The pinhole is a type of defect that is easy to happen in aluminum die casting and has a certain impact on the quality of castings. Here we’ll introduce the causes of pinholes in aluminum castings and how to avoid or prevent pinhole defects in casting.
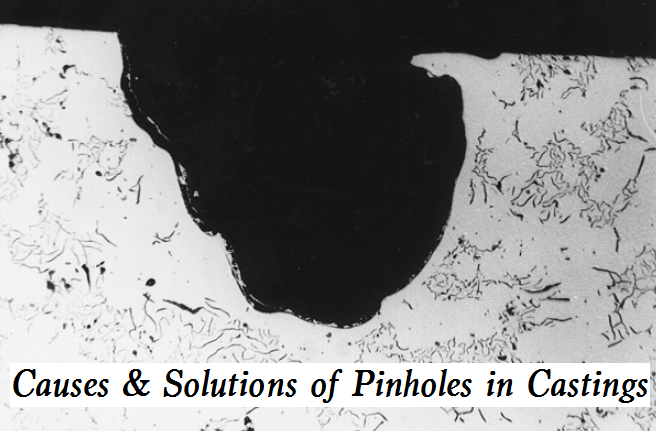
What Are Pinholes in Aluminum Castings
Due to the serious oxidation and gas absorption tendency of aluminum alloy, and the direct contact with furnace gas or the outside atmosphere during smelting, if the control is slightly improper during smelting, the aluminum alloy will easily absorb gas and form pores, the most common being pinholes. Pinholes usually refer to precipitation pores less than 1mm in the casting, which are mostly circular and unevenly distributed on the whole section of the casting, especially in the thick section of the casting and the part with a low cooling rate. The main gas component of the air hole formed in aluminum alloy due to gas absorption is hydrogen, and its occurrence has no certain rule to follow, usually, all or most castings in one heat have pinholes; Materials are no exception. All kinds of aluminum alloys are prone to pinholes. Pinholes reduce the actual stress area of the component and may become a source of cracks, and destroy the continuity of the material, reducing the strength and plasticity of the casting. Pinholes also affect the corrosion resistance and anodizing performance.
Causes of Pinholes in Aluminum Alloy Castings
Aluminum alloy can absorb a large amount of hydrogen during smelting and pouring, and continuously precipitate due to the decrease of solubility when cooling. The solubility of more hydrogen dissolved in the aluminum alloy increases with the increase in the temperature of the alloy liquid and decreases with the decrease of the temperature. When the liquid is transformed into a solid, the solubility of hydrogen in aluminum alloy decreases by 19 times. Therefore, during the cooling and solidification process of aluminum alloy liquid, at a certain time, the hydrogen content exceeds its solubility, which means that the hydrogen is precipitated in the form of bubbles. The hydrogen bubbles formed due to the precipitation of supersaturated hydrogen can not float up and discharge in time, so they form small and dispersed pores during the solidification process, which are commonly referred to as pinholes. The supersaturation reached before the formation of hydrogen bubbles is a function of the number of hydrogen bubble nucleation, while oxides and other inclusions play the role of bubble core.
Under general production conditions, especially in thick sand castings, it is difficult to avoid pinholes. Pinholes in castings are especially serious when aluminum alloys are melted and poured into an atmosphere with high relative humidity. Generally speaking, for aluminum alloys, if the crystallization temperature range is large, the probability of producing reticulated pinholes is much greater. This is because, under general casting production conditions, castings have a wide solidification temperature range, which makes aluminum alloys easy to form developed dendritic crystals. At the later stage of solidification, the residual aluminum liquid in the dendrite crystal gap may be isolated from each other and exist in a small space that is approximately closed. Because they are less affected by the external atmospheric pressure and the static pressure of the alloy liquid, when the residual aluminum liquid further cools and shrinks, a certain degree of vacuum can be formed (that is, the feeding channel is blocked), so that the supersaturated hydrogen in the alloy can be separated to form a pinhole.
Methods of Preventing Pinholes in Aluminum Alloy Castings
1) Strictly control the quality of furnace charge:
– All furnace materials shall be stored in a dry warehouse.
– The pouring and riser, waste castings, and other blocks shall be free from water and oil contamination.
– The returned materials shall not exceed 50% of the total weight of the furnace materials.
– The severely corroded furnace materials shall not be put into the furnace.
2) Strictly control the quality of main auxiliary materials:
– The incoming materials shall be analyzed, and unqualified materials should not be used.
– Chlorine shall be dried with calcium chloride, and the calcium chloride shall be changed every half month.
– When magnesium blocks are added in front of the furnace, they shall be preheated before being added.
3) Prepare the furnace and melting tools:
– All tools entering the furnace must be coated and baked before use.
– The coated crucible should be thoroughly dried (orange-red) before pouring aluminum water.
– The good plate of the furnace must seal the flame and prevent it from contacting with the molten aluminum.
4) Strictly control smelting operation:
– The distance from the lower end of the nitrogen (or chlorine pipe) to the bottom of the crucible is 100~150 mm.
– The refining time is guaranteed to be 8-10 minutes.
– After refining, let the alloy liquid stand for about 5 minutes, and then slag.
5) Reasonable selection of smelting process parameters:
– The smelting time shall be as short as possible, which should not exceed 1 hour and 40~50 minutes for ZL108 alloy.
– The casting time after refining shall be shortened to no more than 1 hour.
– The refining temperature ZL110 is about 720-740 ℃, and ZL108 is about 700-720 ℃.
– Chlorine or chlorine pressure is appropriate when the alloy liquid boils but does not fly out of the crucible.
– The alloy at the bottom of the crucible should not be cast.