What Causes Tool Wear & How To Reduce Tool Wear In Aluminum Die Casting
When CNC processes aluminum alloy die castings and mold blanks, the tools are worn, and the excessively worn tools can only be discarded, which prolongs the service life of the tools and reduces the cost of the aluminum alloy die casting in a disguised way. The coating technology will be adopted for the current cutting tools to further improve the service life of the cutting tools and significantly improve the machining efficiency. In this article, we introduce the causes of tool wear and how to reduce tool wear for aluminum die casting.
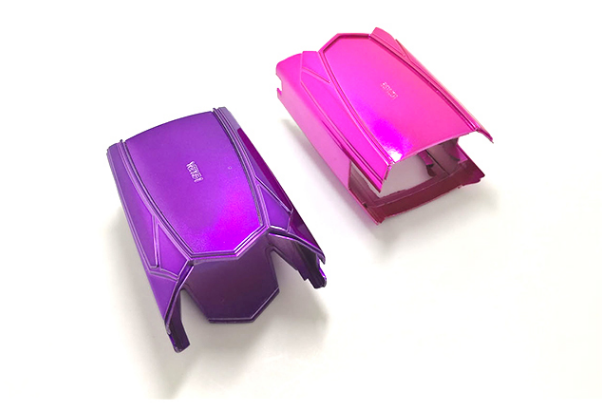
Tool Wear Types
Tool wear usually includes the following types:
① Flank wear
② Scoring wear
③ Crater wear
④ Blunt cutting edge
⑤ Cutting edge collapse
⑥ Cutting edge crack
⑦ Catastrophic failure
What Causes Tool Wear
In the metal cutting of aluminum alloy die castings or mold blanks, the heat and friction are the manifestations of energy. The high surface load and the heat and friction generated by the high-speed sliding of chips along the tool rake face make the tool in a very challenging machining environment. The cutting force often fluctuates up and down, which mainly depends on different machining conditions. Therefore, in order to maintain its strength at high cutting temperature, the tool is required to have some basic characteristics, including excellent toughness, wear resistance and high hardness.
How To Reduce Tool Wear & Prolong Tool Life
There is no generally accepted unified definition of tool life, which usually depends on different workpiece and tool materials and different cutting processes. One way to quantitatively analyze the end point of tool life is to set an acceptable maximum flank wear limit.
The continuous development of optimal tool substrate, coating and cutting edge preparation technology is very important to limit tool wear and resist cutting high temperature. These factors, together with the chip breaking groove and corner arc radius adopted on the indexable blade, determine the applicability of each tool to different workpieces and machining. The best combination of all these elements can reduce tool wear & prolong the tool life and make the cutting process more economical and reliable.