What Are The Requirements For Secondary Spinning Of Stainless Steel & Aluminum Alloy?
Stainless steel and aluminum alloy are the most used materials among all metal materials. From materials to finished products, in addition to spinning, stamping, stretching, bending, rounding and other forming processes, subsequent processes such as polishing, punching, laser cutting, welding, secondary turning and milling are also carried out for secondary processing. Different metal products have different requirements for secondary processing.
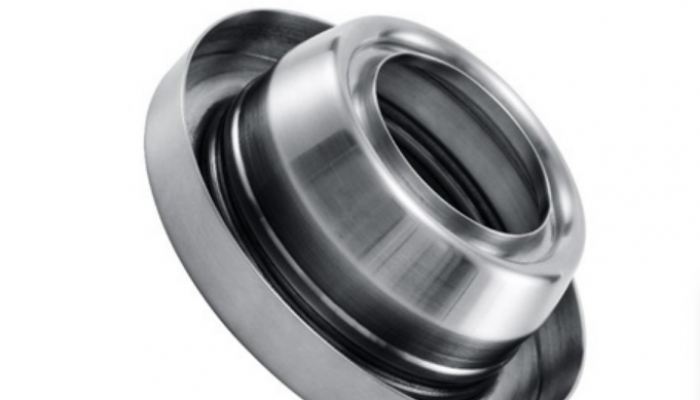
Stainless Steel Spinning Products
Surface requirements: general wire drawing or mirror polishing
Stainless steel spinning products often need wire drawing or mirror polishing. The surface texture of the blank of NC spinning products is thicker than that of stamping and stretching, and the cost of polishing is slightly higher than that of stretching and punching (except for cone and special-shaped rotating parts). Controlling spinning lines can effectively control the cost of polishing, and strong spinning can make the surface of spinning products smoother.
Secondary processing: punching, turning and milling, laser processing, welding
After spinning, the size of stainless steel spinning products will be different from the designed size due to stress rebound. Tooling positioning is required during secondary processing. If holes are allowed at the bottom, the center hole at the bottom can be used as the secondary positioning center for product processing, and the accuracy is more accurate than that of other positions as tooling positions; If turning and milling processing is required, in addition to considering the tooling position, we should also consider how to strengthen the local rigidity of thin-walled parts, otherwise it is easy to cause vibration in the processing process and make the cutter particles collapse; If laser cutting is required, the impact of stress release rebound of stainless steel during cutting on laser cutting needs to be considered. There are mainly two aspects that can be improved: using fixtures to avoid stress rebound and displacement, and changing the cutting sequence, cutting from the position with the best rigidity of the product structure.
Aluminum Alloy Apinning Products
Surface requirements: generally oxidation or painting
Aluminum spinning can use a calendering knife to calender the surface effect of spinning products, and the finished products will be smoother than stamping and stretching. The spinning surface treated by the calender does not need to be polished and can be directly sprayed with powder, which can cover the fine lines on the surface. Similarly, the spinning surface treated by calendering knife can be sandblasted and oxidized without wire drawing, but fine sand needs wire drawing. When polishing oxidized aluminum spinning products, nylon wheels need to be used for final polishing, so as to get a better oxidized surface. Profiled products should not be treated with calendering knife.
Secondary processing: punching, turning and milling, laser processing, welding
Because the hardness of aluminum is lower than that of stainless steel, the turning and milling of aluminum alloy spinning products is easier than that of stainless steel, but the laser processing of aluminum alloy is more difficult than that of stainless steel, because aluminum and copper are easy to produce reflection in laser cutting, and the cutting surface will be worse than that of stainless steel, and the welding performance of aluminum is also worse than that of stainless steel. Therefore, if it is not necessary, the welding and laser cutting processes of aluminum alloy spinning products should be minimized to prevent product deformation.
Whether it is stainless steel or aluminum alloy, the production of each spinning product is jointly completed by multiple processing procedures. How to ensure that the products still have good shape consistency and accuracy after many times of processing is a problem that the processing manufacturers need to seriously consider, which depends on the processing experience and technical strength of the manufacturers.