What Causes Blackening Of Die Castings And How To Solve Them - Reasons For Die Casting Blackening
In the usual casting process, there are occasional blackening of die casting parts. Why is this? Here in this article, aiming at the phenomenon of blackening of die casting parts, we detail the reasons for blackening of die casting parts and discuss the influencing factors and solutions for blackening of die castings.
The followings are the reasons for the blackening of die castings:
The Surface Blackening Of Die Castings
Aluminum, zinc and magnesium die casting alloys are all active metal. In a dry environment, they will slowly oxidize, and will be easily oxidized and corroded under higher temperature or humidity conditions. This is determined by the characteristics of the alloy itself. After the surface of the die casting is oxidized, its color will become dull, even black or moldy.
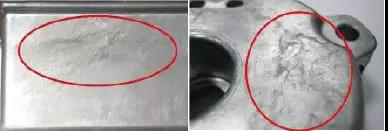
1. Oil fume like blackening on the surface
The oil fume like blackening on the surface of the die casting is shown in the picture. On the surface of the die casting, it seems that there are black clouds of smoke. The black shape is irregular and the depth is uneven. This is because in the process of filling the cavity with the alloy liquid, after the release agent or punch oil meets the high temperature alloy liquid, the combustion is not sufficient, and a large amount of oil fume is gathered in the cavity. The smoke can not be fully and quickly removed from the cavity. The accumulated oil fume pollutes the surface of the alloy liquid and the mold cavity, causing blackening like oil fume on the surface of the die casting part.
2. Black spots
There will be black spots on die castings. The size of the spot is different, and the shape is nearly round. The dark spot is darker in color. This is caused by the black particles formed by the release agent or punch oil. Each black particle individually causes the surface of the casting to become black on the surface of the mold or die castings.
3. Oxidation and blackening on the surface
The blackened surface of the die casting can be caused by oxidation. There is a trace of release agent on the surface of the casting, and the color will become darker and black after natural oxidation in the atmosphere. The atmosphere containing moisture, a large amount of moisture in the air deposits on the surface of the casting, and the hot and humid moisture will quickly oxidize the entire casting. However, good packaging can prevent the surface of the casting from oxidizing and blackening.
4. Carbon deposit marks formed on the surface
Carbon deposit marks are caused by carbon accumulating on the surface of the mold, which is rough and like traces of sticking to the mold. Generally, there is no sign of tension on the mold. If quality of the release agent or punch oil is improperly selected, or the release agent is not pure, the wax and organic grease in the release agent are easy to burn, and the burned residue carbon black will gather and adhere to the surface of the mold, forming carbon deposits. The carbon deposit appears on the surface of the mold and is a layer of dark black dirt.
5. Molding and blackening
The punch oil on the material cake exploded and sprayed on the surface of the casting at the moment of mold opening, forming the yellow spot. Blackening caused by oxidation appears on the die casting after it encounters moist moisture. The casting has been exposed to rain and weather for a long time. Rust occurs after the casting is seriously oxidized and molded.
6. Oil stains
The oil stains on the conveyor belt which transports the castings contaminate the castings, causing the castings to turn black. If the storage box, working platform for storing the castings and tools, the trimming die for trimming and the gloves used for operation are stained with dirt and oil, they will also contaminate the castings and cause the surface of the castings to become black. After the fine machining process, the die casting is washed, but the water is not dry. After the casting is oxidized, blackened and rusted, there will cause surface oxidation and blackening of die castings by the negative residue of the finishing coolant. If the packaging carton is damp and absorbed, it will also cause mold due to the contact between the casting and the damp carton.
Causes & Solutions For The Blackening Of Die Castings – Measures To Blackening Of Die Casting Parts
1. Excessive amount of sprayed punch oil
If there is too much oil in the punch in the injection chamber, a large amount of flame, oil fumes and carbon black will be produced when the punch oil encounters the poured high temperature alloy liquid. These flames,oil fumes and carbon black will not only promote the oxidation of the alloy liquid, but also contaminate the alloy liquid and the cavity wall. Therefore, it is necessary to reduce the amount of punch oil. The amount of punch oil depends on whether or not outer circle of the material cake is black. The black color should only be on one side of the punch.
If the punch oil produces too much and too thick oil fumes, the oil fume will flow into the cavity from the inner gate and adhere to the cavity near the inner gate, causing the surface of the casting near the inner gate to appear black spots.
2. The spraying amount of the release agent is too much or the proportion is too thick
If the release agent is over accumulated after the die casting cavity is sprayed, or the concentration of the release agent is too high, organic substances such as the oil, grease, wax and organic silicone oil and moisture in the release agent will generate a large amount of oil fume after encountering the high temperature alloy liquid. Excessive oil fume not only seriously pollutes the alloy liquid and the surface of the mold cavity, but also rapidly oxidizes the injected alloy liquid, causing black spots, blackening and carbon deposits on the surface and inside of the casting. Therefore, it is necessary to choose a mold release agent that has a good effect on preventing sticking to the mold, high temperature resistance, being not easy to burn and generate oil fumes. Using a release agent with a lighter concentration can also reduce oil fumes. Generally, the ratio of mold release agent is about 1:120 to 150.
