What Causes Sand Hole In Zinc Alloy Die Casting Surface And How To Fix & Prevent | Diecastng-mould
In the process of die casting production, the quality problem of sand holes on the surface of zinc alloy die casting often occurs. Many simple reasons sometimes have a great impact on the consequences, and the damage is large. In this article, we discuss what causes sand hole in zinc alloy die casting surface and how to fix them.
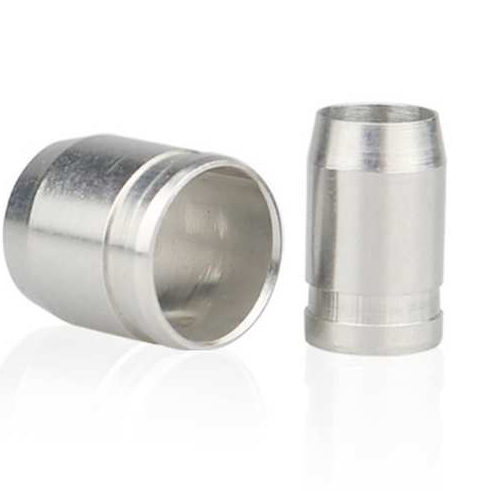
Causes & Solutions To Sand Hole In Zinc Alloy Die Casting Surface
1. General Sand Hole
In the whole process of zinc die casting production, sand holes on the surface of zinc alloy die casting are produced for various reasons. The main characteristics of sand holes are different regular precipitation sand holes due to different reasons.
The causes of sand holes on the surface of zinc alloy die casting are as follows:
– The melting time of the alloy is too long and the heat preservation is too long, which leads to the aggravation of inspiratory oxidation.
– The alloy material is polluted and moistened, resulting in H2O entering the charge.
– The cleaning agent itself gets wet and enters into the alloy liquid.
– The returned material has been seriously corroded and the surface has changed to Al (OH) 3.
– Improper stirring in the melting process results in more gas entering into the alloy liquid.
– There is too much h in all gold ingots.
In view of the above reasons, the following countermeasures can be taken to prevent:
– Before alloy melting, the furnace must be baked, and the moisture that can enter the alloy liquid in the furnace must be completely removed to prevent the increase of (H).
– All tools in contact with the alloy liquid must be baked. The coating agent shall be painted evenly and dried.
– The alloy material should be well protected from rain and moisture to prevent a large amount of Al (OH) 3 from accumulating on the surface.
– Control the raw materials and strictly control the gas content in the alloy ingot.
– Strictly control all kinds of greasy dirt into the alloy to prevent (H) from increasing.
– In the degassing process of alloy refining, attention should be paid to stable mixing, and the slag remover should be kept moisture-proof at ordinary times to prevent the increase of steam.
2. Immersion Sand Hole
The following is the reason analysis of sand hole on the surface of immersion zinc alloy die casting:
– The mold cavity wall contains volatile substances
– There is incomplete volatilized water and release agent on the surface of the inner wall of the mold cavity, which will emit white gas when filling the alloy liquid in the die casting, and there is no place to go, so it will be immersed in the casting.
– Leakage of mould.
Prevention to sand holes on the surface of immersion zinc alloy die casting:
– The release agent should be used properly and evenly, without local excess and volatilization.
– Blow evenly and thoroughly without residual liquid on the surface of the cavity.
– The cooling water must not leak into the mold cavity.
3. Involved Sand Hole
Defect characteristics: in the process of zinc alloy pouring, injection and filling, the gas is involved or contained in the liquid aluminum alloy. With the filling process, the alloy still has vortex splashing and so on, and the gas can not be eliminated, resulting in the gas in the alloy remaining in the casting with solidification to form sand holes. The inner wall of the sand holes is smooth, but not smooth, with obvious traces of pollution or corrosion, Sometimes it even has a peculiar smell. What’s more, sometimes it can be seen that there are oil stains (punch oil) in this hole, showing dispersion distribution.
Discovery method: appearance inspection after machining or X-ray.
Cause analysis of sand holes on the surface of involved zinc alloy die casting:
– Improper setting of gating system.
– The gate is too thin.
– The material pipe is too large and the filling rate is too low.
– The impact is too severe.
– The gate opening direction is wrong.
– Vortex aggravation.
– Improper setting of exhaust system.
– Poor exhaust.
– The overflow tank and exhaust tank are unreasonable.
– The vacuum channel is not smooth.
– Excessive amount of punch oil causes combustion after pouring alloy, resulting in a large amount of smoke.
– The filling speed is too fast, resulting in a large amount of gas involved, or blocking the exhaust channel too early.
– The vacuum system leaks, and the vacuum effect is reduced, because the gas in the high-speed filling cavity cannot be discharged.
– Machining allowance is too large.
– The gas in the deep cavity cannot be discharged.
Preventive measures:
– Change the direction of liquid metal into the cavity, and fill the deep cavity first.
– Reduce the injection speed properly.
– Under the condition of ensuring good filling, the larger the section at the entrance of the ingate, the better.
– The position of the exhaust groove should not be blocked by the alloy liquid flowing into the mold cavity first, or the overflow groove should be added appropriately. The deep cavity of the external vacuum casting can be inlaid with a mold to facilitate the gas discharge.
– Properly reduce the amount of punch oil to reduce the occurrence of gas in the feed pipe.
– Increase the charge rate.
– Use the vacuum device correctly without air leakage.
– Reduce machining allowance.
The above points are the causes and solutions of sand holes on the surface of zinc alloy die casting. Hope it will be helpful to you. In short, the surface defects of die casting parts are also one of the common problems in the manufacturing process. In addition to the reasonable design from the pressing mold, the quality control in the manufacturing process is also a very important link, because it is more appropriate to find problems early than to mend them later.