
Characteristics of Grey Cast Iron
Grey cast iron refers to the cast iron with flake graphite, which is mainly composed of iron, carbon, silicon, manganese, sulfur and phosphorus. It is the most widely used cast iron, and its output accounts for more than 80% of the total output of cast iron. Grey cast iron is also known as gray cast iron, and its graphite is in strip shape.
Performance characteristics of gray cast iron material:
(1) Poor strength performance;
(2) Hardness characteristics: In cast iron, the ratio of Brinell hardness to tensile strength is very dispersed. For the same hardness, there is a range of tensile strength. Similarly, when the strength is the same, the hardness also has a range, which is because the strength performance is greatly affected by graphite, while the hardness basically reflects the matrix situation;
(3) Low notch sensitivity;
(4) Good shock absorption;
(5) Good antifriction.
And because of its low price and simple production process, gray iron is still widely used in brake disc, brake drum, flywheel and other auto parts, as well as motor housing (base) and motor end cover in the motor industry; Air conditioning compressor parts; As well as automobile gearbox, cylinder block, machine tool guide rail cutting.
How to Select NC Tool to Process Gray Cast Iron
At present, CNC tools for processing gray cast iron include carbide tools, ceramic tools and cubic boron nitride tools (CBN tools).
(1) Cemented carbide tools: Cemented carbide tools are often used, such as YG6 and YG6X. When machining gray cast iron, because cemented carbide is sensitive to linear speed, the higher the linear speed, the lower the tool durability, resulting in high tool change frequency, which ultimately affects the processing efficiency and increases the tool cost (it is more economical to select cemented carbide tools in small batches);
(2) Ceramic tools: Although the hardness of ceramic tools is higher than that of cemented carbide tools, due to the high brittleness, the white structure is easy to crack when encountering hard spots. For investment castings or gray iron castings with uniform allowance size, ceramic tools can be selected;
(3) Cubic boron nitride NC tool: The hardness of cubic boron nitride tool is higher than that of cemented carbide tool and ceramic tool. Due to its brittleness as that of ceramic tool, it can only process gray cast iron with small feed and small knife depth. Later, with the continuous research and practice of our tool engineers, the non-metallic adhesive cubic boron nitride NC tool BN-S300 was finally developed. Compared with the traditional CBN tool, it has increased toughness. It not only has high hardness, good wear resistance, and strong impact resistance toughness, but also can achieve high-speed cutting while ensuring the accuracy requirements of the workpiece. When encountering hard spots, white microstructure does not need to be annealed first, and can directly process the workpiece without tool breakage.
Another finish turning gray cast iron tool BNK30, due to its low friction coefficient, excellent high-temperature thermal stability and wear resistance, can easily process the surface roughness of Ra1.6 when the cutting speed is several times higher than that of cemented carbide. At the same time, the tool life is dozens of times that of cemented carbide tools, and the surface brightness is increased by an order of magnitude.
Application of Cubic Boron Nitride Blade in Grey Iron Parts
The integral cubic boron nitride blade BN-S300 material rough turning gray iron part brake disc has stable performance, and its service life is N times longer than that of the cemented carbide tool.
The cubic boron nitride tool BNK30 and the blade model WNGA080408/12 are used to finish turning the brake drum of gray iron parts. The advantage is that the surface roughness is within Ra1.6, and the single edge life of the tool is 70% longer than that of a CBN tool of a certain brand.
Fine milling engine cylinder block with cubic boron nitride blade BN-S300 brand has significantly improved productivity and stable cutting performance, which can take the advantage of replacing international first-class brands such as Shangao tools.
Remark: The structure of BNK30 CBN tools includes integral type and inlaid type. According to the machining allowance (processing procedure) of the brake disc, BNK30 tools with different structures are used to ensure a longer tool life and a higher surface finish (within Ra1.6).
(1) BNK30 brand integrated CBN blade needs to be equipped with Valin super hard special machine tool holder;
(2) The cutter bar of BNK30 inlaid CBN blade and the cutter bar of carbide indexable blade are common, and can be used by direct clamping;
(3) Before selecting CBN tools, tool matching is very important. In order to achieve high-speed cutting and reduce cost and increase efficiency, good communication is very important.