There are many types of tool steel used to make plastic molds and casting molds. The selection of mold steel is important considering the precision and quality requirements in the production. Now let’s go through 10 types of mold steels and their applications.
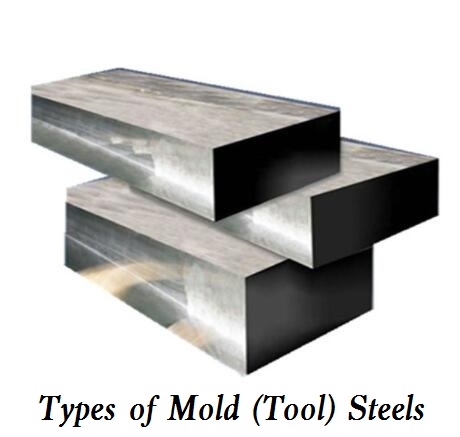
Types of Mold (Tool) Steels - Mold Steel Introduction and Selection
1. NAK55 Steel
The hardness value of NAK55 is 37 to 43HRC, without heat treatment, with high hardness, good wear resistance and pressure resistance, uniform hardness, and good machinability. It is suitable for high-precision mold processing, and is often used to manufacture high-precision mirror mold, such as cameras, cosmetic instruments,s or transparent covers, and is suitable for PMMA, PC, PS, and other plastics.
2. NAK80 Steel
Pre-hardened plastic mold steel, with a hardness of 32~43HRC, has good polishing and sculpting properties, and good discharge processing properties. It is often used in mirror polishing molds, such as anti-dust, TV filter plates, cosmetic boxes or precision wrinkle processing molds, etc. This material does not need heat treatment and has good polishing, cutting, and etching properties. It is suitable for ABS, GPPS, PS, PC, ABC, AS, and other plastics.
3. 718H Steel
718H material is pre-hardened plastic mold steel, which does not need hardening and tempering treatment. It is often used in large long-life plastic injection molds, such as household electrical parts and computer shells, and its working life is longer than that of ordinary P20 steel. It has good polishing, formability, and processability is widely used in injection mold, air-blowing mold, and extrusion mold, and is applicable to plastics such as PA, PS, PE, PP, and ABS.
4. P20 Steel
P20 material is one of the most commonly used plastic mold steels, with a hardness value of 28~32HRC. It can be electrically etched and has good polishing performance. It is often used for toy molds and is suitable for PP, PE, and other plastics.
5. S136 Steel
The hardness value of S136 material is 290-300HB. It has excellent corrosion resistance, polishing properties, and processability. No heat treatment is required. It is suitable for making molds used in weak acid and humid environments. It is especially suitable for high-yield transparent plastic parts molds, such as CD discs and optical instruments. When using transparent materials, can be preferred. It is suitable for PVC, PP, EP, PC, PMMA, and other materials. This kind of material is suitable for all kinds of plastic parts molds, especially for molds with special requirements.
6. 420SS Steel
420SS material is stainless steel, with high hardness, good polishing and corrosion resistance, and a hardness value of 30-33HRC. It is often used for transparent plastic parts, which are easy to rub and burn, and is not suitable for inserts. It is suitable for mold templates in mass production.
7. H13 Steel
H13 material contains a large amount of tungsten and has a high-temperature resistance. It is suitable for alloy die-casting mold materials, such as aluminum, magnesium, zinc, and copper alloy die-casting dies, and is often used for tool die manufacturing.
8. 8407 Steel
8407 material is chromium, molybdenum, and vanadium alloy tool steel, which is better than the general H13 material and has good fatigue strength and thermal stress fatigue performance. It is commonly used in die-casting dies, forging dies and extrusion dies.
9. S7 Steel
S7 material is made of chrome-molybdenum alloy, with high impact resistance and toughness, and good processing and heat treatment. It is suitable for impact tools and plastic molds for hot and cold work.
10. M300 Steel
M300 material is easy to be processed and polish after heat treatment, with a chromium content of up to 16%. It has excellent corrosion resistance and is very suitable for PVC material. It can be polished into a mirror. It is applicable to plastic molds, transparent plastic products, or molds that are in contact with all chemicals.
Generally, the materials used in the mold are divided into the hard mold and soft mold. The so-called hard mold means that the materials used in the mold core parts need to undergo heat treatment, such as quenching and carburizing. This kind of mold is called hard mold, and the commonly used materials include H13, 420, S7, etc. Soft mold refers to the mold whose internal mold parts can meet the design requirements without heat treatment. Common materials include P20, 420H, NAK80, and beryllium copper.