FAW has completed the 7+2+N product process platform layout, with seven major blank manufacturing processes, including green sand, resin sand, gravity metal molds, low-pressure metal molds, low-pressure core assembly, high-pressure casting and forging, as well as parts finishing, overall It has completed product manufacturing capabilities, and at the same time completed a variety of new process research and development reserves in terms of forward-looking materials, processes and products. In the future, it will focus on transforming and upgrading research and development of new energy products, lightweight products, and assembly products. The following are the types of R&D products.
1. Seat frame (cast magnesium)
Material: Magnesium alloy AZ91
Features: Magnesium alloy integrated castings are used to replace the separate parts stamped and welded on the original steel plates to achieve component integration and lightweighting; meet the safety performance of the entire vehicle and achieve a 30% weight reduction.
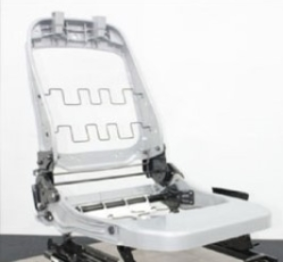
2. Subframe (cast aluminum)
Material: Aluminum alloy A356.2
Features: Based on the large hollow structure, it achieves an overall uniform wall thickness of 4mm and an ultimate breakthrough of 3.5mm in some areas. Compared with the original “casting + profile welding” structure, the weight is reduced by 10%.
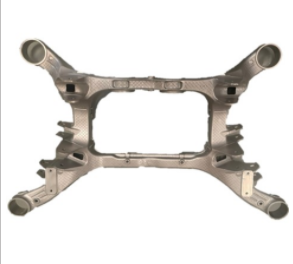
3. Motor housing (cast aluminum)
Material: Aluminum alloy A356.2
Features: Integrated reducer housing, the wall thickness of the reducer housing is 3.5mm, the side wall has an integrated spiral water jacket with a thickness of 6.5mm, the bottom of the housing is inlaid with a bearing bushing, and the low-pressure core assembly process is used to meet the needs of high internal quality and high efficiency. Sealing requirements.
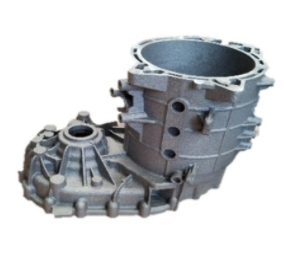
4. Instrument panel sub-panel frame (cast magnesium)
Material: Magnesium alloy AZ91
Features: The casting has a complex structure and a basic wall thickness of 2.5mm. The riveting and thread clamping processes are used to achieve no mechanical processing in most areas of the casting, improving the accuracy of interior assembly.
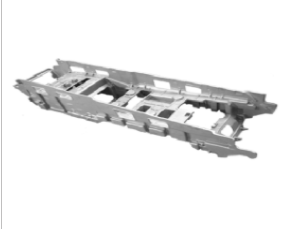
5. Passenger car shock tower (cast aluminum)
Material: Aluminum alloy AlSi10MnMg
Features: Using high vacuum die-casting technology, the thinnest wall thickness is 2.5mm. The casting can be heat treated to greatly improve the mechanical performance.
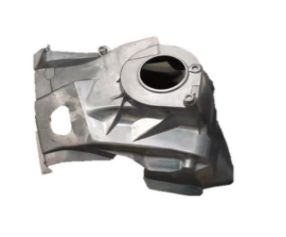
6. Passenger car steering knuckle (cast aluminum)
Material: Aluminum alloy A356.2
Features: Using squeeze casting and process optimization, the mechanical properties are higher than low pressure and differential pressure casting, improving the safety performance of the vehicle chassis.
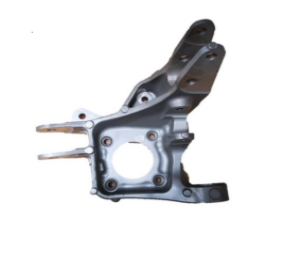
7. Gearbox middle shell (cast magnesium)
Material: Magnesium alloy AZ91 Features: The passenger car gearbox housing is developed using magnesium alloy high-pressure casting. Compared with aluminum alloy castings, the weight is reduced by 33.5%, and the material creep strength is ≥50MPa.
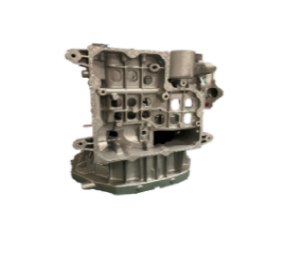