3. Excessive moisture residue of the release agent on the surface of the mold cavity
Moisture of the mold release agent in the mold cavity is not wiped or volatilized, and excessive moisture remains on the surface of the mold. The moisture will decompose into oxygen , hydrogen and HO-ions when encountering high temperature alloy liquid. Oxygen oxidizes and contaminates the alloy liquid, causing the surface layer of the casting to oxidize and turn black. If the surface temperature of the mold is higher than 160 ℃, the moisture will evaporate faster. Therefore, it is necessary to appropriately increase the mold temperature of the parts that are far away from the inner gate and the mold temperature in the part where the temperature is too low.
After spraying the release agent, accurately and thoroughly blow the moisture of the release agent on the surface of the mold. Excessive release agent should be blown with compressed air. The moisture on the parting surface of the mold should also be blown with an blowing pipe. We should not only prevent the moisture on the parting surface from flowing into the cavity, but also prevent excessive moisture on the parting surface from blocking the parting surface and the exhaust groove, affecting the effect of exhaust.
4. Gating systems and mold structure
Although the die casting process can solve some casting defects, most of the casting defects still need to be resolved by improving the mold when the process is normally adjusted. The gating system and mold structure will directly cause the casting to blacken. Generally, the surface of the die casting parts being away from the inner gate, with eddy currents, in the deep cavity of the mold and at the final filling are prone to blackening.
Solution: Improving the gating system of the mold and changing the position, size and direction of the inner gate and overflow groove can change the flow direction and flow of the alloy liquid, and change the generation, flow direction and discharge of oil fumes. After the mold is modified in this way, the blackening of the surface of the heat sink on both sides of the casting is eliminated, and the alloy liquid directly fills the heat sink on the side of the casting.
5. Die casting alloy materials
Most die casting alloys are aluminum alloys that are easily oxidized, especially at high temperatures. During the pouring process and the moment of die casting filling, the die casting alloys will be oxidized and the defects of oxidation and slag inclusions will appear. If aluminum alloy die castings are stored in a humid environment, rust defects will appear on their surfaces in a few days. The dense oxide layer formed during the die casting high temperature demolding of the casting is worn after the shot blasting process, which will make the surface oxidize faster and seriously.
Die casting alloys with different chemical composition have different oxidation resistance. Therefore, the degree of blackening on the surface of castings made of different grades of alloys is different. Therefore, a die casting alloy that is not easy to be oxidized and blackened can be used.
6. The surface of the die casting part becomes black and discolored after being shot blasted
The stainless steel shot should be regularly selected and dust removed. This is because after a period of use, the steel shot will be worn and the aluminum oxide dust will adhere to the surface of the steel shot. When the shot is hitting the die casting, it will also hit the alumina dust on the surface of the casting, causing the overall color of the casting surface to darken or become mat.
7. Poor die castings cause blackening, bubbles and peeling in electroplating treatment
Defects such as cracks, porosity, shrinkage holes, pores, bubbles, pinholes, cold shuts and flow marks can’t appear on the surface of die castings, otherwise the surface of the castings will easily bubble and the plating layer will separate from the substrate after electroplating. In the solidification process, a dense chilled layer is formed on the surface of the die casting due to rapid cooling, and the internal structure may have defects such as pores and shrinkage holes. If this good surface layer is removed during grinding, pitting, bubbles and other defects will appear during electroplating. The polishing wheel should not be pressed too tightly when the die cast part is polished. The casting should not be overheated to prevent the abrasive from sticking to the casting, causing the product to fail to be electroplated and appear black or peeling.
8. Methods of removing the blackened surface of die castings
A 100% full inspection is carried out for the blackening of the surface of the castings. After finding individual blackened castings, they can be polished by a polishing machine or hands by using a scouring pad. For oil stains and mildew stains on castings, the most effective way is to use die-cast aluminum alloy mildew stain cleaning agent to thoroughly clean the oil stains and mildew stains at one time. After the casting is cleaned, passivation treatment should be carried out immediately to form a passivation film on the surface of the aluminum alloy casting to achieve the purpose of anti corrosion and anti bacteria.
9. Surface coating treatments for preventing oxidation of die castings
The commonly used surface coating methods for die castings are as follows:
(1) Painting.
(2) Anodizing can prevent aluminum alloy from continuously oxidize.
(3) Porcelain anodic oxidation has beautiful surfaces, high hardness and good decoration.
(4) Micro-arc oxidation has advantages of high hardness and good corrosion resistance, and has disadvantages of rough surfaces and poor appearance.
(5) Hard oxidation has features of high hardness, wear resistance, ugly gray colors.
(6) Electroplating.
(7) Chemical oxidation.
(8) Organic coatings and plastic spraying.
(9) Physical vapor deposition or the PVD treatment has good effect.
(10) Ceramic coatings have high costs.