What Are The Reasons For The Moldy And Blackening Of Zinc Alloy Die Casting
Zinc alloy is widely used in bathroom, bags, shoes and clothing accessories due to its convenient forming, strong plasticity, low cost and high processing efficiency. The color degree of zinc alloy is slightly lower than that of stainless steel, but the strength and rust resistance of zinc alloy are good. Many complex die castings are mostly made of zinc alloy. In the process of zinc alloy die casting, because zinc is an active metal and easy to oxidize, it is often moldy and black, so how to deal with with such problems? Read on this guide and we briefly introduce the causes of moldy and blackening in zinc alloy die casting.
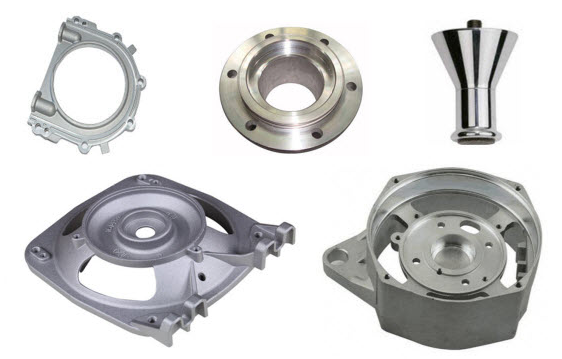
What Are Reasons For The Blackening Of Zinc Die casting
1. External environmental factors. Zinc is a kind of active metal, which is easily oxidized to black or mildew under certain temperature and humidity conditions, which is determined by the characteristics of aluminum itself.
2. Then there are internal factors. After the die casting and machining processes, many manufacturers do not do any cleaning treatment, or simply flush with water, which can not be completely cleaned. There are corrosive substances such as release agent, cutting fluid, saponification fluid and other stains on the surface of zinc die casting, which speed up the mildew growth of zinc die casting.
3. The process design is unreasonable. Improper treatment of zinc alloy die castings after cleaning or pressure inspection creates conditions for mould formation of zinc alloy die castings and accelerates the formation of mould.
4. Improper selection of cleaning agent. Cleaning has strong corrosiveness, resulting in corrosion and oxidation of die casting zinc.
5. Warehouse management is not in place. The mildewing condition is different when the storage height is different.
Solutions To Moldy & Blackening Of Zinc Die Casting
1. Consider from the material die casting: if the material die casting is not good, there are many loose holes, so that the liquid medicine will be stored in the electroplating process, when the electroplating is finished, the stored liquid medicine will slowly seep out, leading to white spots, which is the so-called mildew. At this time, it is required that the pH of the pretreatment liquid medicine such as dewaxing water should not be too high, and the ultrasonic power should not be too high.
2. The filling and leveling of acid copper is better: when the material of zinc alloy is slightly poor, we need the filling and leveling of acid copper, which can fill out some small holes.
3. Before adding acid copper, the base copper must have enough thickness to prevent the erosion of acid copper solution. If necessary, coke copper can be added for insurance.
4. The sulfur content of bright nickel is lower and the decomposition products are less.
5. Chromium plating should be in good position, without cracks.
6. Wash thoroughly after chromium plating.
7. Dry well after chromium plating and keep the oven clean.
8. The storage environment should keep a certain degree of dryness.